Hydraulic systems are critical components in many industrial and manufacturing applications. The proper customization and optimization of hydraulic systems can lead to increased efficiency, productivity, and cost savings. One essential component of a hydraulic system is the hydraulic pump. The pressure compensated variable displacement pump is a type of hydraulic pump that offers unique benefits for hydraulic system customization.This article will provide an overview of pressure compensated variable displacement pumps, their components, and how they work. We will explore the benefits of incorporating these pumps into hydraulic systems, their applications, and considerations for installation, maintenance, and repair. Additionally, we will examine successful case studies of implementing pressure compensated variable displacement pumps in hydraulic systems. Finally, we will compare pressure compensated variable displacement pumps to other types of hydraulic pumps and discuss which type is better for specific hydraulic system applications.
Overall, the purpose of this article is to provide a comprehensive understanding of pressure compensated variable displacement pumps and their impact on hydraulic system customization. By the end of this article, readers will have a clear understanding of the benefits and considerations of incorporating pressure compensated variable displacement pumps into their hydraulic systems.
Understanding Pressure Compensated Variable Displacement Pump
A pressure compensated variable displacement pump is a type of hydraulic pump that is designed to deliver a specific flow rate of hydraulic fluid regardless of the load pressure. This means that as the load pressure changes, the pump will adjust the displacement of the pump to maintain a constant flow rate. The pump displacement can be adjusted either mechanically or electronically to accommodate a range of flow rates.
The components of a pressure compensated variable displacement pump typically include a swash plate, cylinder block, pistons, and a control system. The swash plate is responsible for converting the rotational motion of the pump’s input shaft into the linear motion of the pistons. The cylinder block houses the pistons and allows them to move up and down to pump the hydraulic fluid. The control system is responsible for adjusting the pump displacement based on the load pressure.
The basic operation of a pressure compensated variable displacement pump is as follows: hydraulic fluid is drawn into the pump through an inlet port and then flows into the cylinder block. The pistons inside the cylinder block then move up and down to pressurize the fluid and push it out of the outlet port. The control system monitors the load pressure and adjusts the pump displacement as needed to maintain a constant flow rate.
Overall, pressure compensated variable displacement pumps are an important component in many hydraulic systems, allowing for more efficient and flexible operation.

Benefits of Incorporating Pressure Compensated Variable Displacement Pump
A pressure compensated variable displacement pump offers several benefits to a hydraulic system. Here are some of the most significant benefits:
- Improved system efficiency with pressure compensation feature: One of the most important benefits of a pressure compensated variable displacement pump is its pressure compensation feature. This feature helps maintain a constant pressure level within the hydraulic system, regardless of changes in the load. As a result, the system can operate more efficiently, reducing energy waste and lowering operating costs.
- Flexibility in system design with variable displacement feature: Another significant benefit of the pressure compensated variable displacement pump is its variable displacement feature. This feature allows the pump to adjust its output based on the demands of the hydraulic system. It provides flexibility in system design, enabling the system to handle varying loads more effectively.
- Lower maintenance and operating costs: A pressure compensated variable displacement pump can help reduce maintenance and operating costs for a hydraulic system. The pressure compensation feature helps minimize energy waste and reduce wear and tear on the hydraulic components, which can extend the lifespan of the system. Additionally, the variable displacement feature enables the system to operate more efficiently, resulting in lower energy consumption and reduced operating costs over time.
In summary, incorporating a pressure compensated variable displacement pump in a hydraulic system can improve system efficiency, increase flexibility in system design, and reduce maintenance and operating costs. These benefits can ultimately lead to a more reliable and cost-effective hydraulic system.
Applications of Pressure Compensated Variable Displacement Pump
Pressure compensated variable displacement pumps are widely used in a variety of hydraulic system applications. These pumps provide excellent control over fluid flow and pressure, which makes them a popular choice for industries such as agriculture, construction, and manufacturing.
One of the key advantages of pressure compensated variable displacement pumps is their ability to be used in a wide range of applications. They are commonly used in hydraulic power units, injection molding machines, machine tools, and many other hydraulic systems. In addition, these pumps are often used in applications that require precise control over fluid flow and pressure, such as in the aerospace industry.
The benefits of using pressure compensated variable displacement pumps in hydraulic systems are numerous. For example, these pumps can help improve system efficiency by providing precise control over fluid flow and pressure, which can reduce energy consumption and improve overall system performance. Additionally, the variable displacement feature of these pumps allows for greater flexibility in system design, which can help reduce the overall size and weight of the hydraulic system.
Another key advantage of pressure compensated variable displacement pumps is their ability to operate under a wide range of conditions. These pumps are capable of operating at high pressures and temperatures, which makes them suitable for use in harsh environments. Additionally, the pressure compensation feature of these pumps helps ensure that the pump will continue to operate at a consistent pressure, even under varying load conditions.
Overall, pressure compensated variable displacement pumps are a versatile and reliable choice for many hydraulic system applications. Their ability to provide precise control over fluid flow and pressure, as well as their flexibility in system design, make them an attractive option for businesses looking to improve the performance and efficiency of their hydraulic systems.
Considerations for Incorporating Pressure Compensated Variable Displacement Pump
Before incorporating a pressure compensated variable displacement pump into a hydraulic system, there are several considerations that need to be taken into account to ensure successful integration and operation.
Pre-installation Considerations
One of the first considerations is the intended application of the hydraulic system. The pump should be selected based on the requirements of the system, such as flow rate and pressure. The type of hydraulic fluid that will be used should also be considered as it can affect the compatibility of the pump and other components.
The size and mounting configuration of the pump must also be considered to ensure proper installation and integration into the system. The location of the pump in the system and the accessibility for maintenance and repair should also be taken into account.
Compatibility with Existing Hydraulic System Components
It is essential to ensure that the pressure compensated variable displacement pump is compatible with the other components of the hydraulic system. This includes the hydraulic fluid, hoses, valves, and cylinders. Compatibility issues can cause system malfunctions or component failures, leading to increased maintenance and repair costs.
Maintenance and Repair Considerations
The maintenance requirements of the pump should be considered before installation. The maintenance schedule should be established and adhered to for the pump to function correctly and have a longer lifespan. Proper maintenance can also help prevent system failures and reduce repair costs.
When repairs are needed, it is important to have the proper knowledge and tools to perform them correctly. It may be necessary to contact a professional service provider to perform repairs or maintenance on the pump.
In summary, incorporating a pressure compensated variable displacement pump into a hydraulic system requires careful consideration of the intended application, compatibility with other system components, and maintenance requirements. By taking these factors into account, the pump can be integrated successfully, and the hydraulic system can operate efficiently and effectively.
Case Studies: Successful Implementation of Pressure Compensated Variable Displacement Pump
In this section, we will explore a few case studies that showcase the successful implementation of pressure compensated variable displacement pump in different hydraulic system applications. These case studies provide insights into the benefits of using this pump in hydraulic systems and how it has helped businesses achieve their goals.
Case Study 1: Construction Equipment
A construction equipment manufacturer wanted to improve the performance of its hydraulic excavator. The existing hydraulic system was not efficient enough, resulting in slower operation and increased fuel consumption. After evaluating different options, the manufacturer decided to incorporate a pressure compensated variable displacement pump in the hydraulic system.
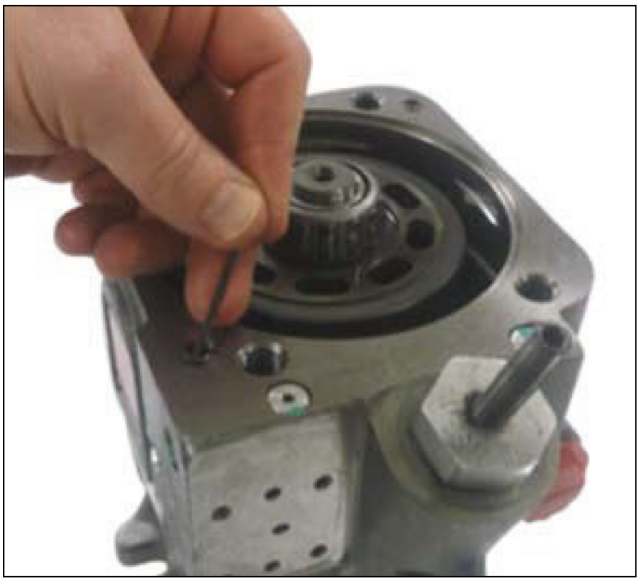
The pump provided the excavator with better control and improved responsiveness, resulting in faster operation and reduced fuel consumption. The variable displacement feature of the pump allowed the manufacturer to customize the hydraulic system according to the specific needs of the excavator. The manufacturer also reported lower maintenance costs and longer pump lifespan.
Case Study 2: Industrial Machinery
An industrial machinery manufacturer was facing issues with its hydraulic system, which was causing increased downtime and maintenance costs. The manufacturer was using a fixed displacement pump in the hydraulic system, which was not providing the required level of control and efficiency.
After considering different options, the manufacturer decided to incorporate a pressure compensated variable displacement pump in the hydraulic system. The pump allowed the manufacturer to customize the hydraulic system according to the specific requirements of the machinery. The pressure compensation feature of the pump ensured that the hydraulic system provided consistent performance, resulting in reduced downtime and maintenance costs. The manufacturer also reported improved energy efficiency and longer pump lifespan.
Case Study 3: Agricultural Machinery
An agricultural machinery manufacturer wanted to improve the performance of its hydraulic system used in a tractor. The existing hydraulic system was not efficient enough, resulting in slower operation and increased fuel consumption. After evaluating different options, the manufacturer decided to incorporate a pressure compensated variable displacement pump in the hydraulic system.
The pump provided the tractor with better control and improved responsiveness, resulting in faster operation and reduced fuel consumption. The variable displacement feature of the pump allowed the manufacturer to customize the hydraulic system according to the specific needs of the tractor. The manufacturer also reported lower maintenance costs and longer pump lifespan.
These case studies highlight the benefits of using pressure compensated variable displacement pump in different hydraulic system applications. The pump provides businesses with improved efficiency, better control, and flexibility in hydraulic system design, resulting in reduced downtime, lower maintenance costs, and longer lifespan. By customizing their hydraulic systems with the right pump, businesses can achieve their goals and improve their bottom line.
Conclusion
In conclusion, the incorporation of pressure compensated variable displacement pumps can greatly benefit hydraulic systems. With their ability to adjust to system pressure and flow demand, these pumps provide increased efficiency and flexibility in system design, resulting in lower operating and maintenance costs. However, careful consideration must be taken before incorporating these pumps into an existing hydraulic system, such as ensuring compatibility with other system components and proper maintenance and repair procedures.
Successful case studies have demonstrated the advantages of using pressure compensated variable displacement pumps in various hydraulic system applications, including in construction equipment and industrial machinery. These examples have shown how these pumps can improve system performance and reduce overall costs.
It is important for businesses to consider the benefits of customization when designing and maintaining their hydraulic systems. The use of pressure compensated variable displacement pumps can play a crucial role in achieving these goals.
In addition, it is important to compare pressure compensated variable displacement pumps with other types of hydraulic pumps and understand their pros and cons in order to determine which type is best suited for a specific hydraulic system.
Overall, the incorporation of pressure compensated variable displacement pumps is a smart investment for businesses looking to optimize the performance and efficiency of their hydraulic systems.
Comparison with Other Hydraulic Pumps
In the world of hydraulic systems, there are several types of pumps to choose from. While the pressure compensated variable displacement pump is a popular choice, it is important to consider other options before making a final decision. In this section, we will compare the pressure compensated variable displacement pump with other types of hydraulic pumps, weighing their pros and cons to help you decide which is best for your system.
Gear Pumps
Gear pumps are among the most common types of hydraulic pumps. They work by trapping fluid between the teeth of two meshing gears and forcing it through the pump, creating flow. Gear pumps are simple and cost-effective, making them a popular choice for low-pressure applications. However, they are not as efficient as other types of pumps and can be noisy due to their meshing gears.
Compared to gear pumps, pressure compensated variable displacement pumps have the advantage of being able to maintain a constant flow rate regardless of system pressure, resulting in improved efficiency. Additionally, variable displacement allows for greater flexibility in system design, making it easier to customize the system to specific requirements.
Vane Pumps
Vane pumps use a rotor with sliding vanes to create fluid flow. They are more efficient than gear pumps and can handle higher pressures, but they are more complex and expensive. Vane pumps also tend to be more sensitive to fluid contamination, which can impact their performance.
Compared to vane pumps, pressure compensated variable displacement pumps have the advantage of being able to maintain a constant flow rate regardless of system pressure. Additionally, variable displacement allows for greater flexibility in system design, making it easier to customize the system to specific requirements.
Piston Pumps
Piston pumps use reciprocating pistons to create fluid flow. They are the most efficient type of hydraulic pump and can handle high pressures, making them ideal for heavy-duty applications. However, they are also the most complex and expensive type of pump, making them a less popular choice for smaller applications.
Compared to piston pumps, pressure compensated variable displacement pumps have the advantage of being more cost-effective and easier to maintain. Additionally, variable displacement allows for greater flexibility in system design, making it easier to customize the system to specific requirements.
In conclusion, while each type of hydraulic pump has its own set of advantages and disadvantages, the pressure compensated variable displacement pump stands out for its ability to maintain a constant flow rate regardless of system pressure, resulting in improved efficiency. Additionally, variable displacement allows for greater flexibility in system design, making it easier to customize the system to specific requirements. When choosing a hydraulic pump for your system, consider the specific requirements of your application and weigh the pros and cons of each type before making a final decision.