Hydraulic pumps are essential pieces of machinery in many industrial and commercial settings, and their variety is staggering. In this article, we’ll take a look at the different types of hydraulic pumps, their uses, and what you need to know if you’re thinking of purchasing one.
Types of Hydraulic Pumps
There are a few different types of hydraulic pumps, each with its own specific characteristics and applications.
Vacuum Pump: A vacuum pump is used to create a negative pressure, or suction, in order to move or extract something else. They’re commonly used in industrial settings to move liquids or gas, and can be found in a variety of sizes and capacities.
A vacuum pump is used to create a negative pressure, or suction, in order to move or extract something else. They’re commonly used in industrial settings to move liquids or gas, and can be found in a variety of sizes and capacities. Piston Pump: A piston pump is similar to a vacuum pump, but uses pistons instead of tubes to create the negative pressure. They’re typically used for moving fluid substances that don’t require high pressures, such as water or milk.
A piston pump is similar to a vacuum pump, but uses pistons instead of tubes to create the negative pressure. They’re typically used for moving fluid substances that don’t require high pressures, such as water or milk. Rotary Pump: A rotary pump consists of a number of rotating disks that act as pistons,
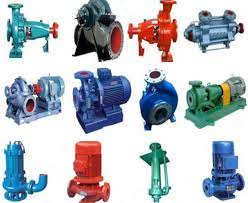
What is a hydraulic pump?
There are many different hydraulic pumps, but all of them work on the same principle. A fluid is pumped through a tube and into a piston, which causes a change in pressure. This can be used to push things forwards, or pull things backwards.
There are three main types of hydraulic pump: positive displacement, rotary and vane-type. Positive displacement pumps use a plunger to move the fluid, while rotary and vane-type pumps use blades or vanes to create movement.
Different types of Hydraulic Pumps and Their Uses
There are many different types of hydraulic pumps, each with its own unique purpose. Here are just a few examples:
– Piston pump: Used to move liquids or gas through a pipe or system
– diaphragm pump: Used to push or pull objects
– screw pump: Used in mining and oil production
– vane pump: Used to move liquid or gas through a porous medium
– electric motor pump: Used in water treatment and sewage plants
What do the different types of pumps do?
There are many different types of hydraulic pumps, each with its own unique purpose. Here is a quick overview of the most common types: oil-based pumps, water-based pumps, hybrid pumps, and air-cushion pumps.
Oil-based pumps are the most common type and are used to move liquids or gas. They work by using a piston to compress the fluid, which then moves the pump forward. Oil-based pumps are usually small and lightweight, making them easy to move around. They also have a short lifespan due to the oil they use being difficult to keep clean.
Water-based pumps work similar to oil-based pumps but use water instead of oil. They are often used to move water or other liquids, and they are larger and more powerful than oil-based pumps. Water-based pumps can be used in both indoor and outdoor settings, making them more versatile. However, they also have a longer lifespan due to their reliance on water.
Hybrid pumps combine features from both oil-based and water-based pumps. They are usually smaller than either type of pump, making them easier to move around. They also have a shorter lifespan than either
How do hydraulic pumps work?
There are many different types of hydraulic pumps, but all work in a similar way. A hydraulic pump uses the pressure of fluid to move objects or fluid from one place to another. Hydraulic pumps can be used for a variety of tasks, including moving things like water, oil, and gas.
When was the first hydraulic pump invented?
The first hydraulic pump was invented in 1678 by the Italian scientist and mathematician Evangelista Torricelli.
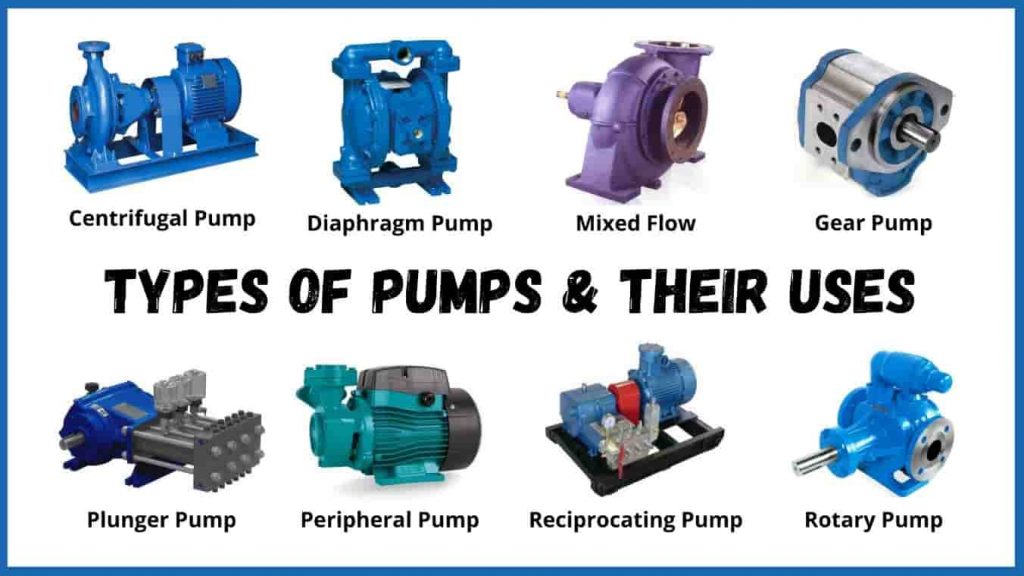
Why are these pumps so important in our everyday lives?
Hydraulic pumps are incredibly important in our everyday lives because they allow us to move things around fluidly. They are used in a variety of industries, such as construction, agriculture, and manufacturing. There are many different types of hydraulic pumps, but the most common are those that use pistons to move the fluid.
Different pumps that are used for different jobs or by different companies
There are a variety of hydraulic pumps on the market that can be used for a variety of purposes. Some pumps are designed for industrial use, while others are specific to the automotive industry. Here is a list of some of the most common types of hydraulic pumps:
-Rotary vane pump: This type of pump is often used in industrial settings because it is efficient and durable. It works by using a series of rotor blades to move the fluid.
-Piston pump: This pump is often used in automotive applications because it is compact and efficient. It uses pistons to move the fluid and is often more reliable than rotary vane pumps.
-Vane pump: This type of pump is often used in agricultural applications because it can move large volumes of fluid quickly and easily. It uses a series of vanes to spin and move the fluid.
Benefits of Using a Hydraulic Pump
There are many different types of hydraulic pumps, each with its own benefits. Here are a few of the most common:
-Rotary vane pumps: These are the most common type of pump and are used for a variety of applications, including irrigation, water harvesting, and oil and gas production. They have a low profile and can be easily moved around.
-Piston pumps: These pumps are used for high-volume applications, such as swimming pools and water treatment plants. They have a higher profile and require more power to operate.
-Vacuum pumps: These pumps are used in industries that require high vacuum levels, such as medical equipment and automotive parts. They have a higher price tag but also offer greater efficiency than other types of pumps.
Conclusion
There are a few different types of hydraulic pumps, but the most common type is the piston pump. This type of pump uses pistons to move the fluid, and it is used in many applications where high pressure is needed, including mining and oil drilling.
How many different hydraulic pumps are there,please click topkitparts see more