Hydraulic flow rates are a critical part of hydraulic systems, and understanding how to increase them can help you optimize your equipment. In this article, we’ll discuss five common ways to increase hydraulic flow rate and give you tips on how to measure and calculate each one.
1. By increasing the size of the pump
One common way to increase hydraulic flow rate is to increase the size of the pump. This can be done by upgrading to a larger pump or by using multiple pumps in parallel.
2. By increasing the pressure of the system
Another way to increase hydraulic flow rate is to increase the pressure of the system. This can be done by installing a higher-pressure pipeline or by using a more powerful pump.
3. By adding more turbines
Another way to increase hydraulic flow rate is to add more turbines. This can be done by purchasing an additional turbine or building your own turbine system.
4. By increasing the horsepower of the engine
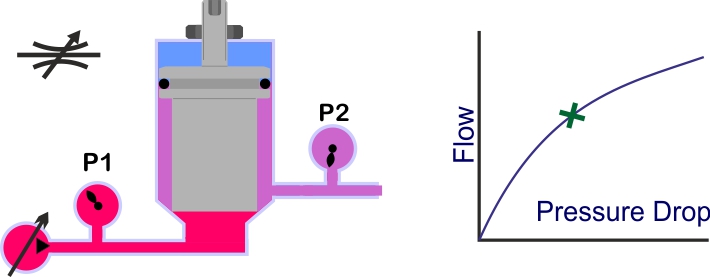
What is hydraulic flow rate?
Hydraulic flow rate is the rate at which hydraulic fluid is flowing through a pipe or pipeline. It’s important to keep hydraulic flow rate high so that the machinery can move fluid quickly and efficiently.
Hydraulic fluid can flow at different rates depending on the pressure and temperature involved. A high hydraulic flow rate is important for things like water pumps, irrigation systems, and oilfield equipment.
Hydraulic flow rate basics
Most hydraulic systems are designed to flow a certain amount of fluid per minute (GPM). However, the actual flow rate can be significantly lower if the system is not operating at its optimal efficiency. Here are a few tips to help increase your system’s flow rate:
1. Check the system’s overall efficiency. This can be determined by reviewing fluid usage records or by using an efficiency meter. Correct any problems before proceeding.
2. Clean and lube the system as needed. A clean and well-maintained system will run more efficiently and produce a higher flow rate.
3. Use proper pipeline sizing. Too large of a pipeline will not allow the system to operate at its maximum output, while too small of a pipeline can cause excessive wear and tear on the system components.
4. Use correct fluid pressures. Overpressuring the system can damage components or even cause it to rupture. Follow manufacturers’ recommendations for pressure ratings for your specific hydraulic equipment.
Factors that Influence Hydraulic Flow Rate
There are many factors that can influence hydraulic flow rate and the rate at which a hydraulic system can move fluid. Some of these factors include the size and type of hydraulic system, the design of the hydraulic system, the upstream and downstream mechanical equipment, and the operating conditions.
The size and type of the hydraulic system
The size and type of the hydraulic system can influence the flow rate. For example, a large hydraulic system with many pumps may move fluid at a slower rate than a small hydraulic system with only one pump.
The design of the hydraulic system
The design of the hydraulic system also can influence the flow rate. For example, a closed-loop system with many interconnected pipes will move fluid at a faster rate than a open-loop system with only one pipe.
The upstream and downstream mechanical equipment
The upstream and downstream mechanical equipment can also influence the flow rate. For example, if there is a lot of resistance to movement in the upstream or downstream equipment, the flow rate will be slower.
The operating conditions
Factors to consider in increasing hydraulic flow rate
When it comes to increasing hydraulic flow rate, there are a few things you need to take into account. Here are some of the most important factors:
1) The size of the hydraulic system
2) The type of hydraulic fluid used
3) The design of the hydraulic system
4) The type and size of valves used
5) The operating conditions of the system
Why does hydraulic flow affect pressure?
A hydraulic system consists of two main components: the pump and the reservoir. The pump is used to move fluid from the reservoir to the desired location. The pressure in the system is determined by how much fluid is moving through the pump and how much resistance is encountered along the way.
The pressure in the system is affected by the flow rate of the hydraulic fluid and the pressure differential between the reservoir and the pump. The higher the flow rate, the greater the pressure difference, and the higher the pressure, the greater the flow resistance.
Why is increase hydraulic flow rate important?
There are many reasons why increasing hydraulic flow rate is important. The most obvious reason is that it can increase the speed of a machine or the efficiency of a process. It can also help to decrease the amount of noise and vibration that is produced. Additionally, increased hydraulic flow rate can also improve the quality of the finished product.
Some other reasons why increasing hydraulic flow rate is important include the following:
It can help to decrease the amount of time that it takes to complete a task.
It can help to reduce the amount of energy that is used in a process.
It can help to improve the accuracy of a machine or process.
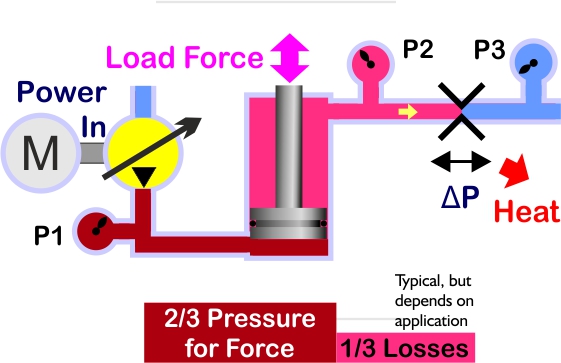
Steps to increase hydraulic flow rate
Increasing hydraulic flow rate can be done by altering the valves and fittings, increasing the size of the channel, and using a higher pressure pump.
Valves and fittings:
-Valves can be adjusted to change the amount of water flowing through them.
-Fitting sizes can also be changed to increase or decrease the flow rate.
-Using a higher pressure pump can increase the flow rate even more.
Channel size:
-The size of the channel can be altered by widening or narrowing it.
-Smaller channels will result in lower flow rates, while wider channels will result in higher flow rates.
-When altering the channel size, it is important to maintain the same cross-sectional area throughout. This will ensure that fluid is able to travel freely throughout the system.
High pressure pump:
-A high pressure pump can be used to increase the flow rate of a hydraulic system significantly.
Conclusion
Hydraulic flow rate is one of the most important factors when it comes to hydraulic systems. It determines how much fluid can be transferred per unit time and, as such, has a significant impact on the performance of a hydraulic system. This article will teach you how to increase your hydraulic flow rate using various methods. So if you’re looking to improve the performance of your hydraulic system, read on!
How do you increase hydraulic flow rate,please click topkitparts see more