Pompa hydraulic pumps are essential components of hydraulic systems used in various industrial applications. They are designed to convert mechanical energy into hydraulic energy, creating fluid flow and pressure that can be used to power machines and equipment. In this article, we will provide an introduction to pompa hydraulic pumps, discussing their definition, importance, and types.
Definition of Pompa Hydraulic Pumps
Pompa hydraulic pumps are mechanical devices that use pressure to create fluid flow, converting mechanical energy into hydraulic energy. They are commonly used in hydraulic systems to power machines and equipment, such as presses, lifts, and cranes. Pompa hydraulic pumps are designed to deliver a specific flow rate and pressure, which can be adjusted to meet the needs of the application.
Importance of Pompa Hydraulic Pumps in Industrial Applications
Pompa hydraulic pumps play a crucial role in various industrial applications, powering machines and equipment that perform critical tasks. They are commonly used in the manufacturing, construction, and transportation industries, among others. Pompa hydraulic pumps offer several advantages over other types of pumps, including higher efficiency, greater power density, and more precise control over fluid flow and pressure.
Types of Pompa Hydraulic Pumps
There are several types of pompa hydraulic pumps, each designed for specific applications. The most common types include:
- Gear Pumps Gear pumps are the most common type of pompa hydraulic pump, using two or more gears to create fluid flow and pressure. They are known for their simplicity and reliability and are commonly used in low to medium-pressure applications.
- Vane Pumps Vane pumps use a rotor with vanes to create fluid flow and pressure. They are known for their quiet operation and are commonly used in low to medium-pressure applications.
- Piston Pumps Piston pumps use one or more pistons to create fluid flow and pressure. They are known for their high efficiency and are commonly used in high-pressure applications.
In conclusion, pompa hydraulic pumps are essential components of hydraulic systems used in various industrial applications. They convert mechanical energy into hydraulic energy, creating fluid flow and pressure that can be used to power machines and equipment. Understanding the definition, importance, and types of pompa hydraulic pumps can help businesses select the right pump for their specific application, ensuring optimal performance and efficiency.
Understanding Hydraulic Systems
Hydraulic systems are used in various industrial applications, providing a reliable and efficient means of transmitting power. They use fluids, usually oil or water, to transmit force from one point to another. In this section, we will provide an overview of hydraulic systems, discussing their basics, importance in industrial applications, and components.
Basics of Hydraulic Systems
Hydraulic systems are based on Pascal’s law, which states that pressure applied to a fluid in a closed system is transmitted equally in all directions. Hydraulic systems consist of a pump, which creates fluid flow and pressure, a control valve, which regulates fluid flow and pressure, and an actuator, which converts fluid pressure into mechanical force. The system is usually closed, meaning that the fluid is contained within the system and circulated by the pump.
Importance of Hydraulic Systems in Industrial Applications
Hydraulic systems are essential components of various industrial applications, providing a reliable and efficient means of transmitting power. They are commonly used in manufacturing, construction, and transportation industries, among others. Hydraulic systems offer several advantages over other types of power transmission systems, including high power density, precise control, and low maintenance requirements.
Components of Hydraulic Systems
Hydraulic systems consist of several components, including:
- Pump The pump creates fluid flow and pressure, providing the power needed to operate the system. There are several types of pumps used in hydraulic systems, including gear pumps, vane pumps, and piston pumps.
- Control Valve The control valve regulates fluid flow and pressure, directing the fluid to the actuator as needed. There are several types of control valves used in hydraulic systems, including directional control valves, pressure control valves, and flow control valves.
- Actuator The actuator converts fluid pressure into mechanical force, allowing the system to perform work. There are several types of actuators used in hydraulic systems, including cylinders, motors, and hydraulic brakes.
- Reservoir The reservoir stores the fluid used in the system, providing a source of fluid for the pump to circulate. It also serves as a heat sink, dissipating the heat generated by the system.
- Filter The filter removes contaminants from the fluid, ensuring that the system operates smoothly and preventing damage to the components.
In conclusion, hydraulic systems are used in various industrial applications, providing a reliable and efficient means of transmitting power. They use fluids to transmit force from one point to another and consist of several components, including a pump, control valve, actuator, reservoir, and filter. Understanding the basics and components of hydraulic systems can help businesses select the right system for their specific application, ensuring optimal performance and efficiency.
How Pompa Hydraulic Pumps Work
Pompa hydraulic pumps are essential components of hydraulic systems, converting mechanical energy into hydraulic energy that can be used to power machines and equipment. In this section, we will provide an overview of how pompa hydraulic pumps work, discussing their working principle, components, and types of systems.
Working Principle of Pompa Hydraulic Pumps
Pompa hydraulic pumps work on the principle of displacement, using the movement of a piston, vane, or gear to create fluid flow and pressure. The pump is connected to the hydraulic system and circulates fluid through the system, creating pressure that can be used to power machines and equipment.
Components of Pompa Hydraulic Pumps
Pompa hydraulic pumps consist of several components, including:
- Inlet and Outlet Ports The inlet port is connected to the hydraulic system and allows fluid to enter the pump, while the outlet port is connected to the system and allows fluid to exit the pump.
- Pump Body The pump body contains the internal components of the pump and is designed to withstand the pressure created by the pump.
- Internal Components The internal components of the pump include a rotor, vanes, gears, or pistons, depending on the type of pump. These components work together to create fluid flow and pressure.
- Shaft and Bearings The shaft and bearings support the internal components of the pump and allow them to rotate.
Types of Pompa Hydraulic Pump Systems
There are several types of pompa hydraulic pump systems, each designed for specific applications. The most common types include:
- Fixed Displacement Pump Systems Fixed displacement pump systems are designed to deliver a fixed amount of fluid with each revolution of the pump. They are commonly used in applications where a constant flow rate is required, such as in hydraulic presses and lifts.
- Variable Displacement Pump Systems Variable displacement pump systems can adjust the amount of fluid delivered with each revolution of the pump, allowing for greater control over fluid flow and pressure. They are commonly used in applications where varying flow rates are required, such as in excavators and cranes.
- Radial Piston Pump Systems Radial piston pump systems use a set of radial pistons to create fluid flow and pressure. They are known for their high efficiency and are commonly used in high-pressure applications.
In conclusion, pompa hydraulic pumps are essential components of hydraulic systems, converting mechanical energy into hydraulic energy that can be used to power machines and equipment. They work on the principle of displacement, using the movement of a piston, vane, or gear to create fluid flow and pressure. Understanding the working principle, components, and types of pompa hydraulic pump systems can help businesses select the right pump for their specific application, ensuring optimal performance and efficiency.
Factors Affecting Pompa Hydraulic Pump Performance
Several factors can impact the performance of pompa hydraulic pumps, including the type of pump, fluid viscosity, temperature, and pressure. In this section, we will discuss the factors that affect pompa hydraulic pump performance, the importance of proper pump performance, and the effects of low or high pump performance.
Factors That Affect Pompa Hydraulic Pump Performance
- Type of Pump The type of pump used can affect pump performance. Different types of pumps have different efficiencies, flow rates, and pressure capabilities, which can impact pump performance in specific applications.
- Fluid Viscosity The viscosity of the fluid used in the hydraulic system can affect pump performance. Higher viscosity fluids require more energy to circulate through the system, which can result in lower pump performance.
- Temperature Temperature can affect pump performance, as high temperatures can cause the fluid to thin and reduce the efficiency of the pump. High temperatures can also cause damage to the internal components of the pump, reducing its lifespan.
- Pressure The pressure requirements of the application can affect pump performance. If the pump is not capable of delivering the required pressure, the system may not operate properly, resulting in reduced performance.
Importance of Proper Pump Performance
Proper pump performance is essential for the efficient and reliable operation of hydraulic systems. If a pompa hydraulic pump is not operating at peak performance, it can impact the performance of the entire system, resulting in decreased productivity, increased maintenance costs, and potential equipment damage.
Effects of Low or High Pump Performance
Low pump performance can result in reduced flow rates, decreased pressure, and increased energy consumption. It can also result in increased wear and tear on the pump and other system components, reducing the lifespan of the equipment.
High pump performance can result in increased pressure, which can cause damage to the system and equipment. It can also result in increased energy consumption and reduced pump lifespan.
In conclusion, several factors can impact the performance of pompa hydraulic pumps, including the type of pump, fluid viscosity, temperature, and pressure. Proper pump performance is essential for the efficient and reliable operation of hydraulic systems, and low or high pump performance can result in decreased productivity, increased maintenance costs, and potential equipment damage. Understanding the factors that affect pompa hydraulic pump performance can help businesses select the right pump for their specific application and ensure optimal performance and efficiency.
Selecting the Right Pompa Hydraulic Pump
Selecting the right pompa hydraulic pump for a specific application is essential for optimal performance and efficiency. In this section, we will discuss the factors to consider when selecting a pompa hydraulic pump, the types of pumps for different applications, and the importance of selecting the right pump.
Factors to Consider When Selecting a Pompa Hydraulic Pump
- Flow Rate The required flow rate is one of the most critical factors to consider when selecting a pompa hydraulic pump. The flow rate is the amount of fluid that the pump can deliver per unit of time and is measured in gallons per minute (GPM) or liters per minute (LPM).
- Pressure The required pressure is another critical factor to consider when selecting a pompa hydraulic pump. The pressure is the force per unit area and is measured in pounds per square inch (PSI) or bar.
- Fluid Viscosity The viscosity of the fluid used in the hydraulic system can affect pump performance, as higher viscosity fluids require more energy to circulate through the system.
- Temperature The temperature of the fluid and the environment in which the pump will operate can impact pump performance and lifespan.
- Type of Pump Different types of pompa hydraulic pumps have different efficiencies, flow rates, and pressure capabilities, which can impact pump performance in specific applications.
Types of Pompa Hydraulic Pumps for Different Applications
- Gear Pumps Gear pumps are the most common type of pompa hydraulic pump and are commonly used in low to medium-pressure applications. They are known for their simplicity and reliability and are suitable for a wide range of applications.
- Vane Pumps Vane pumps are commonly used in low to medium-pressure applications and are known for their quiet operation. They are suitable for applications where low noise levels are required.
- Piston Pumps Piston pumps are known for their high efficiency and are commonly used in high-pressure applications. They are suitable for applications where high pressure and high flow rates are required.
Importance of Selecting the Right Pompa Hydraulic Pump
Selecting the right pompa hydraulic pump is essential for optimal performance and efficiency. Using the wrong pump can result in decreased productivity, increased maintenance costs, and potential equipment damage. It is important to consider the factors outlined above when selecting a pompa hydraulic pump, ensuring that the pump is suitable for the specific application and capable of delivering the required flow rate and pressure.
In conclusion, selecting the right pompa hydraulic pump is essential for optimal performance and efficiency. The factors to consider when selecting a pompa hydraulic pump include flow rate, pressure, fluid viscosity, temperature, and type of pump. Different types of pompa hydraulic pumps are suitable for different applications, and selecting the right pump is critical for the efficient and reliable operation of hydraulic systems.
Installation and Maintenance of Pompa Hydraulic Pumps
Proper installation and maintenance of pompa hydraulic pumps are essential for optimal performance and longevity. In this section, we will discuss the importance of proper installation and maintenance of pompa hydraulic pumps, the steps for installing and maintaining pompa hydraulic pumps, and the tools required for installation and maintenance.
Importance of Proper Installation and Maintenance of Pompa Hydraulic Pumps
Proper installation and maintenance of pompa hydraulic pumps are critical for the efficient and reliable operation of hydraulic systems. Incorrect installation can result in decreased pump performance, increased wear and tear on system components, and potential equipment damage. Poor maintenance can also result in decreased pump performance, increased energy consumption, and reduced pump lifespan.
Steps for Installing and Maintaining Pompa Hydraulic Pumps
- Installation The following steps should be followed for the installation of pompa hydraulic pumps:
- Ensure that the pump is compatible with the hydraulic system and the application requirements.
- Install the pump in a clean, dry, and well-ventilated area, away from any heat sources.
- Ensure that the pump is properly aligned with the hydraulic system and is securely mounted.
- Connect the inlet and outlet ports of the pump to the hydraulic system, ensuring that the connections are tight and leak-free.
- Fill the hydraulic system with the appropriate fluid, ensuring that the fluid level is correct and that there are no air bubbles in the system.
- Start the hydraulic system and check for any leaks or abnormal noises.
- Maintenance The following steps should be followed for the maintenance of pompa hydraulic pumps:
- Regularly check the fluid level and condition, ensuring that the fluid is clean and free from contaminants.
- Regularly check the pressure and flow rate of the pump, ensuring that it is operating within the required specifications.
- Regularly check the condition of the pump and its components, looking for signs of wear, damage, or leaks.
- Replace any worn or damaged components as soon as possible.
- Clean the pump and its components regularly, ensuring that they are free from dirt and debris.
Tools Required for Installation and Maintenance of Pompa Hydraulic Pumps
The following tools are required for the installation and maintenance of pompa hydraulic pumps:
- Wrenches and sockets for tightening and loosening connections
- Hydraulic pressure gauge for checking pressure and flow rate
- Fluid level gauge for checking fluid level
- Cleaning supplies for cleaning the pump and its components
- Replacement components for replacing worn or damaged parts
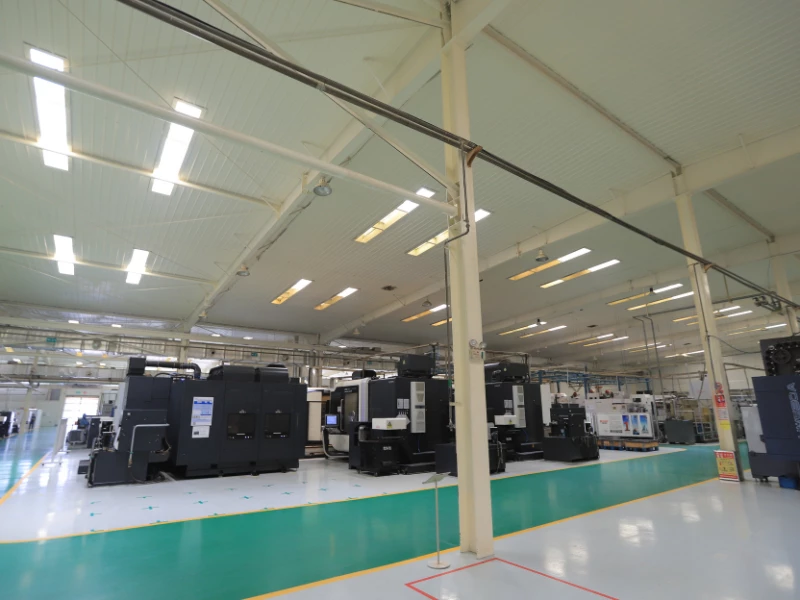
In conclusion, proper installation and maintenance of pompa hydraulic pumps are essential for optimal performance and longevity. The steps for installing and maintaining pompa hydraulic pumps should be followed carefully, ensuring that the pump is installed correctly and maintained regularly. The tools required for installation and maintenance should be on hand, ensuring that any issues can be addressed quickly and efficiently.
Common Problems with Pompa Hydraulic Pumps
Like any mechanical system, pompa hydraulic pumps can experience problems from time to time. In this section, we will discuss common problems with pompa hydraulic pumps, the symptoms of pompa hydraulic pump problems, and the solutions to these problems.
Common Problems with Pompa Hydraulic Pumps
- Overheating Overheating is a common problem with pompa hydraulic pumps and can be caused by several factors, including low fluid levels, excessive fluid viscosity, and high ambient temperatures. Overheating can cause damage to the internal components of the pump and reduce its lifespan.
- Leaks Leaks in the hydraulic system can cause a loss of pressure, reduced performance, and potential equipment damage. Common causes of leaks include damaged seals, cracked hoses, and loose connections.
- Cavitation Cavitation occurs when air bubbles form in the hydraulic system, resulting in a loss of pressure and reduced pump performance. Cavitation can be caused by low fluid levels, excessive fluid viscosity, or a clogged suction filter.
- Noisy Operation Noisy operation can be caused by several factors, including damaged bearings, loose components, or worn internal components.
Symptoms of Pompa Hydraulic Pump Problems
The following are some of the symptoms of pompa hydraulic pump problems:
- Reduced flow rate
- Reduced pressure
- Overheating
- Noisy operation
- Vibration
- Leaks
- Cavitation
Solutions to Common Pompa Hydraulic Pump Problems
The following are some of the solutions to common pompa hydraulic pump problems:
- Overheating To address overheating, ensure that the fluid level is correct, the fluid viscosity is appropriate for the application, and the ambient temperature is within the specified range. If the problem persists, consider installing a cooling system or upgrading to a pump with higher efficiency.
- Leaks To address leaks, identify and repair the damaged seals, hoses, or connections. Regularly inspect the hydraulic system for signs of leaks and address them as soon as possible.
- Cavitation To address cavitation, ensure that the fluid level is correct, the fluid viscosity is appropriate for the application, and the suction filter is clean and free from debris. If the problem persists, consider upgrading to a pump with higher flow rate and pressure capabilities.
- Noisy Operation To address noisy operation, identify and repair the damaged bearings, loose components, or worn internal components. Regularly inspect the pump and its components for signs of wear and damage.
In conclusion, pompa hydraulic pumps can experience problems from time to time, including overheating, leaks, cavitation, and noisy operation. Identifying the symptoms of these problems and addressing them as soon as possible can help prevent equipment damage and ensure optimal performance and efficiency. Regular maintenance, including inspections and repairs, can help prevent these problems from occurring in the first place.
Troubleshooting Pompa Hydraulic Pumps
Troubleshooting pompa hydraulic pumps is essential for identifying and addressing problems as soon as possible. In this section, we will discuss the importance of troubleshooting pompa hydraulic pumps, the steps to troubleshoot pompa hydraulic pumps, and the tools required for troubleshooting.
Importance of Troubleshooting Pompa Hydraulic Pumps
Troubleshooting pompa hydraulic pumps is critical for identifying and addressing problems as soon as possible. Prompt troubleshooting can prevent equipment damage, reduce downtime, and ensure optimal performance and efficiency. Regular troubleshooting and maintenance can also help identify potential problems before they occur.
Steps to Troubleshoot Pompa Hydraulic Pumps
The following steps should be followed when troubleshooting pompa hydraulic pumps:
- Identify the Problem The first step in troubleshooting pompa hydraulic pumps is to identify the problem. This can be done by observing the symptoms of the problem, such as reduced flow rate or noisy operation, and performing diagnostic tests, such as checking the fluid level and pressure.
- Gather Information Once the problem has been identified, gather information about the hydraulic system and the pump, including the specifications, operating conditions, and maintenance history. This information can help identify potential causes of the problem and guide the troubleshooting process.
- Perform Diagnostic Tests Perform diagnostic tests to further identify the cause of the problem, such as checking the fluid level and condition, checking the pressure and flow rate, and inspecting the pump and its components for signs of wear or damage.
- Identify Potential Causes Based on the information gathered and the diagnostic tests performed, identify potential causes of the problem. Common causes of pompa hydraulic pump problems include low fluid levels, damaged seals, clogged filters, and worn or damaged components.
- Address the Problem Once the cause of the problem has been identified, address the problem by repairing or replacing the damaged or worn components, cleaning the system, and ensuring that the pump is properly aligned and mounted.
- Test the Pump After addressing the problem, test the pump to ensure that it is operating correctly and within the specified parameters. Monitor the pump and the hydraulic system for any further problems.
Tools Required for Troubleshooting Pompa Hydraulic Pumps
The following tools are required for troubleshooting pompa hydraulic pumps:
- Wrenches and sockets for tightening and loosening connections
- Hydraulic pressure gauge for checking pressure and flow rate
- Fluid level gauge for checking fluid level
- Diagnostic tools for identifying potential problems, such as a stethoscope for identifying noisy components
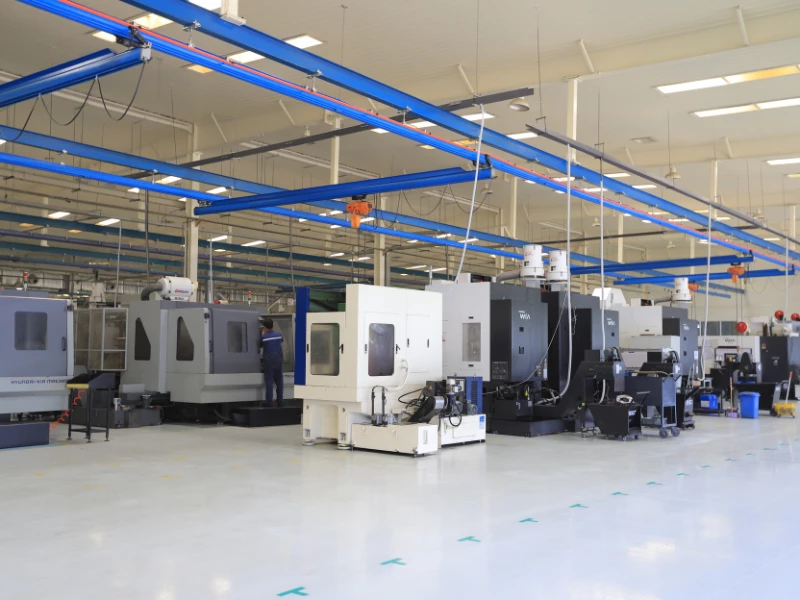
In conclusion, troubleshooting pompa hydraulic pumps is critical for identifying and addressing problems as soon as possible. The steps to troubleshoot pompa hydraulic pumps include identifying the problem, gathering information, performing diagnostic tests, identifying potential causes, addressing the problem, and testing the pump. The tools required for troubleshooting include wrenches, sockets, hydraulic pressure gauges, fluid level gauges, and diagnostic tools. Regular troubleshooting and maintenance can help prevent problems and ensure optimal performance and efficiency of pompa hydraulic pumps.