Two-stage hydraulic pumps are a type of two stage hydraulic pump adjustment commonly used in various hydraulic systems. They are designed to deliver high pressure and flow rates to the system while minimizing energy consumption. The main purpose of two-stage hydraulic pumps is to increase the efficiency and performance of hydraulic systems, resulting in lower operating costs and increased productivity.
There are two main types of two-stage hydraulic pumps: gear pumps and vane pumps. Gear pumps are generally used for higher pressure and lower flow rate applications, while vane pumps are used for lower pressure and higher flow rate applications. Both types of pumps have their unique features and advantages, making them suitable for different hydraulic system applications.
Two-stage hydraulic pumps can be used in a wide range of hydraulic systems, including industrial machinery, mobile equipment, and agricultural machinery. They are commonly used in applications such as construction equipment, material handling, and power generation.
In the next section, we will discuss the importance of proper adjustment of two-stage hydraulic pumps for optimal system efficiency and performance.

Importance of Proper Adjustment
Proper adjustment of two-stage hydraulic pumps is critical for achieving optimal system efficiency and performance. If a two stage hydraulic pump adjustment is not properly adjusted, it can result in inefficient operation and reduced performance, leading to increased operating costs and decreased productivity. Improper adjustment can also result in damage to system components and potential safety hazards.
One of the most important factors to consider when adjusting a two-stage two stage hydraulic pump adjustment is the pressure setting. The pressure setting determines the maximum pressure that the pump can deliver to the system. If the pressure setting is too low, the system may not be able to perform at its optimal level, while a pressure setting that is too high can cause damage to system components.
Another important factor to consider is the flow rate. The flow rate determines the amount of fluid that the pump can deliver to the system. If the flow rate is too low, the system may not be able to perform its required functions, while a flow rate that is too high can cause excessive wear and tear on system components.
Proper adjustment of a two stage hydraulic pump adjustment also involves ensuring that the pump is operating at its optimal efficiency. This involves adjusting the pump’s displacement, which determines the volume of fluid that the pump can deliver per revolution. If the pump’s displacement is not properly adjusted, it can result in inefficient operation and reduced performance.
In addition to ensuring optimal pressure, flow rate, and efficiency, proper adjustment of two-stage hydraulic pumps also involves considering other factors, such as the viscosity of the fluid being pumped, the size of the hydraulic system, and the type of load being applied to the system.
Overall, proper adjustment of two-stage hydraulic pumps is critical for achieving optimal system efficiency and performance. In the next section, we will discuss the process for adjusting two-stage hydraulic pumps in more detail.
Understanding Two-Stage Pump Adjustment
Two-stage hydraulic pumps are designed to operate at different pressure levels depending on the hydraulic system’s needs. To achieve optimal performance and efficiency, it is crucial to adjust the pump’s pressure settings and flow rate to match the system’s requirements.
The adjustment process for two-stage hydraulic pumps typically involves two main steps: setting the low-pressure relief valve and setting the high-pressure relief valve. The low-pressure relief valve controls the pump’s output pressure during the first stage, while the high-pressure relief valve controls the output pressure during the second stage.
The first step in adjusting a two-stage hydraulic pump is to set the low-pressure relief valve. This valve determines the maximum pressure that the pump can output during the first stage. The pressure setting should be based on the system’s minimum pressure requirements, taking into account factors such as the load and the system’s overall efficiency.
Once the low-pressure relief valve is set, the next step is to adjust the high-pressure relief valve. This valve determines the maximum pressure that the pump can output during the second stage. The pressure setting should be based on the system’s maximum pressure requirements, taking into account factors such as the load and the system’s overall efficiency.
In addition to adjusting the pressure settings, it is also important to adjust the pump’s flow rate to match the system’s requirements. The flow rate can be adjusted by changing the pump’s displacement or by installing a flow control valve in the system.
Proper adjustment of a two stage hydraulic pump adjustment requires an understanding of the hydraulic system’s needs and the pump’s capabilities. It is important to consult the manufacturer’s specifications and recommendations when making adjustments to ensure that the system operates safely and efficiently.
Testing and Validation
Once a two stage hydraulic pump adjustment has been properly adjusted, it is important to test and validate its performance to ensure that it is operating optimally. Testing and validation procedures involve verifying that the pump is providing the required flow rate and pressure output under various load conditions. This can be accomplished using a flow meter and pressure gauge, which allow the hydraulic system to be monitored and the pump’s performance to be measured.
During testing, it is important to monitor the system closely to ensure that the pump is operating within the manufacturer’s recommended parameters. Any deviation from these parameters could indicate a problem with the pump or other components in the hydraulic system. If any issues are identified during testing, they should be addressed promptly to prevent damage to the pump or other components.
Validation procedures involve confirming that the pump is operating within the manufacturer’s specified range of flow rates and pressure outputs. This can be done by comparing the measured flow rate and pressure output to the manufacturer’s specifications for the pump. If the measured values are within the specified range, then the pump can be considered validated and ready for use.
Troubleshooting with Hydraulic Pump Schematics: A Step-by-Step Guide
It is important to note that testing and validation procedures should be performed regularly, not just during initial installation. Regular testing and validation can help identify any changes or issues that may have occurred over time, and can ensure that the pump continues to operate optimally throughout its lifespan. This can also help prevent system failure and reduce the risk of downtime or costly repairs.
Troubleshooting and Maintenance
Two-stage hydraulic pumps are complex systems that require regular maintenance to ensure optimal performance. Over time, wear and tear can cause problems with the pump’s components, such as the seals, valves, and pistons. To prevent these problems, it is important to perform regular maintenance on the pump.
One common problem with two-stage hydraulic pumps is leakage. Leaks can occur due to worn or damaged seals, loose fittings, or damaged components. If you notice any signs of leakage, such as fluid on the ground or low fluid levels in the reservoir, it is important to address the issue as soon as possible.
Another common problem with two-stage hydraulic pumps is overheating. Overheating can be caused by a number of factors, such as insufficient fluid levels, blocked or clogged filters, or a malfunctioning pressure relief valve. To prevent overheating, it is important to check fluid levels regularly, clean or replace filters as needed, and ensure that the pressure relief valve is functioning properly.
Proper maintenance procedures for two-stage hydraulic pumps include regular inspection, cleaning, and lubrication of components. It is important to follow the manufacturer’s recommended maintenance schedule and procedures to ensure optimal performance and prevent system failure.
The Importance of Proper Hydraulic Valve Adjustment in Industrial Systems
If you encounter any problems with your two-stage hydraulic pump, it is important to troubleshoot the issue as soon as possible. This may involve testing various components, such as the pressure relief valve, to identify the source of the problem. Once the problem has been identified, it can be addressed through repair or replacement of the affected component.
In addition to regular maintenance and troubleshooting, it is also important to properly store and transport two-stage hydraulic pumps. This involves draining the fluid, cleaning the components, and protecting them from damage during storage or transport.
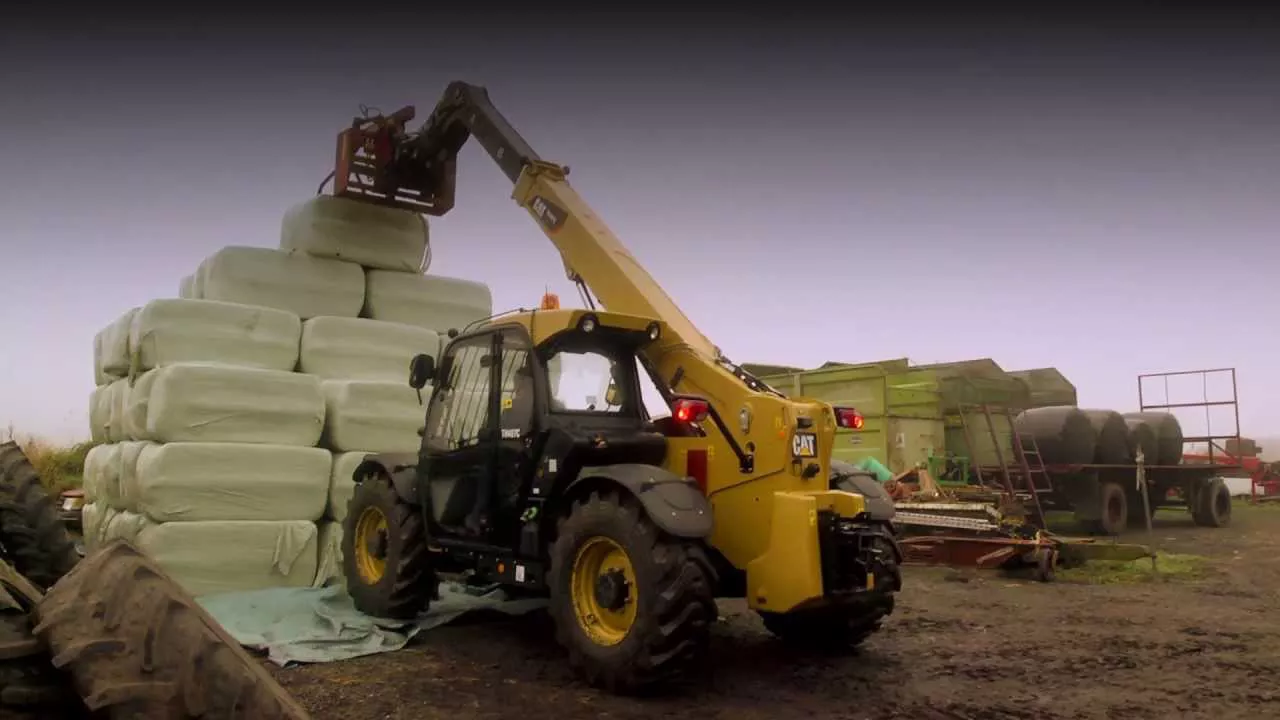
By following proper maintenance and troubleshooting procedures, two-stage hydraulic pumps can provide reliable and efficient performance for many years.
Industry Standards and Regulations
Proper adjustment of two-stage hydraulic pumps is not only important for optimal performance and efficiency, but also for compliance with industry standards and regulations. Hydraulic systems are subject to numerous regulations and standards that ensure safety, reliability, and environmental responsibility. It is important for operators to be aware of these regulations and ensure that their hydraulic systems meet the necessary requirements.
One of the most important regulations is the Occupational Safety and Health Administration (OSHA) regulations. OSHA requires employers to provide a safe and healthy workplace for their employees, which includes complying with regulations for hydraulic systems. OSHA regulations include requirements for proper system design, installation, maintenance, and operation.
In addition to OSHA regulations, hydraulic systems must comply with various industry standards. One of the most widely recognized industry standards for hydraulic systems is ISO 4413:2010 Hydraulic fluid power — General rules and safety requirements for systems and their components. This standard specifies the general rules and safety requirements for hydraulic systems and their components, including pumps, valves, and hoses. Compliance with ISO 4413 ensures that hydraulic systems are designed, installed, and maintained to the highest safety standards.
Other industry standards that may apply to hydraulic systems include the National Fire Protection Association (NFPA) standards, American Society of Mechanical Engineers (ASME) standards, and Society of Automotive Engineers (SAE) standards. These standards cover a wide range of topics, including system design, materials, installation, and maintenance.
Compliance with industry standards and regulations is critical for maintaining a safe and reliable hydraulic system. Operators should be familiar with the relevant standards and regulations and ensure that their hydraulic systems are designed, installed, and maintained in compliance with these requirements. Failure to comply with industry standards and regulations can result in serious safety hazards, system failure, and potential legal consequences.
Comparison with Other Hydraulic Pump Types
Two-stage hydraulic pumps are just one type of hydraulic pump available for use in various hydraulic system applications. Other types of hydraulic pumps include gear pumps, vane pumps, and piston pumps. In this section, we will compare two-stage hydraulic pumps with these other types of hydraulic pumps in terms of efficiency and performance.
Gear pumps are one of the most common types of hydraulic pumps. They work by using the rotation of gears to create a vacuum that draws fluid into the pump and then pressurizes it as the gears mesh together and force the fluid out of the pump. Gear pumps are known for their simplicity, low cost, and reliability. However, they are not very efficient at high pressures and can be quite noisy.
Vane pumps, on the other hand, use a rotating vane that slides in and out of a rotor to create a vacuum and pressure. They are more efficient than gear pumps at higher pressures, but are also more expensive and have a shorter lifespan.
Piston pumps use a reciprocating piston to draw in and pressurize fluid. They are the most efficient type of hydraulic pump, with the ability to operate at high pressures and with high flow rates. However, they are also the most expensive and complex type of hydraulic pump, requiring precise manufacturing and tolerances.
Compared to these other types of hydraulic pumps, two-stage hydraulic pumps offer a balance of efficiency, cost, and performance. They are more efficient than gear pumps at high pressures and have a longer lifespan than vane pumps. While they may not be as efficient as piston pumps, they are also less expensive and simpler to manufacture and maintain.
Ultimately, the choice of hydraulic pump type will depend on the specific needs and requirements of the hydraulic system. Two-stage hydraulic pumps are an excellent choice for many applications, but it is important to consider all options before making a final decision.
Conclusion
In summary, two-stage hydraulic pumps are an important component in many hydraulic systems, and proper adjustment is crucial to achieving optimal efficiency and performance. It is important to understand the purpose and function of two-stage pumps, as well as the different types and their applications in hydraulic systems.
Proper adjustment of two-stage pumps involves adjusting the pressure setting and flow rate, and it is important to ensure that the adjustment process is done correctly to prevent system failure and ensure safety. Testing and validation procedures should also be followed to confirm that the pump is properly adjusted.
Maintenance procedures should also be followed to prevent common problems with two-stage pumps, and troubleshooting procedures should be used to identify and resolve any issues that arise. It is important to comply with industry standards and regulations to ensure safety and reliability.
Comparisons with other types of hydraulic pumps have shown that two-stage pumps have certain advantages and disadvantages in terms of efficiency and performance, and these factors should be considered when selecting a pump for a specific hydraulic system application.
In conclusion, achieving optimal efficiency with two-stage hydraulic pumps requires proper adjustment, testing, and maintenance procedures, as well as compliance with industry standards and regulations. By following these guidelines, hydraulic systems can achieve higher efficiency and performance, resulting in improved productivity and reduced downtime.