Hydraulic pump pressure adjustment is a critical aspect of hydraulic systems used in industrial applications. The pressure adjustment of hydraulic pumps determines the system’s performance, energy efficiency, and reliability. A hydraulic system’s overall efficiency is directly proportional to the hydraulic pump’s pressure adjustment.In this article, we provide an overview of hydraulic pump pressure adjustment, its importance, and its effects on hydraulic system performance. We also cover the factors that affect hydraulic pump pressure adjustment, methods for adjusting hydraulic pump pressure, common mistakes to avoid, and recommended best practices.The purpose of this article is to provide readers with an understanding of hydraulic pump pressure adjustment and its impact on hydraulic system performance. This knowledge can help businesses optimize their hydraulic systems, improve performance, and reduce operating costs.
An Introduction to Rexroth Hydraulic Pump Adjustment Techniques
Understanding Hydraulic Pump Pressure Adjustment
Hydraulic pump pressure adjustment refers to the process of altering the pressure at which a hydraulic pump operates. This adjustment can be made in various ways, such as adjusting the pressure relief valve, modifying the hydraulic pump’s flow rate, or adjusting the pump displacement.
The components of a hydraulic pump pressure adjustment system include the pressure relief valve, which is responsible for regulating the maximum pressure of the hydraulic system, and the pressure control valve, which adjusts the pressure of the hydraulic fluid flowing through the system. Additionally, some hydraulic systems may incorporate sensors or other components to monitor and adjust hydraulic pump pressure automatically.
The hydraulic pump pressure adjustment process involves setting the pressure at which the hydraulic pump operates, which can affect the performance of the entire hydraulic system. A hydraulic system operating at the correct pressure will achieve optimal performance, while a system with incorrect pressure may experience reduced performance, increased energy consumption, and potential system failure.
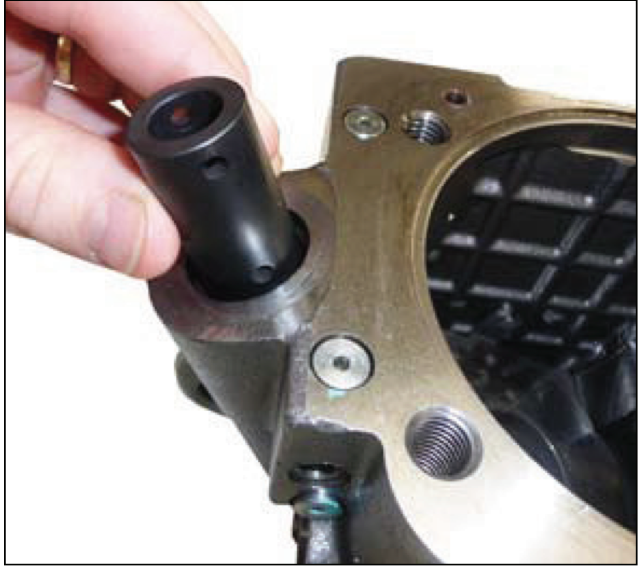
Importance of Proper Hydraulic Pump Pressure Adjustment
Hydraulic pump pressure adjustment is a critical factor in ensuring the optimal performance of hydraulic systems. Proper adjustment of the pump pressure can help to increase the efficiency of the system and reduce energy consumption, ultimately leading to cost savings.
Furthermore, proper hydraulic pump pressure adjustment can also have a significant impact on the performance of the machines or equipment that rely on hydraulic power. If the pressure is not adjusted correctly, the machine may not function as intended, leading to decreased performance, reduced productivity, and potentially costly downtime.
In addition to improving machine performance, proper hydraulic pump pressure adjustment can also help to extend the lifespan of hydraulic components. When the pressure is not adjusted correctly, it can cause excessive wear and tear on the system, leading to premature failure of components such as pumps, valves, and cylinders.
Overall, the importance of proper hydraulic pump pressure adjustment cannot be overstated. By ensuring that the pressure is correctly adjusted, businesses can optimize the performance of their hydraulic systems, improve machine performance, and reduce operating costs.
Factors Affecting Hydraulic Pump Pressure Adjustment
Hydraulic pump pressure adjustment is a critical aspect of hydraulic system optimization. However, there are several factors that can affect the effectiveness of the adjustment process. In this section, we will discuss the main factors that impact hydraulic pump pressure adjustment.
- Fluid Viscosity: The viscosity of the hydraulic fluid affects the pump’s ability to generate pressure. If the fluid is too viscous, it can reduce the pump’s flow rate, resulting in inadequate pressure. Conversely, if the fluid is too thin, it can cause the pump to cavitate, which can damage the system.
- System Load: The load on the hydraulic system affects the pressure requirements. If the system is overloaded, the pressure requirement will be higher, and the pump will have to work harder to maintain the desired pressure. If the load is too low, the pressure requirement will be lower, and the pump may be overworking, leading to premature wear and tear.
- Pump Type: The type of pump used in the system can also impact pressure adjustment. Different types of pumps have varying pressure capabilities, and some are better suited for high-pressure applications than others.
- Pump Size: The size of the pump determines the flow rate and the pressure that it can generate. If the pump is too small, it may not be able to meet the pressure requirements of the system. On the other hand, if the pump is too large, it may generate excessive pressure, which can lead to system damage.
- Operating Pressure Range: The operating pressure range of the system is another critical factor that affects hydraulic pump pressure adjustment. If the system pressure exceeds the pump’s maximum operating pressure, it can cause damage to the pump and the system. Conversely, if the pressure is too low, it can lead to system inefficiencies and poor performance.
- Temperature: The temperature of the hydraulic fluid can impact pump performance and pressure adjustment. If the fluid is too hot, it can cause the pump to overheat and lose efficiency. On the other hand, if the fluid is too cold, it can reduce the pump’s performance and pressure generation.
To optimize hydraulic pump pressure adjustment, it is essential to consider these factors and ensure that the system components are appropriately sized and rated to meet the pressure requirements. It is also critical to use high-quality hydraulic fluid and maintain the system to prevent issues such as contamination and fluid degradation.
Key Factors to Consider When Configuring Your Hydraulic Pump System
Methods for Adjusting Hydraulic Pump Pressure
There are several methods for adjusting hydraulic pump pressure, each with its own set of advantages and disadvantages. Here are some of the most common methods:
- Manual Adjustment: This method involves manually adjusting the pressure relief valve to achieve the desired pressure. It is a simple and cost-effective method, but requires frequent monitoring and adjustment to maintain the desired pressure.
- Spring Adjustment: This method involves adjusting the tension of the spring in the pressure relief valve to achieve the desired pressure. It is a relatively simple method and requires less monitoring compared to manual adjustment, but may be less precise.
- Pilot-Operated Relief Valve Adjustment: This method involves adjusting the pilot pressure that controls the relief valve. It provides more precise control over the pressure and can be used in more complex hydraulic systems.
- Proportional Relief Valve Adjustment: This method uses a proportional relief valve to adjust the pressure based on the system’s demand. It provides precise pressure control and can be used in systems with varying flow rates and loads.
- Load-Sensing Adjustment: This method uses a load-sensing pump and pressure compensator to adjust the pressure based on the system’s demand. It provides precise pressure control and can be used in systems with varying flow rates and loads, but requires a more complex hydraulic system.
Each method has its own set of advantages and disadvantages, and the best method for adjusting hydraulic pump pressure depends on the specific needs of the hydraulic system. It is important to consult with a hydraulic system expert to determine the most suitable method for a given application.
Common Mistakes in Hydraulic Pump Pressure Adjustment
Even with the best intentions, mistakes can happen during hydraulic pump pressure adjustment. These mistakes can cause a decrease in system performance and energy efficiency, as well as increase the risk of hydraulic system failure. Some of the most common mistakes made during hydraulic pump pressure adjustment include:
- Using incorrect hydraulic fluid: Using the wrong type or viscosity of hydraulic fluid can cause problems in the hydraulic system, including decreased performance and increased wear on system components. It is important to use the correct hydraulic fluid specified by the manufacturer.
- Not adjusting pressure to the correct level: If the hydraulic pump pressure is not adjusted to the correct level, the system may not perform as intended. This can result in decreased system performance and energy efficiency, and increased wear on system components.
- Neglecting to consider the load characteristics: The load characteristics of the system must be taken into account when adjusting hydraulic pump pressure. Failure to do so can lead to system inefficiencies and increased wear on system components.
- Overadjusting pressure: Overadjusting the hydraulic pump pressure can lead to system damage and decreased system performance. It is important to adjust the pressure to the recommended level specified by the manufacturer.
- Failing to properly maintain the hydraulic system: Poor maintenance can lead to issues with hydraulic pump pressure adjustment, such as leaks and system contamination. Regular maintenance can help prevent these issues from occurring.
- Improperly installing hydraulic components: If hydraulic components are not installed properly, it can cause issues with hydraulic pump pressure adjustment and overall system performance. It is important to follow the manufacturer’s instructions for installation.
- Not monitoring system performance after adjustment: After hydraulic pump pressure adjustment, it is important to monitor the system’s performance to ensure that it is functioning as intended. Failure to do so can lead to system failure and decreased efficiency.
To avoid these common mistakes, it is important to follow proper hydraulic pump pressure adjustment procedures and adhere to manufacturer recommendations. Regular maintenance and monitoring of system performance can also help prevent issues from occurring.
Hydraulic Pump Pressure Adjustment Best Practices
Proper hydraulic pump pressure adjustment is essential for the efficient operation of hydraulic systems. It is important to follow best practices to ensure optimal performance and longevity of the hydraulic system. Here are some best practices for hydraulic pump pressure adjustment:
- Follow Manufacturer’s Guidelines: It is important to follow the manufacturer’s guidelines for hydraulic pump pressure adjustment. Each hydraulic pump has its unique operating specifications, and deviating from them can result in inefficient operation or damage to the pump.
- Monitor System Pressure: It is essential to monitor the hydraulic system pressure during pump pressure adjustment. This allows for real-time adjustments to the pressure setting and ensures that the system operates within safe and efficient pressure ranges.
- Use Appropriate Tools: The use of appropriate tools during hydraulic pump pressure adjustment is critical. This ensures accurate pressure measurements and adjustments to the hydraulic system.
- Make Incremental Adjustments: It is recommended to make small incremental adjustments to the hydraulic pump pressure to avoid sudden changes in the system. Sudden changes can lead to system damage or failure.
- Conduct Periodic Checks: Regular checks of the hydraulic system pressure and pump pressure adjustment can identify any abnormalities or changes in the system. This allows for timely action and prevents potential system failures.
- Proper Maintenance: Proper maintenance of the hydraulic system is crucial for efficient operation and longevity. Regular maintenance can identify any issues with the hydraulic pump pressure adjustment and prevent costly repairs.
- Safety First: When performing hydraulic pump pressure adjustment, safety should always be the top priority. It is essential to follow safety guidelines and procedures to prevent any accidents or injuries.
By following these best practices for hydraulic pump pressure adjustment, businesses can optimize their hydraulic system’s performance and reduce downtime and repair costs. It is important to prioritize proper maintenance and safety to ensure optimal system performance.
Conclusion
In conclusion, proper hydraulic pump pressure adjustment is crucial for optimizing hydraulic system performance and energy efficiency. A well-adjusted hydraulic pump ensures that the hydraulic system operates smoothly and efficiently, which translates into improved machine performance and energy savings.
In this article, we discussed the definition and components of hydraulic pump pressure adjustment, as well as its importance and benefits in industrial applications. We also explored the factors affecting hydraulic pump pressure adjustment, the methods for adjusting hydraulic pump pressure, and common mistakes to avoid during the adjustment process. Additionally, we shared recommended best practices for successful hydraulic pump pressure adjustment and maintenance.
It is important to note that improper hydraulic pump pressure adjustment can lead to consequences such as decreased machine performance, increased energy consumption, and premature equipment failure. Therefore, businesses must prioritize proper hydraulic pump pressure adjustment and ensure that their systems are optimized for maximum efficiency and performance.
As technology continues to advance, we can expect to see future trends in hydraulic pump pressure adjustment that further improve system performance and energy efficiency. However, it is essential that businesses stay up-to-date with best practices and industry developments to remain competitive and efficient in their operations.
In conclusion, businesses should consider proper hydraulic pump pressure adjustment as a critical component of their hydraulic system optimization strategy. By following recommended best practices and avoiding common mistakes, businesses can improve machine performance, reduce energy consumption, and increase the longevity of their equipment.