Hydraulic pumps are an essential component of many machines and systems used in various industries such as construction, agriculture, and manufacturing. They are responsible for generating the necessary hydraulic pressure required for the system to function correctly. Understanding the different types of hydraulic pumps and their operation is crucial for selecting the right pump for a specific application and ensuring optimal system performance.This tutorial provides an overview of the different types of hydraulic pumps, their operation, applications, advantages, and limitations. It also discusses important factors to consider when selecting a hydraulic pump tutorial and common maintenance and troubleshooting practices. By the end of this tutorial, you will have a better understanding of hydraulic pumps and their role in various applications.

Hydraulic pumps come in different types, including gear pumps, vane pumps, and piston pumps. Each type has unique characteristics, advantages, and limitations that make it suitable for specific applications. Understanding the different types of hydraulic pumps is essential for selecting the right pump for a specific application.
Moreover, the tutorial will also discuss the importance of understanding hydraulic pumps in various applications. Hydraulic pumps play a vital role in various industries, and selecting the right pump for a specific application can result in optimal system performance, cost savings, and increased productivity.
In summary, this tutorial provides valuable insights into hydraulic pumps, their operation, and their applications. Understanding hydraulic pumps is crucial for selecting the right pump for a specific application, ensuring optimal system performance, and preventing costly repairs.
Gear Pumps
Gear pumps are one of the most common types of hydraulic pumps. They are positive displacement pumps that generate hydraulic pressure by forcing fluid through the gears’ meshing teeth. The gears rotate in opposite directions, trapping the fluid between the gear teeth and the pump casing, creating a pumping action that generates hydraulic pressure.
Applications and Advantages of Gear Pumps:
Gear pumps are commonly used in applications that require low to medium pressure and flow rates, such as in hydraulic power steering systems, machine tools, and small construction equipment. They are also popular in mobile applications due to their compact size and low cost.
One of the key advantages of gear pumps is their simplicity of design, making them easy to manufacture and maintain. They are also self-priming, meaning they can create suction to draw fluid from a reservoir without the need for external priming. Another advantage is that they have a relatively low noise level, making them suitable for applications that require quiet operation.
Disadvantages and Limitations of Gear Pumps:
Gear pumps have some limitations that make them unsuitable for certain applications. One of the limitations is that they are not suitable for high-pressure applications due to their design, which can lead to high levels of internal leakage. They are also not ideal for handling fluids with high viscosity or containing abrasive particles as this can cause damage to the gear teeth.
Moreover, gear pumps can experience significant wear over time due to their design, which can result in reduced performance and efficiency. They also have a limited range of flow rates, which can make it challenging to match them to specific system requirements.
In summary, gear pumps are commonly used in applications that require low to medium pressure and flow rates due to their simplicity, compact size, and low cost. However, they have limitations that make them unsuitable for high-pressure applications or applications that require handling fluids with high viscosity or abrasive particles. Understanding the advantages and limitations of gear pumps is crucial for selecting the right pump for a specific application.
Gear Pumps
Gear pumps are one of the most common types of hydraulic pumps. They are positive displacement pumps that generate hydraulic pressure by forcing fluid through the gears’ meshing teeth. The gears rotate in opposite directions, trapping the fluid between the gear teeth and the pump casing, creating a pumping action that generates hydraulic pressure.
Applications and Advantages of Gear Pumps:
Gear pumps are commonly used in applications that require low to medium pressure and flow rates, such as in hydraulic power steering systems, machine tools, and small construction equipment. They are also popular in mobile applications due to their compact size and low cost.
One of the key advantages of gear pumps is their simplicity of design, making them easy to manufacture and maintain. They are also self-priming, meaning they can create suction to draw fluid from a reservoir without the need for external priming. Another advantage is that they have a relatively low noise level, making them suitable for applications that require quiet operation.
Disadvantages and Limitations of Gear Pumps:
Gear pumps have some limitations that make them unsuitable for certain applications. One of the limitations is that they are not suitable for high-pressure applications due to their design, which can lead to high levels of internal leakage. They are also not ideal for handling fluids with high viscosity or containing abrasive particles as this can cause damage to the gear teeth.
Moreover, gear pumps can experience significant wear over time due to their design, which can result in reduced performance and efficiency. They also have a limited range of flow rates, which can make it challenging to match them to specific system requirements.
In summary, gear pumps are commonly used in applications that require low to medium pressure and flow rates due to their simplicity, compact size, and low cost. However, they have limitations that make them unsuitable for high-pressure applications or applications that require handling fluids with high viscosity or abrasive particles. Understanding the advantages and limitations of gear pumps is crucial for selecting the right pump for a specific application.
Vane Pumps
Vane pumps are another type of positive displacement hydraulic pump. They generate hydraulic pressure by trapping fluid between the vanes and the pump housing. As the vanes rotate, the trapped fluid is forced out of the pump at a high pressure.
Overview of Vane Pumps and their Operation:
Vane pumps consist of a cylindrical rotor with slots that hold sliding vanes. The rotor is eccentrically mounted within a circular pump casing, creating an elliptical space between the rotor and the casing. The vanes slide in and out of the rotor slots, maintaining contact with the casing and forming small chambers that fill and discharge fluid as the rotor rotates.
Applications and Advantages of Vane Pumps:
Vane pumps are commonly used in medium-pressure applications such as in hydraulic power steering systems, lifts, and industrial machinery. They have a relatively low noise level and are suitable for continuous operation due to their ability to maintain a constant flow rate.
One of the key advantages of vane pumps is their ability to handle low to medium viscosity fluids with ease. They also have a wide range of flow rates and can handle a range of pressures, making them suitable for various applications.
Disadvantages and Limitations of Vane Pumps:
Vane pumps also have some limitations that make them unsuitable for certain applications. One of the limitations is that they are not suitable for high-pressure applications as they can experience significant internal leakage due to their design.
Moreover, vane pumps can also experience significant wear over time, which can result in reduced efficiency and performance. They are also not ideal for handling fluids with high viscosity or containing abrasive particles, as this can cause damage to the vanes and casing.

In summary, vane pumps are commonly used in medium-pressure applications and can handle low to medium viscosity fluids with ease. However, they have limitations that make them unsuitable for high-pressure applications or applications that require handling fluids with high viscosity or abrasive particles. Understanding the advantages and limitations of vane pumps is crucial for selecting the right pump for a specific application.
Piston Pumps
Piston pumps are positive displacement pumps that generate hydraulic pressure by reciprocating a piston within a cylinder. The piston’s movement creates a suction and discharge action that generates hydraulic pressure.
Overview of Piston Pumps and their Operation:
Piston pumps consist of a cylinder, a piston, and inlet and outlet valves. The piston moves back and forth within the cylinder, drawing in fluid during the suction stroke and discharging it during the discharge stroke. The inlet valve opens during the suction stroke, allowing fluid to enter the cylinder, while the outlet valve opens during the discharge stroke, allowing fluid to exit the cylinder.
Piston pumps can be further classified into two types: axial piston pumps and radial piston pumps. Axial piston pumps have pistons that are arranged in a circular pattern and reciprocate parallel to the cylinder’s axis. Radial piston pumps have pistons that are arranged radially and reciprocate perpendicular to the cylinder’s axis.
Applications and Advantages of Piston Pumps:
Piston pumps are commonly used in high-pressure applications such as in hydraulic presses, heavy machinery, and construction equipment. They are capable of generating high pressures and flow rates, making them suitable for demanding applications.
One of the key advantages of piston pumps is their efficiency, which can result in lower energy consumption and reduced operating costs. They also have a long lifespan and can handle fluids with high viscosity and containing abrasive particles.
Disadvantages and Limitations of Piston Pumps:
Piston pumps also have some limitations that make them unsuitable for certain applications. One of the limitations is their high cost and complexity, which can make them less attractive for low-pressure applications or applications with a limited budget.
Moreover, piston pumps can experience significant wear over time due to their reciprocating action, which can result in reduced efficiency and performance. They are also more prone to cavitation than other types of hydraulic pumps, which can result in damage to the pump and other system components.
In summary, piston pumps are commonly used in high-pressure applications and can handle fluids with high viscosity and containing abrasive particles. However, they have limitations that make them unsuitable for low-pressure applications or applications with a limited budget. Understanding the advantages and limitations of piston pumps is crucial for selecting the right pump for a specific application.
Other Types of Hydraulic Pumps
In addition to gear pumps, vane pumps, and piston pumps, there are other types of hydraulic pumps that are less common but still have unique characteristics and applications.
- Screw Pumps: Screw pumps are positive displacement pumps that generate hydraulic pressure by trapping fluid between two screw-shaped rotors. They are commonly used in applications that require high flow rates and low to medium pressure.
- Peristaltic Pumps: Peristaltic pumps are positive displacement pumps that use a series of rollers to compress a flexible tube, creating a pumping action that generates hydraulic pressure. They are commonly used in applications that require gentle fluid handling, such as in the pharmaceutical and food industries.
- Diaphragm Pumps: Diaphragm pumps are positive displacement pumps that use a flexible diaphragm to generate hydraulic pressure. They are commonly used in applications that require handling abrasive or corrosive fluids or applications that require a high degree of contamination control.
- Gerotor Pumps: Gerotor pumps are positive displacement pumps that generate hydraulic pressure by trapping fluid between a rotor and a stator. They are commonly used in applications that require low to medium pressure and flow rates, such as in automotive and industrial applications.
Comparison to More Common Types of Hydraulic Pumps:
Each type of hydraulic pump has unique characteristics, advantages, and limitations that make it suitable for specific applications. Understanding the different types of hydraulic pumps and their operation is crucial for selecting the right pump for a specific application.
In summary, while gear pumps, vane pumps, and piston pumps are the most common types of hydraulic pumps, there are other types of pumps that have unique characteristics and applications. Understanding the advantages and limitations of each type of pump is crucial for selecting the right pump for a specific application.
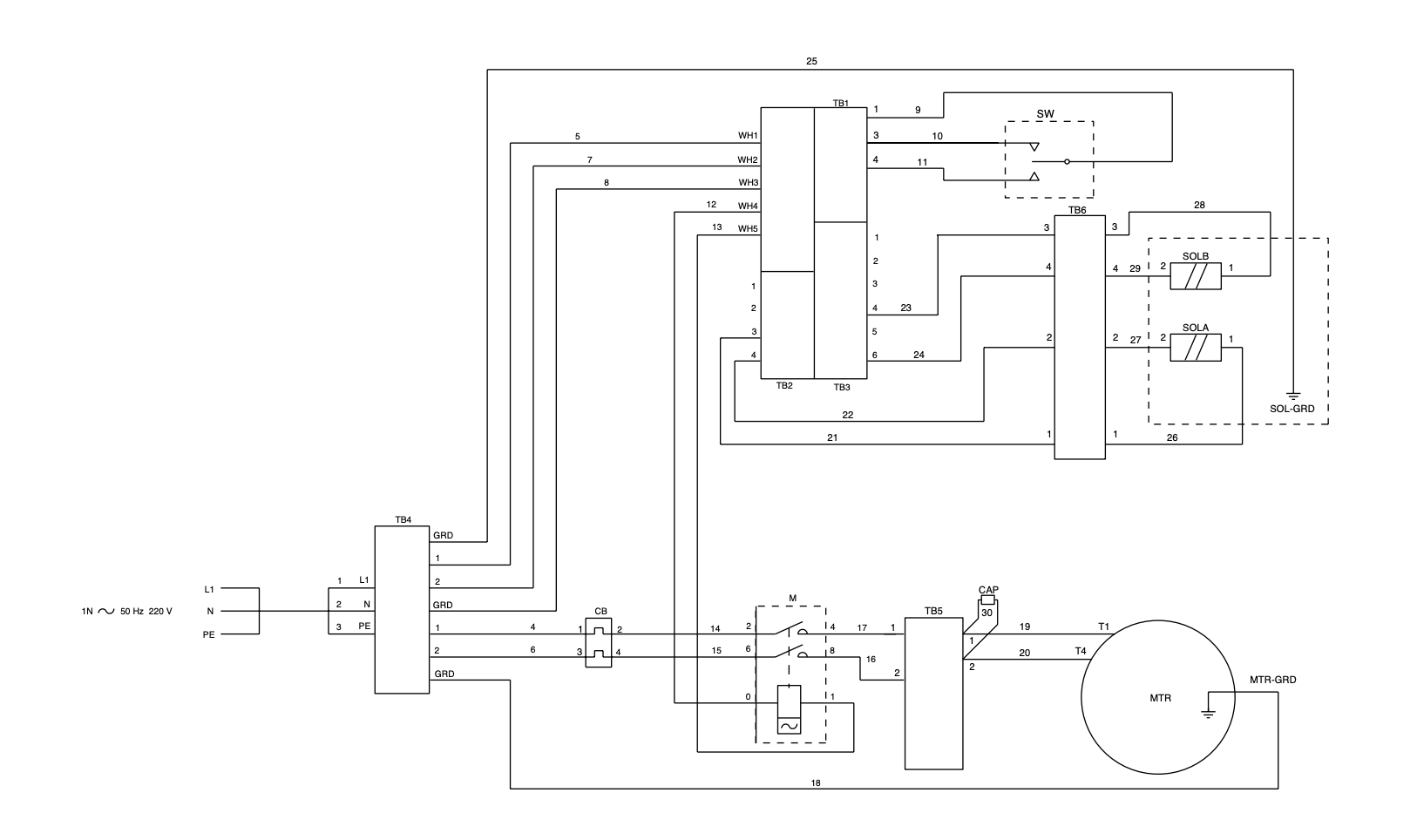
Factors to Consider When Selecting a Hydraulic Pump
Selecting the right hydraulic pump tutorial for a specific application requires considering several important factors. These factors can affect pump performance, efficiency, and application suitability.
- Fluid Properties: The fluid properties, including viscosity, temperature, and chemical composition, can affect the pump’s ability to generate hydraulic pressure and its lifespan. It is important to select a pump that is compatible with the fluid being pumped and can handle the required viscosity and temperature range.
- Flow Rate: The required flow rate depends on the application’s demands, and it is crucial to select a pump that can provide the required flow rate. It is also important to consider the system’s flow path and the pressure losses due to friction, which can affect the pump’s performance.
- Pressure: The required pressure depends on the application’s demands and can vary from low to high pressure. It is important to select a pump that can generate the required pressure without excessive wear or internal leakage.
- Efficiency: The pump’s efficiency can affect the operating cost and lifespan of the system. It is important to select a pump with high efficiency to minimize energy consumption and reduce maintenance costs.
- Size and Weight: The size and weight of the pump can affect the system’s design and installation. It is important to select a pump that is compact and lightweight, especially in mobile applications.
- Noise Level: The noise level can affect the system’s operation and environment. It is important to select a pump with a low noise level, especially in applications that require quiet operation.
- Cost: The cost of the pump can affect the system’s budget and overall cost-effectiveness. It is important to select a pump that provides the required performance at a reasonable cost.
Tips and Guidelines for Selecting the Right Hydraulic Pump:
- Consult with a hydraulic system designer or manufacturer for guidance on selecting the right pump for a specific application.
- Consider the entire hydraulic system, including the pump, reservoir, valves, and actuators, when selecting a pump.
- Consider the system’s future needs and potential changes when selecting a pump to ensure its long-term suitability.
- Always choose a pump from a reputable manufacturer with a proven track record of reliability and performance.
In summary, selecting the right hydraulic pump for a specific application requires considering several important factors, including fluid properties, flow rate, pressure, efficiency, size and weight, noise level, and cost. Following the tips and guidelines for selecting the right pump can help ensure a successful and cost-effective hydraulic system.
Maintenance and Troubleshooting of Hydraulic Pumps
Proper maintenance and troubleshooting of hydraulic pumps are crucial for maintaining their efficiency, performance, and lifespan. Neglecting maintenance can lead to increased operating costs, reduced system performance, and even equipment failure. Here are some maintenance practices and troubleshooting methods for hydraulic pumps.
Maintenance Practices:
- Regular Inspection: Regular inspection of the hydraulic pump and system can help identify potential issues before they become major problems. Inspections should include checking for leaks, wear, and contamination.
- Fluid Quality: Maintaining proper fluid quality is essential for the pump’s lifespan and performance. The fluid should be checked and changed regularly, and it should be compatible with the pump’s material and designed for the specific application.
- Filter Maintenance: Filters play a crucial role in removing contaminants from the hydraulic system. Regular filter maintenance, including cleaning and replacement, is essential for ensuring proper filtration and system performance.
- Lubrication: Proper lubrication is essential for maintaining the pump’s efficiency and reducing wear. It is important to use the recommended lubricant and follow the manufacturer’s recommendations for lubrication frequency and amount.
Troubleshooting Methods:
- Leakage: Leakage is a common issue with hydraulic pumps and can lead to reduced performance and even equipment failure. Leakage can be caused by worn seals, loose connections, or damaged components. Identifying and fixing the source of the leakage is crucial for maintaining proper pump performance.
- Excessive Noise: Excessive noise can be a sign of pump wear or damage. It is important to identify and fix the source of the noise to prevent further damage and maintain proper pump performance.
- Loss of Pressure: Loss of pressure can be caused by several factors, including worn components, internal leakage, or contamination. Identifying and fixing the source of the pressure loss is crucial for maintaining proper pump performance.
- Overheating: Overheating can be caused by several factors, including excessive pressure, inadequate cooling, or low fluid levels. It is important to identify and fix the source of the overheating to prevent further damage and maintain proper pump performance.
Importance of Proper Maintenance:
Proper maintenance of hydraulic pumps is crucial for maintaining their efficiency, performance, and lifespan. Neglecting maintenance can lead to increased operating costs, reduced system performance, and even equipment failure. Regular inspection, fluid quality maintenance, filter maintenance, and lubrication are essential for ensuring proper pump performance and longevity.
In summary, proper maintenance and troubleshooting of hydraulic pumps are crucial for maintaining their efficiency, performance, and lifespan. Regular inspection, fluid quality maintenance, filter maintenance, and lubrication are essential for ensuring proper pump performance and longevity. Identifying and fixing common issues such as leakage, excessive noise, loss of pressure, and overheating is also crucial for maintaining proper pump performance.
Conclusion
Understanding hydraulic pumps is crucial for selecting the right pump for a specific application and maintaining its efficiency, performance, and lifespan. Gear pumps, vane pumps, and piston pumps are the most common types of hydraulic pumps, each with unique characteristics, advantages, and limitations. However, other types of pumps, such as screw pumps, peristaltic pumps, diaphragm pumps, and gerotor pumps, also have their applications and advantages.
Factors to consider when selecting a hydraulic pump include fluid properties, flow rate, pressure, efficiency, size and weight, noise level, and cost. Following the tips and guidelines for selecting the right pump can help ensure a successful and cost-effective hydraulic system. Proper maintenance and troubleshooting of hydraulic pumps, including regular inspection, fluid quality maintenance, filter maintenance, and lubrication, are essential for maintaining proper pump performance and longevity.
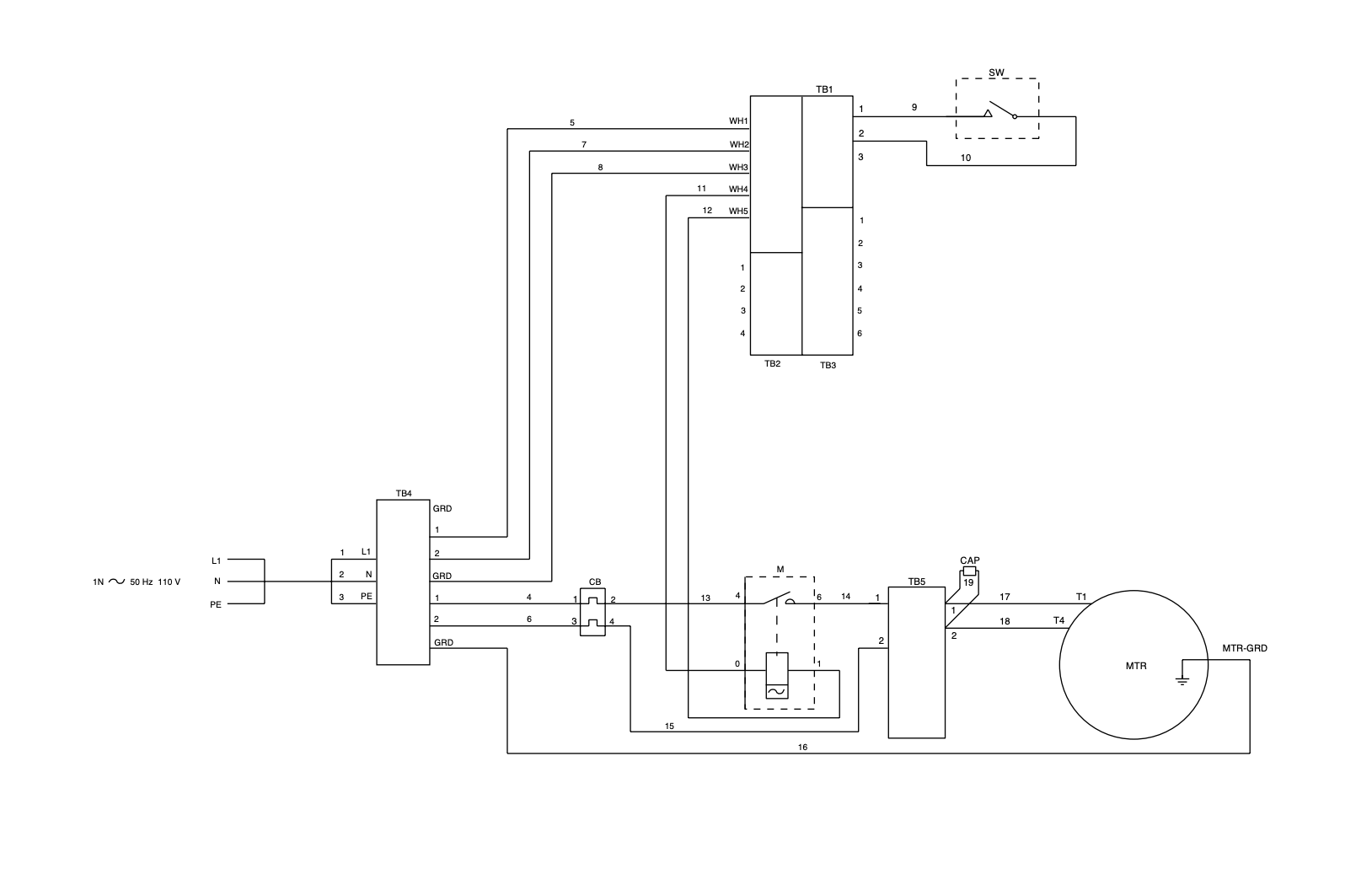
In conclusion, understanding different types of hydraulic pumps, factors to consider when selecting a pump, and maintenance practices and troubleshooting methods are crucial for maintaining a successful hydraulic system. Proper selection, maintenance, and troubleshooting of hydraulic pumps can lead to increased efficiency, reduced operating costs, and improved system performance, ensuring a successful and long-lasting hydraulic system.