Hydraulic motors are used in a variety of applications, from industrial machinery to cars. They work by using hydraulic pressure to spin a shaft. In this article, we’ll learn about the different types of hydraulic motors and how they work. We’ll also look at some common applications for them and see how fast they can spin.
There are two main types of hydraulic motors:
1. Direct-drive hydraulic motors
2. Gear-driven hydraulic motors
Direct-drive hydraulic motors use a single shaft to spin the rotor. Gear-driven hydraulic motors use multiple gears to spin the rotor. Gear-driven motors are generally faster because they can spin faster than direct-drive motors. However, direct-drive motors are more efficient because they use less energy to spin the rotor.
The speed of a hydraulic motor can vary depending on the type of motor, the application, and the size and design of the rotor. However, in general, gear-driven hydraulic motors can spin between 1000 and 3000 rpm while direct-drive hydraulic motors can spin between 2000 and 6000 rpm.
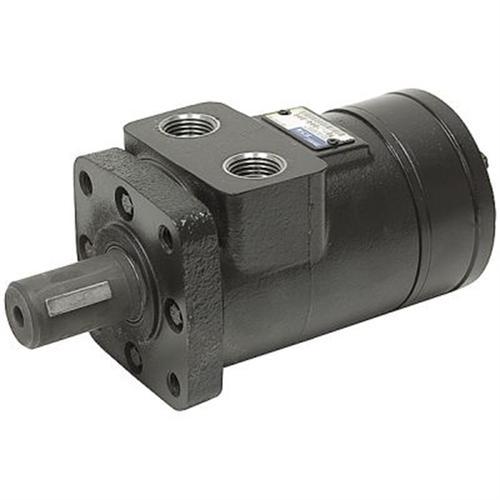
What is a hydraulic motor?
A hydraulic motor is a type of electric motor that uses hydraulic pressure to turn a shaft. This makes the motor very efficient because you don’t need to use a lot of energy to move the shaft. The downside is that you need a source of hydraulic pressure in order to operate the motor.
Hydraulic motors are often used in machines that need to be fast, like drills or saws. They’re also used in machinery that needs to be constantly moving, like printing presses or conveyors. Because they’re so efficient, hydraulic motors are also used in some applications where electric motors wouldn’t be as effective, like in aircraft or water pumps.
How hydraulic motors work
Hydraulic motors are a type of rotary engine that use hydraulic fluid to spin a rotor. The speed of the rotor can be controlled by changing the amount of hydraulic fluid flowing through the motor.
Hydraulic motors are often used in applications where high speed and torque are required, such as forestry machinery and construction equipment. Because they use less fuel than traditional engines, they are also very efficient.
Hydraulic motors are also used in submarines and space ships to generate power.
How does a hydraulic motor work?
There are numerous types of hydraulic motors, but all work on the same basic principle. A hydraulic motor is made up of a piston and cylinder. The piston is connected to a reservoir of pressurized fluid, and the cylinder is used to control the flow of fluid. When the piston is pushed down, it causes the fluid to flow into the cylinder. This pressure causes the cylinder to spin quickly around its axis.
There are a few factors that affect how fast a hydraulic motor can spin. One major factor is the size and shape of the piston and cylinder. The larger and more complex the piston and cylinder, the slower they will spin. Another factor that affects how fast a hydraulic motor can spin is the pressure inside the reservoir. If the pressure is too high, it will cause damage to the motor; if it’s too low, then the motor won’t be able to spin as fast.
How many rotations can a hydraulic motor make in one second?
A hydraulic motor can make up to 1,500 rotations per second.
How to test the speed of a hydraulic motor Conclusion
The speed of a hydraulic motor can be tested by using a gear indicator or an electric motor speedometer. When operating the motor at full power, the gear indicator should rotate quickly. If the electric motor speedometer reads less than full power, then the motor is running too slow.
When testing the speed of a hydraulic motor, be sure to use a gear indicator or electric motor speedometer that is accurate and reliable.
How fast can a hydraulic motor spin at different speeds?
Different speeds can produce different results with regards to the spin speed of a hydraulic motor. A slower speed will create a slower spin and vice versa. Keep in mind that this is just one small factor that can affect the performance of your machine. There are many other factors that need to be taken into account when designing and building a hydraulic machine.
Generally speaking, a hydraulic motor can spin between 1000 and 6000 rpm.
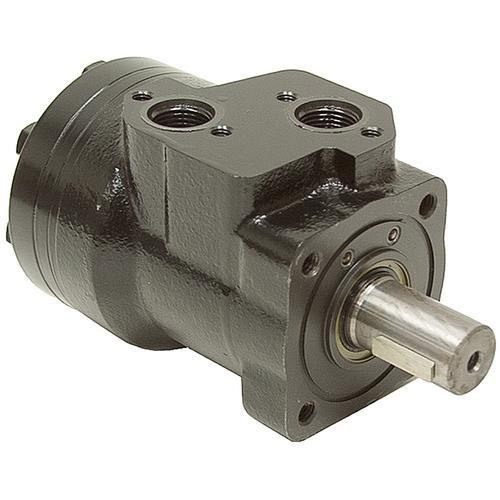
Practical Applications of Hydraulic Motors
The practical applications of hydraulic motors are vast and varied. From large industrial machines to tiny medical devices, hydraulic motors have revolutionized many industries. In this article, we will focus on the speed of a hydraulic motor.
A hydraulic motor’s speed is determined by the number of revolutions per minute (RPM) it can make. For example, a motors with 3000 RPM can move objects three times as fast as one with 1000 RPM. This is why it’s important to choose the right motor for the task at hand.
When choosing a motor, it’s important to consider the load it will be carrying and the distance it needs to travel. For example, a small hydraulic motor might be ideal for moving an object close to where it’s located, while a larger motor would be better for moving an object further away. Additionally, the type of fluid used in the motor affects its speed. A hydrostatic (water) motor operates at a slower speed than an electromagnetic (electric) motor because water has less kinetic energy.
What are the advantages of using a hydraulic motor over other motors?
Hydraulic motors are unique in that they can spin very quickly. This is an advantage because it allows them to move large objects quickly and efficiently. Additionally, they are generally more reliable than other types of motors.
Hydraulic motors are also typically quieter than other types of motors. This is an advantage because it can allow them to be used in areas where noise is a concern, such as factories and construction sites.
Conclusion
In this article, we will be discussing how fast a hydraulic motor can spin and some of the factors that affect the speed. We will also provide some examples to show you how spinning a hydraulic motor affects different types of applications. Finally, we will give you an overview of what to look for when choosing a hydraulic motor for your project.
How fast can a hydraulic motor spin,please click topkitparts see more