Hydraulic systems are widely used in various industrial applications, from heavy equipment to manufacturing machinery. One of the key components of a hydraulic system is the hydraulic pump, which is responsible for converting mechanical power into hydraulic power by pressurizing hydraulic fluid. However, not all hydraulic systems require the same flow rate of hydraulic fluid at all times, which is where a variable flow hydraulic pump comes into play.Avariable flow hydraulic pumpis designed to adjust the flow rate of hydraulic fluid to meet the specific needs of a hydraulic system. This allows for improved energy efficiency, increased system performance, and greater flexibility in system design. In this article, we will provide an overview of variable flow hydraulic pump and its selection process, as well as its importance in industrial applications.
Understanding Variable Flow Hydraulic Pump
A variable flow hydraulic pump is a type of hydraulic pump that has the ability to vary its flow rate based on the hydraulic system’s demand. This is achieved by adjusting the pump’s displacement volume, which refers to the amount of fluid the pump can move per rotation. As the displacement volume changes, so does the pump’s flow rate.
Troubleshooting Kawasaki Hydraulic Pump Issues: Tips for Effective Adjustment
The components of a variable flow hydraulic pump typically include the pump housing, rotor, vanes or pistons, and control mechanisms such as a pressure compensator or a flow control valve. The pump housing contains the rotor, which rotates inside the housing to create the pumping action. The vanes or pistons, which are attached to the rotor, move back and forth within the pump housing to create a vacuum and draw in fluid, which is then forced out through the pump’s outlet.
The control mechanisms of a variable flow hydraulic pump are used to adjust the pump’s displacement volume and flow rate. A pressure compensator, for example, uses feedback from the hydraulic system’s pressure to adjust the pump’s displacement volume and maintain a constant pressure. A flow control valve, on the other hand, restricts the pump’s output flow to a certain rate, regardless of the hydraulic system’s demand.
Advantages of Variable Flow Hydraulic Pump
Variable flow hydraulic pumps have several advantages over traditional fixed flow pumps, including:
- Improved energy efficiency: One of the main advantages of variable flow hydraulic pumps is their ability to vary the flow rate of the hydraulic fluid to match the specific requirements of the system. This means that the pump only delivers the required amount of fluid, reducing energy waste and improving overall efficiency.
- Increased system performance: By delivering the precise amount of hydraulic fluid required, variable flow pumps can help to optimize the performance of the system. This can lead to faster cycle times, more accurate movements, and smoother operation.
- Flexibility in system design: The ability to vary the flow rate of the hydraulic fluid allows for greater flexibility in system design. With a variable flow pump, it is possible to adjust the flow rate to match the specific requirements of the system, making it easier to optimize the design for maximum performance and efficiency.
- Reduced heat generation: Traditional fixed flow pumps can generate a lot of heat, which can lead to increased wear and tear on the system components. By delivering only the required amount of fluid, variable flow pumps generate less heat, which can help to extend the life of the system.
- Lower noise levels: Variable flow pumps can also help to reduce the noise levels of hydraulic systems. By delivering only the required amount of fluid, they operate at a lower speed, which can lead to quieter operation.
Design and Analysis of Hydraulic Compensators for Improved Performance
Overall, the advantages of variable flow hydraulic pumps make them a popular choice for a wide range of industrial applications. They can help to improve energy efficiency, increase system performance, and provide greater flexibility in system design.
Factors to Consider When Selecting Variable Flow Hydraulic Pump
When selecting a variable flow hydraulic pump, several factors must be considered to ensure that the pump meets the specific application requirements. Some of the critical factors include:
Flow Rate Requirements
The flow rate requirement is a crucial factor to consider when selecting a variable flow hydraulic pump. The flow rate is the volume of hydraulic fluid that the pump can deliver per unit of time. It is essential to choose a pump that can provide the required flow rate for the specific application. The flow rate requirement depends on the system’s load characteristics, and it is critical to ensure that the pump’s maximum flow rate matches the system’s requirements.
Operating Pressure Range
The operating pressure range is another essential factor to consider when selecting a variable flow hydraulic pump. The pump must be capable of providing the required pressure range for the system. It is important to select a pump that can operate at the maximum system pressure without exceeding the pump’s maximum pressure rating.
Viscosity of Hydraulic Fluid
The viscosity of the hydraulic fluid is an important factor to consider when selecting a variable flow hydraulic pump. The pump’s performance is affected by the viscosity of the hydraulic fluid, and it is essential to choose a pump that can handle the specific viscosity range of the fluid used in the system.
System Load Characteristics
The system load characteristics are also crucial when selecting a variable flow hydraulic pump. The load characteristics include the system’s resistance to flow, which is affected by factors such as the load type, load size, and system layout. The pump must be capable of providing sufficient flow rate and pressure to overcome the system’s resistance to flow.
By considering these factors, the appropriate variable flow hydraulic pump can be selected for a specific application, ensuring optimal performance and efficiency.
Types of Variable Flow Hydraulic Pump
Variable Displacement Piston Pump Variable Displacement Vane Pump Variable Displacement Gear Pump
Overview of different types of variable flow hydraulic pump Advantages and disadvantages of each type Which type is best suited for a specific application
Variable flow hydraulic pumps are essential components of hydraulic systems, as they provide the necessary force to power different hydraulic actuators. There are different types of variable flow hydraulic pumps, each with its unique advantages and disadvantages. In this section, we will provide an overview of the three main types of variable flow hydraulic pumps and discuss their advantages and disadvantages.
Variable Displacement Piston Pump
Variable displacement piston pumps are one of the most common types of variable flow hydraulic pumps. They consist of a piston that moves back and forth inside a cylinder, which creates a vacuum that draws hydraulic fluid into the cylinder. As the piston moves back and forth, it creates pressure that forces the hydraulic fluid out of the cylinder and into the hydraulic system.
One advantage of variable displacement piston pumps is that they are highly efficient. They are capable of producing high pressures, which makes them suitable for applications that require high force output. They also have a wide range of displacement capabilities, which makes them flexible for use in different types of hydraulic systems.
However, variable displacement piston pumps can be expensive to manufacture and maintain. They require a high level of precision in their manufacturing, and they can be sensitive to contaminants in the hydraulic fluid. As a result, they may require more frequent maintenance than other types of hydraulic pumps.
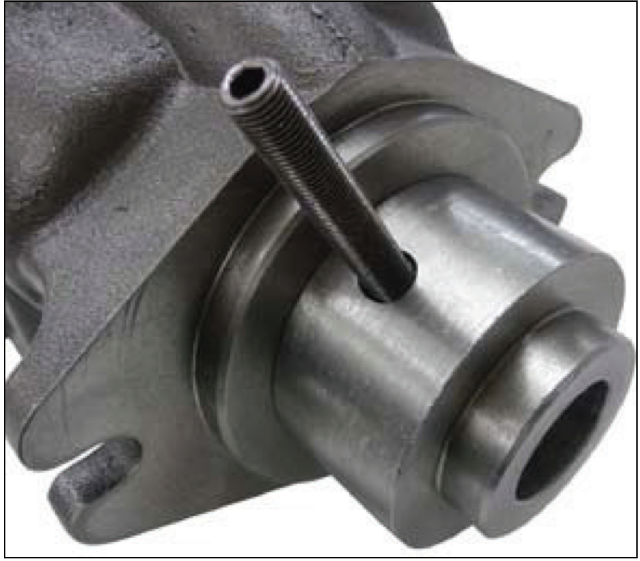
Variable Displacement Vane Pump
Variable displacement vane pumps are another type of variable flow hydraulic pump. They consist of a rotor that is mounted on a shaft and has slots that hold vanes. As the rotor spins, the vanes move in and out of the rotor, creating a vacuum that draws hydraulic fluid into the pump. The hydraulic fluid is then forced out of the pump by the pressure created by the vanes.
One advantage of variable displacement vane pumps is that they are relatively inexpensive to manufacture and maintain. They are also highly efficient, which makes them suitable for use in applications that require high force output. They have a wide range of displacement capabilities, which makes them flexible for use in different types of hydraulic systems.
However, variable displacement vane pumps can be sensitive to contaminants in the hydraulic fluid, which can cause damage to the vanes and decrease the pump’s efficiency. They also have a limited range of pressure capabilities, which makes them less suitable for applications that require high-pressure output.
Variable Displacement Gear Pump
Variable displacement gear pumps are a third type of variable flow hydraulic pump. They consist of two gears that mesh together and create a vacuum that draws hydraulic fluid into the pump. As the gears rotate, they force the hydraulic fluid out of the pump by creating pressure.
One advantage of variable displacement gear pumps is that they are relatively inexpensive to manufacture and maintain. They are also highly efficient, which makes them suitable for use in applications that require high force output. They have a wide range of displacement capabilities, which makes them flexible for use in different types of hydraulic systems.
However, variable displacement gear pumps can be sensitive to contaminants in the hydraulic fluid, which can cause damage to the gears and decrease the pump’s efficiency. They also have a limited range of pressure capabilities, which makes them less suitable for applications that require high-pressure output.
In summary, there are three main types of variable flow hydraulic pumps: variable displacement piston pumps, variable displacement vane pumps, and variable displacement gear pumps. Each type has its unique advantages and disadvantages, and the choice of which type to use in a specific application will depend on factors such
Pre-installation Considerations
Before installing a variable flow hydraulic pump, it is important to consider a few key factors. These considerations can help ensure that the pump is compatible with the existing hydraulic system and that it will perform as expected.
Site Preparation
The first consideration when installing a variable flow hydraulic pump is site preparation. This includes ensuring that there is adequate space for the pump and that the environment is suitable. The site should be clean, dry, and free from any debris or obstacles that may interfere with the installation process.
Selection of Variable Flow Hydraulic Pump
The selection of a variable flow hydraulic pump is critical to ensuring that the pump is compatible with the hydraulic system. When selecting a pump, it is important to consider the flow rate requirements, operating pressure range, and viscosity of the hydraulic fluid. Additionally, the system load characteristics should be taken into account.
Compatibility with Existing Hydraulic System Components
The variable flow hydraulic pump must be compatible with the existing hydraulic system components. This includes the hydraulic lines, valves, and other hydraulic components. Before installation, it is important to check the compatibility of the pump with the existing system and make any necessary adjustments.
By considering these factors, the installation of a variable flow hydraulic pump can be successful and provide numerous benefits to the hydraulic system.
Installation Procedures for Variable Flow Hydraulic Pump
Installing a variable flow hydraulic pump requires careful consideration of many factors to ensure that the system operates at peak efficiency. Here are the step-by-step procedures for the installation of a variable flow hydraulic pump:
- Identify the mounting location: The pump must be mounted securely to a solid foundation. Ensure that the mounting location is clear of debris and has enough space to access the pump and its components.
- Install the pump: The pump must be installed in a location where it can be easily accessed for maintenance and repair. It must also be installed so that the drive shaft is properly aligned with the motor coupling.
- Install the hydraulic fluid reservoir: The hydraulic fluid reservoir must be installed at the same height as the pump or above it. It should also be large enough to accommodate the volume of fluid required by the system.
- Install the control valve: The control valve must be installed between the pump and the actuator. It must also be installed in a location where it can be easily accessed for maintenance and repair.
- Install the pressure relief valve: The pressure relief valve must be installed in the outlet line of the pump to prevent damage to the system in case of pressure surges.
- Install the hydraulic hoses: The hydraulic hoses must be installed between the pump and the control valve, and between the control valve and the actuator. Ensure that the hoses are properly secured and do not have any leaks.
- Connect the pump to the power source: The pump must be connected to a power source that can provide the correct voltage and frequency. Follow the manufacturer’s instructions for proper electrical connection.
- Fill the hydraulic fluid reservoir: Fill the hydraulic fluid reservoir with the correct type and volume of hydraulic fluid specified by the manufacturer.
- Test the system: After installation, test the system for leaks, proper operation, and performance. Adjust the control valve and pressure relief valve as needed to ensure that the system is operating at peak efficiency.
By following these installation procedures, you can ensure that your variable flow hydraulic pump is installed properly and will provide reliable and efficient operation.
Proper maintenance and repair of a variable flow hydraulic pump is essential to ensure its efficient operation and long lifespan. Here are some recommended maintenance procedures, common issues, and their troubleshooting, as well as repair procedures for a variable flow hydraulic pump.
Recommended Maintenance Procedures
- Regularly check and replace the hydraulic fluid according to the manufacturer’s recommendations. Old or contaminated hydraulic fluid can cause damage to the pump and other hydraulic components.
- Check the filters regularly and replace them when necessary. Clogged filters can lead to a drop in system pressure, reducing the pump’s efficiency and potentially causing damage to other components.
- Keep the pump and its components clean to prevent dirt and debris from entering the hydraulic system.
- Check for leaks and repair them immediately to prevent damage to the pump and other hydraulic components.
Common Issues and Their Troubleshooting
- Low Flow Rate: A decrease in the pump’s flow rate can be caused by a clogged filter, a worn pump or motor, or low system pressure. Troubleshooting involves checking the filters and cleaning or replacing them if necessary, checking for worn components and replacing them if necessary, and checking the system pressure and adjusting it if needed.
- High Noise Level: An increase in the pump’s noise level can be caused by cavitation, aeration, or a worn pump or motor. Troubleshooting involves checking the hydraulic fluid level, checking for leaks, replacing worn components, and adjusting the system pressure.
- Overheating: Overheating can be caused by a clogged filter, low fluid level, or high system pressure. Troubleshooting involves checking the filters and cleaning or replacing them if necessary, checking the fluid level and refilling it if necessary, and adjusting the system pressure.
Repair Procedures
In some cases, it may be necessary to repair or replace components of a variable flow hydraulic pump. Here are some common repair procedures:
- Pump or Motor Replacement: If the pump or motor is worn or damaged beyond repair, it may need to be replaced. This involves removing the old component and installing a new one.
- Seal Replacement: Leaking seals can be replaced by removing the old seal and installing a new one.
- Piston Replacement: Worn or damaged pistons can be replaced by removing the old piston and installing a new one.
It is recommended to have a professional technician perform any necessary repairs on a variable flow hydraulic pump to ensure that it is done properly and safely.
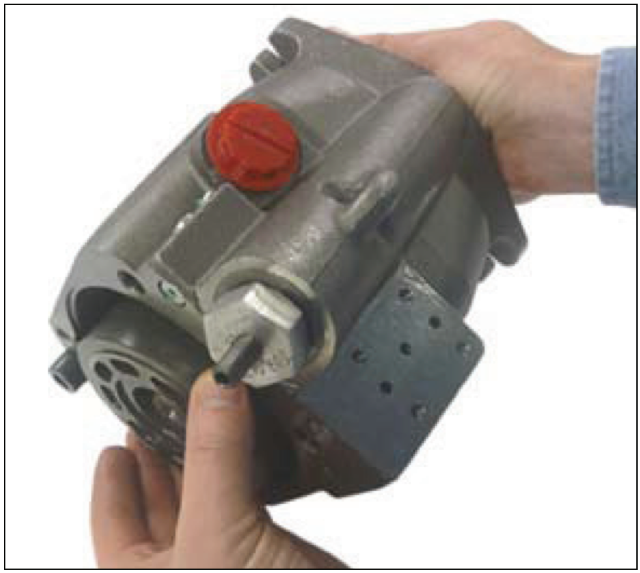
Proper selection, installation, and maintenance of a variable flow hydraulic pump are crucial for achieving optimal system performance and efficiency. By understanding the benefits of variable flow hydraulic pumps, considering the factors to consider when selecting one, and following the recommended procedures for maintenance and repair, businesses can ensure that their hydraulic systems operate smoothly and effectively.
Conclusion
In conclusion, the importance of selecting the right variable flow hydraulic pump for a specific application cannot be overstated. Variable flow hydraulic pumps offer numerous advantages such as improved energy efficiency, increased system performance, and flexibility in system design. However, selecting the wrong pump for an application can lead to inefficiencies, increased maintenance costs, and decreased system performance.
When selecting a variable flow hydraulic pump, it is important to consider factors such as flow rate requirements, operating pressure range, viscosity of hydraulic fluid, and system load characteristics. There are different types of variable flow hydraulic pumps available, each with its own advantages and disadvantages. Choosing the right type of pump for a specific application is crucial for optimal system performance.
Proper installation and maintenance of the variable flow hydraulic pump is also important. Pre-installation considerations such as site preparation and compatibility with existing hydraulic system components should be taken into account. Step-by-step installation procedures should be followed, and testing and validation of the installation should be done to ensure proper operation. Regular maintenance procedures should be carried out, and any issues should be promptly addressed to prevent system downtime.
In conclusion, businesses should consider the importance of proper selection, installation, and maintenance of variable flow hydraulic pumps for their hydraulic systems. By doing so, they can optimize system performance, reduce operating costs, and increase the lifespan of their hydraulic system.