Hydraulic pumps are an essential part of any business, and as such, they can often be damaged or destroyed in accidents. In this article, we’ll look at the options available for repairing hydraulic pumps, and how to choose the correct one for your needs.
If the pump is only partially damaged, it may be possible to repair it using parts from other pumps that are still operational. However, if the pump has been completely destroyed, it will likely need to be replaced.
When choosing a replacement pump, it is important to consider the characteristics of the pump that you need. For example, if you need a small pump for a specific application, then a smaller pump may be more appropriate than a larger one.
Additionally, it is important to choose a pump that is compatible with your equipment and setup. For example, some pumps require direct connection to water sources while others can operate off of an electric supply.
What is a hydraulic pump?
A hydraulic pump is a machine that uses the power of hydraulics to move fluid. They are used in a variety of applications, from powering tools and machines to moving water through irrigation systems. In many cases, they can be repaired or rebuilt using parts from other hydraulic pumps.
Hydraulic pumps are powered by a hydraulically-driven piston or rotor. The power is generated by a fluid flow through the pump, which turns the rotor. This motion creates a force that can be used to move objects or fluids.
How do hydraulic pumps work?
Hydraulic pumps are used to move fluids, such as water or oil, through pipelines, systems, or devices. They use the power of pressurized fluid to move objects. The most common type of hydraulic pump is a rotary vane pump. These pumps have a series of disks that rotate around a central shaft. The disks create a flow of fluid through the pump by moving the fluid against the pressure of the pressurized fluid. Hydraulic pumps can be rebuilt using parts or components from other types of pumps. For example, an electric motor can be used to power a rotary vane pump.
How do hydraulic pumps work in a car?
Hydraulic fluid is used to power the car’s engine. The engine uses the hydraulic fluid to turn the car’s wheels. The hydraulic fluid is also used to move other parts of the car, such as the suspension and the brakes.
Is a hydraulic pump rebuildable?
If your hydraulic pump is not under warranty or you are looking to save money, it may be worth trying to rebuild it yourself. A hydraulic pump is a relatively simple machine that can be easily repaired or rebuilt using commonly available parts and tools. Before beginning the repair or rebuild, however, it is important to understand the basics of how a hydraulic pump works and how it can be damaged.
A hydraulic pump is made up of several moving parts that work together to generate pressure and move fluid. The most common type of hydraulic pump is the vane pump, which uses a series of blades to turn a shaft. When the blades contact the fluid they create pressure, which forces the fluid through the pump chamber. Vane pumps are often used in applications where high volumes of fluid are required, such as water pumps and air conditioning units.
When a vane pump is damaged, it can fail to generate enough pressure to move the fluid through the pump chamber. This can cause various problems, including loss of power, failure of valves and seals, and even complete failure of the pump. In some cases, it may be possible to fix a vane pump using replacement parts; however, this is not always feasible or
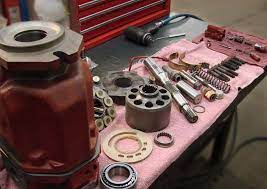
How long does it take to rebuild a hydraulic pump?
Depending on the condition of the pump and its parts, it can take anywhere from a few hours to a few days. However, the most difficult part of the process is often determining which part needs to be replaced.
Most hydraulic pumps are made up of several different parts, and it can be difficult to determine which one is malfunctioning. In some cases, a pump may start to leak or produce low pressure even if only one part is damaged. In order to fix the pump, it is often necessary to replace all of the parts.
Why should you be careful when rebuilding a hydraulic pump?
When it comes to repairing or rebuilding hydraulic pumps, there are a few things to keep in mind. First and foremost is the importance of safety. It’s essential that you take all the necessary precautions to ensure that you don’t end up injuring yourself or damaging the equipment. Second is proper maintenance. Without regular upkeep, your pumps can quickly become unreliable and prone to breakdowns. Finally, make sure you have the correct tools and parts on hand before beginning work. Otherwise, you may find yourself spending more time troubleshooting than fixing!
If you’re ever in doubt about whether or not it’s safe to tackle a hydraulic pump rebuild, always err on the side of caution. Contact a qualified technician for help before starting any work. And if you happen to run into any issues while rebuilding, don’t hesitate to call us for support. We’d be happy to help get your machine back up and running quickly and safely!
Tools needed to rebuild a pump
-Hammer
-Chisel
-Pry bar
-File
-Ruler
-Circular saw
-Jigsaw
-Drill bits: 8, 10, 12 and 14 mm
When your hydraulic pump needs to be rebuilt, it’s important to have the right tools on hand. Here’s a list of what you’ll need: a hammer, a chisel, a pry bar, a file, a ruler, a circular saw, a jigsaw, and drill bits 8, 10, 12 and 14 mm.
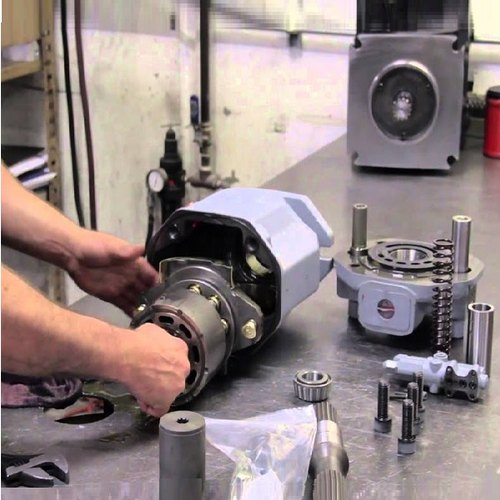
How much will it cost to rebuild my pump?
There is no one answer to this question as pump cost will vary depending on the make and model of your pump, the type of repair required, and the accessibility of the parts. However, many hydraulic experts believe that a typical pump rebuild will cost anywhere from $100 to $1,000.
Be sure to consult with a hydraulic specialist to get an accurate estimate of the cost of your specific pump rebuild.
Conclusion
Yes, hydraulic pumps can be rebuilt. In fact, it is a common and necessary task for many businesses. If your pump does not have warranty coverage or you need to replace the entire pump, rebuilding it is the best option. Rebuilds typically require less downtime than replacing a pump and often result in improved performance and longevity. Contact us today if you want to learn more about our rebuild services or if you need assistance determining whether or not your pump can be rebuilt.
Can hydraulic pumps be rebuilt,please click topkitparts see more