Rotating a hydraulic pump is a common operation that many businesses need to perform on a regular basis. However, if you don’t know how to rotate a pump, there’s a good chance that someone else in your organization does. In this article, we’ll teach you the basics of rotating a pump and provide some tips on how to do it safely and effectively.
Before you can rotate a hydraulic pump, you’ll first need to determine its orientation. This is usually done by inserting a rod into the drive shaft and rotating it until the pump’s impeller blades are pointing in the correct direction. Once you’ve determined the orientation, you can start the rotation process by turning the motor’s rotor.
When rotating a pump, it’s important to keep in mind a few key safety tips. First and foremost, always wear protective gear (such as gloves) when rotating a pump. Second, make sure that the area around the pump is well-lit and free from hazards (like sharp objects). Finally, never work on a pump if you’re impaired by alcohol or drugs.
If you follow these safety tips, rotating a pump should be easy and safe for you to do.
What is a hydraulic pump?
A hydraulic pump is a machine that uses the power of hydraulics to move fluid. In many cases, a hydraulic pump is used in conjunction with a motor to turn a shaft. This can be useful in a variety of applications, including manufacturing, agriculture, and construction.
How is rotation controlled on a hydraulic pump?
Rotational control of a hydraulic pump is accomplished by using a governor or pressure regulator. The governor regulates the flow of fluid by adjusting the pressure applied to the pistons. This pressure determines the speed at which the pistons will rotate.
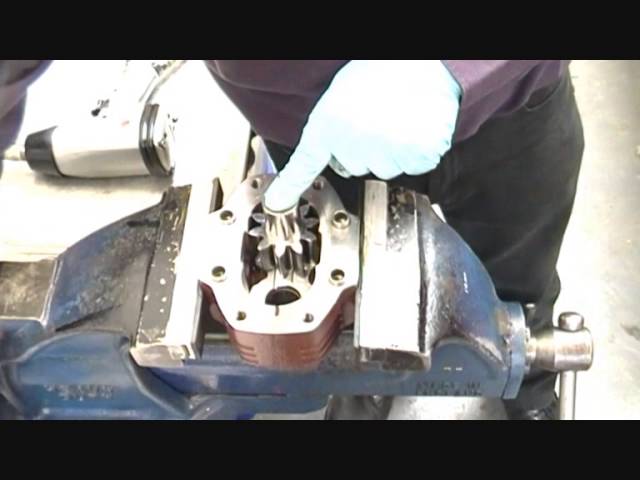
How does a hydraulic pump work?
A hydraulic pump is a device that uses pressurized fluid to move objects or materials. It works by using a hydraulic motor to turn a shaft, which in turn moves the pump’s pistons. These pistons pressurize the fluid inside the pump and cause it to move the object or material it’s attached to.
What is a Rotational Hydraulic Pump?
A rotational hydraulic pump is a type of pump that uses a rotating shaft to move the fluid through the pump. This type of pump is most commonly used in industrial settings, where it is necessary to move large quantities of fluid quickly and efficiently.
Rotational hydraulic pumps are typically divided into two main categories: impulse and continuous. Impulse pumps are used for short-term applications, such as moving fluid between storage tanks and processing plants. Continuous pumps, on the other hand, are typically used for longer-term applications, such as moving fluid in pipelines.
Both types of pumps have their own advantages and disadvantages. Impulse pumps are faster than continuous pumps, but they typically require more energy to operate. Continuous pumps are more durable than impulse pumps, but they can be slower to work
What are the different types of rotating pumps?
The different types of rotating pumps are centrifugal, rotary and axial. Centrifugal pumps are the most common type and use a series of discs or buckets to move fluid. Rotary pumps use a set of rotating metal blades to move fluid. Axial pumps move fluid along an axis by using a series of vanes or paddles.
Why should you change rotation on a hydraulic pump?
A hydraulic pump is a type of engine that uses pressure to move fluid. This fluid can be oil, gas, water, or any other fluid that needs to be moved. The rotation of a hydraulic pump affects how the fluid moves through the engine. Changing the rotation of a hydraulic pump can improve its performance. Here are three reasons why you should change your pump’s rotation:
1) It can increase the efficiency of your engine. When the pump rotates at a different speed, it causes the pistons to move at a different rate which in turn causes more fuel and air to be injected into the engine. This leads to a higher performance and increased fuel efficiency.
2) It can reduce wear and tear on your engine. If your pump is rotating at the same speed as the engine, it will cause friction between the piston and cylinder walls. Over time this friction will cause damage to these areas which will then lead to an increased amount of wear and tear on your engine. By changing the rotation of your pump, you can reduce this friction and therefore decrease the amount of wear and tear on your engine.
3) It can improve your overall reliability of your engine
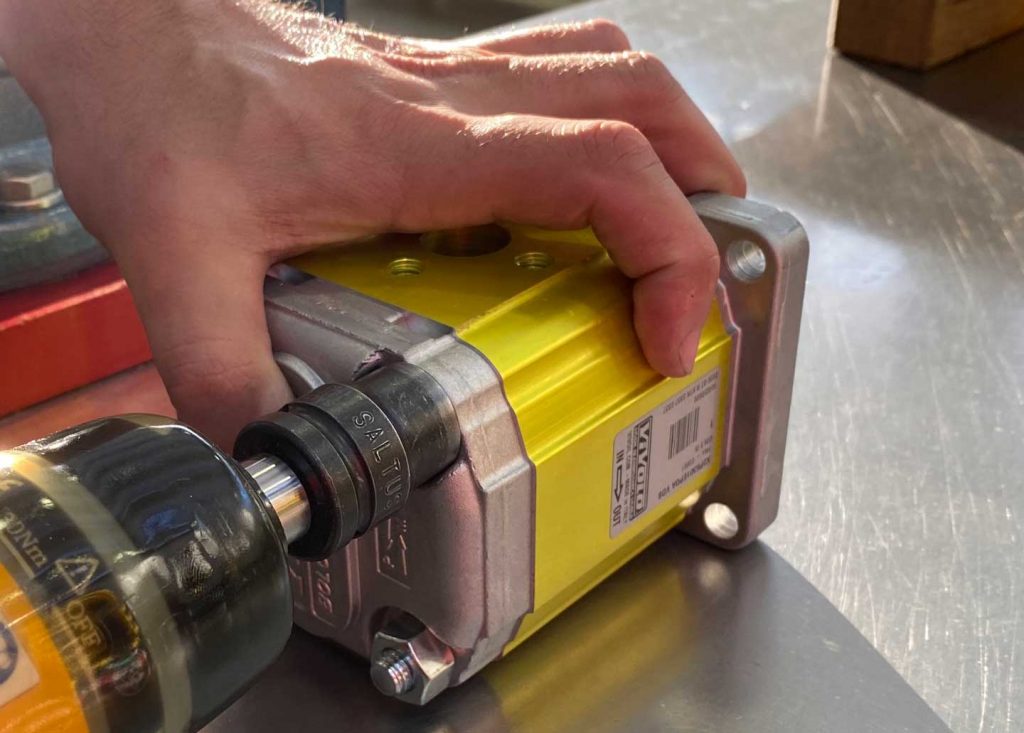
How to change rotation on a hydraulic pump?
A hydraulic pump is a commonly used machine that helps move fluids and products. Rotating the pump can help improve performance. Here are four ways to change rotation on a hydraulic pump:
1. Use a key or a screwdriver to turn the gear wheel.
2. Use a spanner to tighten or loosen the bolt that holds the gear wheel in place.
3. Turn the gear wheel with an Allen wrench.
4. Unscrew the gear wheel and remove it from the motor shaft.
Why Changing Rotation on a Hydraulic Pump is Difficult
When it comes to rotating a hydraulic pump, there are a few factors that must be considered. For one, the axis of rotation (the pipe that the pump is mounted on) must be perpendicular to the direction of flow. Additionally, the speed of the pump must be consistent with the speed of the fluid being pumped. Finally, any seals or gaskets that may be present on the pump must maintain their integrity under high pressure and temperature conditions.
Changing rotation on a hydraulic pump can often be difficult due to these factors. In some cases, it may be necessary to remove the entire pump assembly from its mounting location in order to make a change.
Conclusion
Yes, you can change the rotation on a hydraulic pump. Rotation changes the direction and speed of fluid flow through the pump. This can be useful in various settings, such as when you need to direct a spray or liquid from one location to another.
Can you change rotation on a hydraulic pump,please click topkitparts see more