Cavitation is a phenomenon that can occur when the liquid or gas inside a hydraulic pump encounters a sudden increase in pressure. This increase in pressure can cause bubbles to form, which in turn can lead to the destruction of the pump’s components. Cavitation is a serious issue and one that needs to be avoided at all costs. If you’re ever faced with a pump that’s cavitating, don’t panic; there are steps you can take to prevent the damage from happening and restore your pump to working order.
What is hydraulic pump cavitation?
The hydraulic pump cavitation is caused by the air turbulence which is created in the liquid due to the sudden change in speed of the pump. This turbulence causes the liquid to vaporize, and this vaporization process leads to the formation of bubbles. The bubbles increase in size until they reach a certain size, at which point they burst and create cavitation.
How does hydraulic pump cavitation happen?
Cavitation is a phenomenon that can occur in hydraulic pumps, particularly when the pump is running at high speed. Cavitation occurs when the air inside the pump becomes so hot and pressurized that it starts to vaporize. This vaporized air creates a bubble of gas that can rapidly collapse, creating a powerful explosion. Cavitation can damage the pump and even cause it to fail.
What can be done to prevent or reduce hydraulic pump cavitation?
The main causes of hydraulic pump cavitation are incorrect lubrication, faulty design, and inadequate cooling. Correct lubrication can be ensured by using the correct grade of oil and by maintaining a proper oil level in the hydraulic system. Failing to design for cavitation can result in the pump being overworked and failing prematurely. Improving the overall cooling system of the hydraulic system can also help to reduce cavitation.
Cavitation can also be prevented by using proper maintenance procedures and by following manufacturers’ guidelines. Proper maintenance includes checking the oil level, performing regular inspections, and replacing parts as needed.
In some cases, damage caused by cavitation can be fixed without any permanent changes. This is done by using a shock absorber, which helps to reduce the frequency and severity of cavitation.
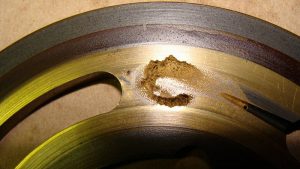
Cavitation is a bubble formation that can occur in many different liquids and gases
Cavitation is a problem with pumps because it creates bubbles in the fluid flow and these bubbles can cause great damage to the pump
One cause of cavitation is when the liquid or gas particles become too small to travel through the fluid without breaking apart. This can happen when the liquid or gas is heated up and starts to vaporize
Another common cause of cavitation is when a pump is operated at a high speed. This can cause tiny bubbles to form in the liquid or gas stream, which then collapse due to their own weight.
Ways to prevent cavitation
There are many ways to prevent cavitation in hydraulic pumps. Some of the most common methods include using high quality oil, using proper bypassing, and using a surge tank. Other measures that can be taken include using a lower speed pump, tensioners at the correct level, and an anti-cavitation device.
One of the most common ways to prevent cavitation in hydraulic pumps is to use high quality oil. This is because low quality oils will create a lot of foam, which can lead to cavitation. Another way to prevent cavitation is to use proper bypassing. Bypassing means that the hydraulic fluid is routed around the area that is prone to cavitation. This will help to prevent the formation of bubbles, which can lead to cavitation.
Another way to prevent cavitation in hydraulic pumps is to use a surge tank. A surge tank is a device that stores extra hydraulic fluid in case of an emergency. This will help to prevent pump damage due to cavitation. Other measures that can be taken include using a lower speed pump, tensioners at the correct level, and an anti-cavitation device.
Causes of hydraulic pump cavitation
Hydraulic pump cavitation can occur when the liquid being pumped is subjected to sudden fluctuations in pressure. These fluctuations can come from a number of sources, including changes in the speed or volume of the flowing fluid, and differences in temperature between the pump discharge and the surrounding environment.
The most common cause of hydraulic pump cavitation is a change in speed or volume of the fluid being pumped. When the flow rate suddenly increases, the pressure inside the pump cylinder drops below the vapor pressure of the liquid. Vaporization (turning into a gas)of some of the liquid leads to increased gas pressures inside and outside of the pump cylinder, which in turn causes further vaporization and so on. This vicious cycle quickly leads to Pump Cavitation!
Another common cause of cavitation is a difference in temperature between the pump discharge and the surrounding environment. When liquid is pumped from a colder to a warmer environment, it expands (goes from a liquid to a gas). This increase in pressure causes bubbles to form inside the liquid, which can then burst due to differential pressures (the higher pressure on top pushing down on the lower pressure underneath).
Pump Cavitation can present several problems for your machine. For
There are many causes of cavitation
– some are mechanical, while others are chemical.
– Mechanical causes of cavitation can include high speeds, sudden changes in pressure, and sharp edges on moving parts.
– Chemical causes of cavitation can include the presence of water vapor, air molecules, or organic molecules.
– Cavitation can occur in any hydraulic system, but is most likely to occur in systems with high speeds and low pressures.
– Cavitation can be a serious problem because it can lead to pump failure and damage to equipment.
Conclusion
One of the most common causes of hydraulic pump cavitation is air entrapment. In this situation, the air gets trapped in between the liquid and the pump impeller, causing excessive friction that can damage or even destroy the pump. If you notice increased noise levels, decreased efficiency, or other indications that your pump is experiencing cavitation, it’s important to take action and remove any excess air from the system as soon as possible.