Hydraulic pumps are devices that use pressurized liquid to move objects. They come in two main types: 2 stage and 3 stage. A 2 stage pump is usually smaller and lighter than a 3 stage pump, but it can only move a limited amount of fluid at a time. A 3 stage pump, on the other hand, is larger and more powerful, but it can move more fluid at one time.
What is a 2-stage hydraulic pump?
A 2-stage hydraulic pump is a type of pump that consists of two separate chambers. The first chamber is used to move the fluid and the second chamber is used to reject the fluid.
2-stage pumps are typically used for applications where there is a need to move fluid in two different directions. This type of pump is especially useful for applications such as water treatment, paper manufacturing, and oil and gas production.
2-stage pumps are also commonly used in industrial applications such as wastewater treatment and paint manufacturing. They are also popular in the agricultural industry because they are able to handle a variety of fluids.
2-stage pumps are often smaller than 1-stage pumps and they are easier to operate. They are also less expensive than 1-stage pumps, which makes them a good choice for many applications.
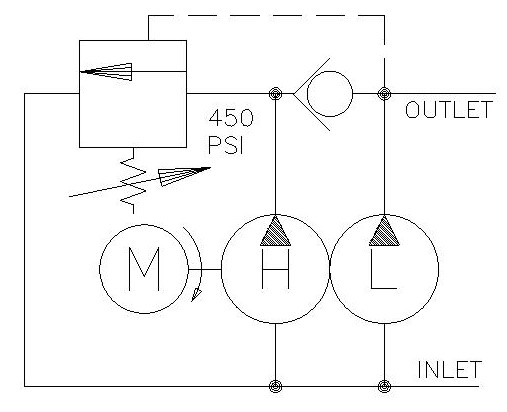
How a 2-stage hydraulic pump works?
A hydraulic pump is a machine that uses hydraulic pressure to move or control fluid. It is often used in industrial and commercial settings to move large amounts of fluid.
A 2-stage hydraulic pump works by using two pistons to create a pressure difference. This difference in pressure causes the fluid to flow through the pump.
What are the components of a 2 stage hydraulic pump?
A 2 stage hydraulic pump is a type of pump that transfers fluid from one container to another. The two stages of the pump are the suction and delivery stages.
The suction stage is where the pump draws fluid up from the lower chamber. The delivery stage is where the pump sends the fluid out to the target destination.
There are many different types of 2 stage hydraulic pumps, but they all share a common set of components. These components include the motor, valves, and manifolds.
The motor is responsible for moving the pistons in the delivery stage. The valves allow fluid to flow in and out of the manifolds, and they also control how fast fluid flows through the pump.
2 stage hydraulic pumps are essential for many different types of applications. They are used in industries such as automotive, food processing, and chemical manufacturing.
What is required for a 2 stage hydraulic pump to be used?
A 2 stage hydraulic pump is a type of reciprocating piston engine that uses two sets of pistons, one for each stage. This type of engine is used in many applications, including aircraft, automotive, engineering, and agricultural machinery.
A 2 stage hydraulic pump requires two sets of pistons: the cylinder block and the connecting rods. The cylinder block has two pistons that are connected by a shaft. The connecting rods have two pistons each that are also connected by a shaft.
The piston on the left side of the cylinder block moves up and down, while the piston on the right side moves up and down. The difference in height between these two pistons creates a backwards and forwards flow of pressurized fluid. This flow drives the engine forwards or backwards.
How to identify a 2 stage hydraulic pump
A 2 stage hydraulic pump is a type of pump that uses two pistons to move the fluid. The pistons are connected by a shaft, and the shaft moves the pistons back and forth. This type of pump is used in a variety of applications, including water pumps, oil pumps, and air compressors.
To identify a 2 stage hydraulic pump, look for the following features:
1. A two-stage piston mechanism
2. A three-point linkage between the pistons and the shaft
3. A cylindrical cover on the piston mechanism
The different types of 2 stage hydraulic pumps
A 2 stage hydraulic pump is a type of pump that is used to move liquids and gases. This type of pump is used in a variety of industries, including oil and gas production, water treatment, and food processing.
2 stage hydraulic pumps work by using two pistons to move the fluid. The first piston moves the fluid forward while the second piston moves the fluid backward. This combination allows the pump to move large amounts of fluid quickly.
There are a number of different types of 2 stage hydraulic pumps. Some pumps are designed for use in water while others are designed for use in oil or gas. Each type of pump has its own unique features and benefits.
If you are looking for a quality 2 stage hydraulic pump, be sure to visit our website. We have a wide selection of pumps that can meet your needs.
Types of fluids that can be pumped using a 2 Stage Hydraulic Pump
A 2 stage hydraulic pump is a type of fluid pump that can be used to move a variety of fluids. These pumps are commonly used to move oil, water, and gas.
2 stage hydraulic pumps are made up of two parts: the motor and the pump body. The motor is responsible for moving the fluid through the pump body.
There are a variety of types of 2 stage hydraulic pumps available on the market today. These pumps can be used to move a variety of fluids, including oil, water, and gas.
If you are looking for a versatile pump that can be used to move a variety of fluids, a 2 stage hydraulic pump is a good option.
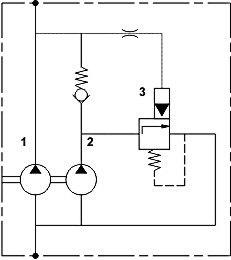
Advantages of a 2 stage hydraulic pump
A 2 stage hydraulic pump offers many advantages over a 1 stage pump. These benefits include:
1. Higher efficiency: A 2 stage pump is more efficient than a 1 stage pump. This means that it can produce more power with less energy expenditure.
2. Increased speed and torque: A 2 stage pump has greater speed and torque than a 1 stage pump. This means that it can move materials faster and with greater force.
3. Reduced noise: A 2 stage pump is quieter than a 1 stage pump. This means that it will not disturb the environment around it.
4. Higher reliability: A 2 stage pump is more reliable than a 1 stage pump. This means that it will not fail often, which will save you time and money.
5. More versatility: A 2 stage hydraulic pump can be used in many different applications than a 1 stage hydraulic pump can be used in. This increased versatility makes it an advantageous choice for businesses and professionals who need to move large quantities of material quickly and efficiently.
Disadvantages of a 2 stage hydraulic pump
A 2 stage hydraulic pump is a type of hydraulic pump that has two stages. The first stage is used to move the fluid, and the second stage is used to lift or lower the object.
The two main disadvantages of a 2 stage hydraulic pump are that it is less efficient than a 3 or 4 stage hydraulic pump, and it can be more difficult to operate.
A 3 or 4 stage hydraulic pump is generally more efficient than a 2 stage hydraulic pump, and it is easier to operate. Additionally, a 3 or 4 stage hydraulic pump can be used to move both fluids and objects.
Conclusion
A 2 stage hydraulic pump is a type of pump that uses two pistons to move the fluid. The first piston moves up and down, while the second piston moves side to side. This combination allows the pump to move a greater amount of fluid than either piston would on its own.
What is 2 stage hydraulic pump. please click topkitparts see more