In the industrial and commercial sectors, the efficiency and performance of machinery and equipment are critical to achieving productivity and meeting operational targets. Belts play a vital role in the functioning of machines, and their replacement is an inevitable aspect of maintenance. However, finding the right replacement belt can be a challenging and time-consuming task. That’s where Dayton belt cross-reference comes in as a quick and easy solution for belt replacement.
This guide will provide an overview of Dayton belts, their importance in various machines and equipment, and the challenges of finding the right replacement belt. It will also discuss the benefits of using Dayton belt cross-reference charts, factors to consider in cross-reference, steps involved in belt replacement, and tips for effective replacement. By the end of this guide, readers will have the knowledge and tools to find the right Dayton replacement belt quickly and easily, ensure optimal belt performance, and extend the life of their equipment.
Understanding Dayton Belts
Dayton belts are a type of power transmission belt used in various industrial and commercial machines and equipment. These belts are manufactured by Dayton, a subsidiary of Grainger, and are known for their durability and reliability. Dayton belts come in different types, including V-belts, timing belts, ribbed belts, and flat belts, each with unique features and advantages.
V-belts, also known as Vee belts, have a trapezoidal cross-section and are used in machines with high power transmission requirements, such as agricultural equipment, air compressors, and pumps. Timing belts, on the other hand, have teeth on the inner surface and are used in machines that require synchronous power transmission, such as automobiles, printers, and packaging machines.
Ribbed belts, also called multi-vee belts or micro-V belts, have a ribbed surface on the inner surface and are used in machines that require high-speed power transmission, such as washing machines, HVAC systems, and power tools. Flat belts, also known as conveyor belts, have a flat surface and are used in machines that require horizontal power transmission, such as conveyor systems, escalators, and treadmills.
It is important to select the right type of Dayton belt for optimal performance and safety. Using the wrong type of belt can result in equipment failure, safety hazards, and increased maintenance costs. Therefore, it is essential to identify the correct type of Dayton belt for each application.
Importance of Dayton Belt Cross Reference
When it comes to industrial and commercial machines and equipment, a broken or worn-out belt can quickly lead to costly downtime and lost productivity. Finding the right replacement belt can be a challenge, especially when dealing with outdated or missing part numbers, incorrect measurements, and unavailable products. This is where Dayton belt cross-reference charts come in handy.
A Dayton belt cross-reference chart is a tool used to simplify the process of finding the right replacement belt for a particular application. It allows users to quickly and easily identify the correct belt by comparing the specifications of the old belt with those of the new one. By using a cross-reference chart, users can avoid the risk of downtime, save money, and ensure optimal belt performance.
In addition to simplifying the replacement process, Dayton belt cross-reference charts are also valuable in situations where the original part number or manufacturer is unknown. By entering the dimensions and characteristics of the old belt, users can find a compatible Dayton replacement belt that meets the same specifications. This not only saves time but also ensures the machine or equipment continues to operate safely and efficiently.
Overall, Dayton belt cross-reference charts are a valuable resource for anyone looking to replace their Dayton belts quickly and easily. By providing a user-friendly tool that simplifies the process and ensures optimal performance, Dayton helps businesses save time and money while keeping their equipment running smoothly.
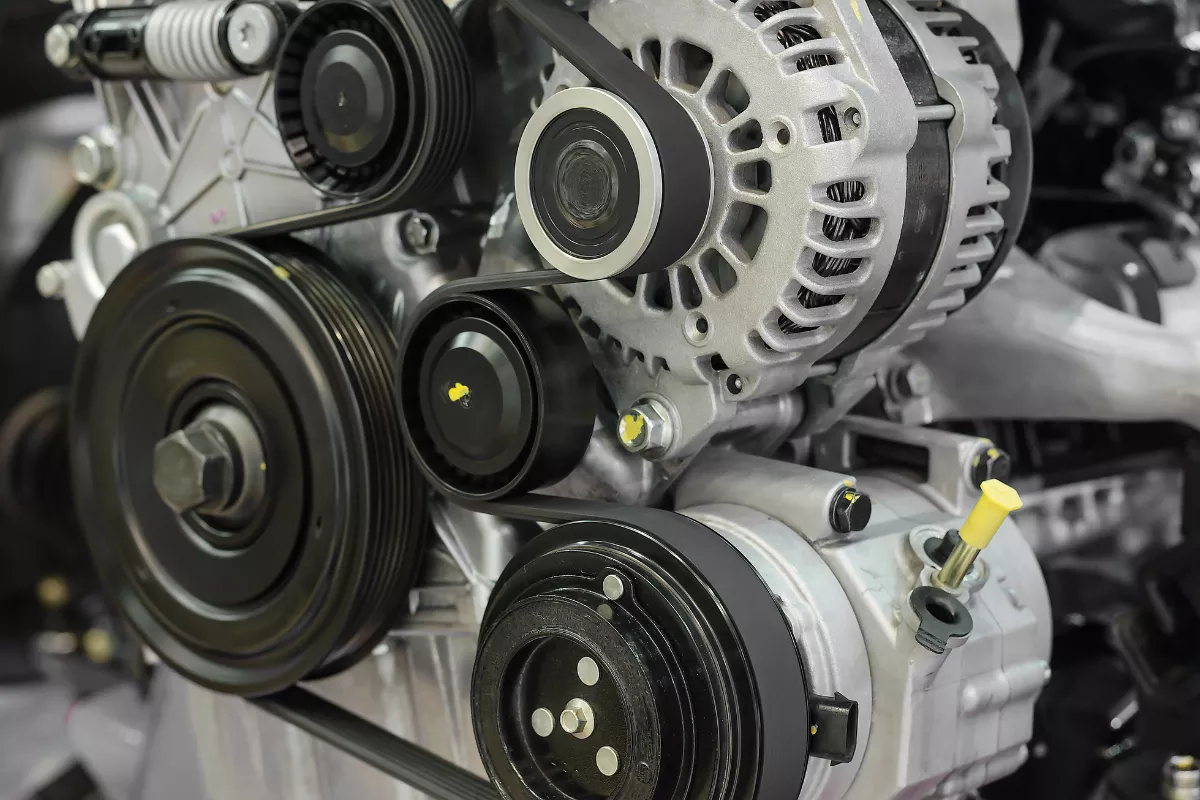
Factors to Consider in Dayton Belt Cross Reference
Before using a Dayton belt cross-reference chart, there are several factors to consider to ensure that you select the correct replacement belt for your application. Here are some essential factors to keep in mind:
- Belt type: Dayton belts come in various types, including V-belts, synchronous belts, and variable speed belts. Make sure you select the right type of belt for your application.
- Belt size: Belt size is a critical factor to consider when choosing a replacement belt. You should measure the old belt’s length, width, and thickness accurately and match it to the replacement belt’s size.
- Belt application: The belt application is also an essential factor to consider when selecting a replacement belt. The application determines the type of belt required, the material, and the tension required.
- Load capacity: The load capacity of a belt refers to the amount of weight it can handle without breaking. You should select a replacement belt that can handle the load capacity required by your application.
- Operating conditions: The operating conditions of the equipment also determine the type of belt required. Factors such as temperature, humidity, and exposure to chemicals or abrasives can affect the belt’s performance and lifespan.
By considering these factors, you can narrow down your search for the right Dayton replacement belt and increase the chances of selecting the correct belt for your application. However, to make sure that you have the right belt, you should also use a Dayton belt cross-reference chart.
Steps in Dayton Belt Replacement
Replacing a Dayton belt can seem like a daunting task, but with the right tools and knowledge, it can be done quickly and efficiently. Here are the steps involved in replacing a Dayton belt:
- Identify the old belt: The first step is to identify the old belt that needs to be replaced. This can be done by checking the part number, the size, or the type of the old belt.
- Select the new belt using a cross-reference chart: Once you have identified the old belt, you can use a Dayton belt cross-reference chart to find the correct replacement belt. The chart will provide you with the part number, size, and type of the new belt that is compatible with your machine.
- Remove the old belt: Before removing the old belt, make sure to turn off the machine and disconnect the power source. Loosen the tensioner and remove the old belt from the pulleys.
- Install the new belt: Install the new belt by threading it through the pulleys and tensioner. Make sure the belt is properly aligned and seated in the grooves of the pulleys.
- Adjust the tension: Adjust the tension of the new belt according to the manufacturer’s specifications. Over-tensioning or under-tensioning the belt can cause premature wear and failure.
- Test the belt: Turn on the machine and check the new belt for proper operation. Listen for any unusual sounds and check the tension again after a few hours of operation.
By following these steps, you can replace your Dayton belt quickly and easily, ensuring optimal performance and safety of your equipment.
Tips for Effective Dayton Belt Replacement
Replacing Dayton belts can be a challenging task, especially if you are not familiar with the process. However, by following a few tips, you can replace Dayton belts effectively and ensure optimal performance and safety. Here are some tips to help you replace your Dayton belts effectively:
- Inspect the Pulleys for Wear: Before installing a new Dayton belt, inspect the pulleys for any signs of wear, such as cracks, chips, or grooves. If the pulleys are worn, they can cause premature belt failure, slipping, or poor performance. Make sure to replace any worn pulleys before installing a new belt.
- Check the Tension and Alignment: It is essential to check the tension and alignment of the Dayton belt before and after installation. Improper tension or misalignment can cause belt slippage, premature wear, or equipment failure. Use a belt tension gauge to check the tension and adjust it as needed. Make sure the pulleys are aligned correctly to ensure even belt wear and longer belt life.
- Lubricate the Belt as Needed: Dayton belts require periodic lubrication to reduce friction and heat buildup. Use a high-quality belt lubricant to lubricate the belt as needed. Over-lubrication can cause belt slipping, so use only the recommended amount.
- Regular Maintenance: Dayton belts require regular maintenance to ensure optimal performance and safety. Check the belts regularly for signs of wear, damage, or misalignment. Replace any worn or damaged belts immediately to avoid equipment failure.
- Troubleshooting Common Problems: If you experience any problems with your Dayton belts, such as slipping, squeaking, or vibration, troubleshoot the problem immediately. Check the tension, alignment, and pulley condition to identify the cause of the problem. If you cannot troubleshoot the problem, seek professional help.
By following these tips, you can replace your Dayton belts effectively and ensure optimal performance and safety. Remember to perform regular maintenance and troubleshoot any problems immediately to avoid equipment failure and downtime.

In conclusion, the Dayton belt cross-reference chart is an essential tool that can simplify the process of finding the right Dayton replacement belt quickly and easily. The guide has provided an overview of the importance of Dayton belts, the challenges of finding the right replacement belt, and the benefits of using a cross-reference chart. It has also explained the factors to consider when using a Dayton belt cross-reference chart, the steps involved in replacing a Dayton belt, and some tips for effective replacement. By applying the knowledge gained from this guide, readers can ensure optimal belt performance and extend the life of their equipment. Therefore, we encourage readers to make use of the Dayton belt cross-reference chart to find the right replacement belt and keep their machines and equipment running smoothly.
Understanding the Gates Belt Cross Reference System: A Comprehensive Guide