Hydro pumps are essential devices in irrigation systems, used to move water from a storage reservoir to fields or garden areas. When they break down, it can be hard to determine the best course of action for repairing them. In this article, we will explain the different types of hydro pumps and discuss the different types of repairs that can be carried out on them.
What is a hydro pump?
A hydro pump is a device that uses water to move objects, such as rocks and soil. Hydro pumps are used in mines, quarries, and other places where water is needed to move heavy objects.
How do you repair a hydro pump?
There are many different types of hydro pumps, but the most common one is the electric pump. When it breaks, the most common problem is that the motor stop working. To fix this, you first have to determine if the motor is faulty or if there’s something wrong with the wiring. If the wiring is faulty, you will have to replace it. If the motor is faulty, you will need to replace it or fix it.
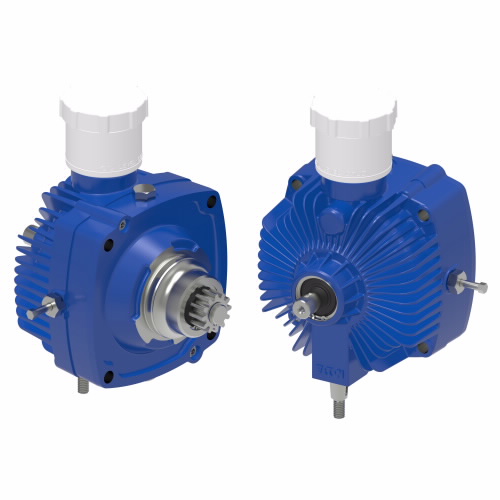
How does a hydro pump work?
A hydro pump is a machine that uses water to move objects, as opposed to gasoline or other combustion engines. Hydro pumps are often used to move objects up and down rivers, but they can also be found in many industrial settings. The most common type of hydro pump is the centrifugal pump, which uses spinning disks to create a flow of water.
When you turn on a hydro pump, water starts flowing out of the reservoir. The spinning disks force the water through the pump impeller and into thetonic flow (a type of flow that is constantly moving in one direction). This churns up the water particles and creates a powerful flow. The hydropump can then push objects around or move large amounts of water quickly.
Common Causes of Hydro Pump Problems
There are a few common causes of hydro pump problems, and each one can be repaired in a different way. Here are the five most common:
-A clog in the pump mechanism
-A broken impeller
-A worn out belt or pulley
-A damaged pump head
-A bad switchIf you notice that your hydro pump is not working properly, it’s important to take action and figure out the cause as soon as possible. If the problem is a clog in the pump mechanism, you may be able to clear it using a plunger or a vacuum cleaner. If the issue is a broken impeller, you will need to replace the pump head. If the belt or pulley is worn out, it will need to be replaced. If the problem is with the switch, you may be able to fix it yourself.
Common Solutions for Hydro Pump Problems
Most common repairs for hydro pumps are replacing the pump, diaphragm, or check valve. Hydro pump problems can often be diagnosed by checking the pressure gauge and comparing it to the manufacturer’s specifications.
If the pressure is low or not rising with use, the pump may need to be replaced. If the pressure is high but not increasing with use, the diaphragm may need to be replaced. If the pressure is high and increasing with use, the check valve may need to be replaced.
Precautions when repairing a hydro pump
Repairing a hydro pump is a relatively simple process, but there are a few things to keep in mind to avoid damaging the pump or yourself. First, always wear gloves and eye protection when working with the pump. Second, make sure to use the correct sealant and lubricants when repairing the pump. Finally, be sure to follow all safety guidelines when working with hydro pumps.
If you need help repairing a hydro pump or any other water-related issue, don’t hesitate to reach out to our team at Water Damage Restoration Company. We have decades of experience working with all types of water damage and can help get your home or business back up and running as quickly and safely as possible.
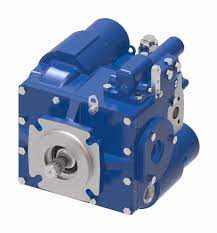
How long does it take to repair a hydro pump?
There is not a one-size-fits-all answer to this question since the time required to repair a hydro pump will vary depending on the severity of the damage, the age of the pump, and the skills and tools that are available. However, in general, most hydro pumps can be repaired within a few hours by a skilled technician.
The most common repairs involve replacing failed parts such as seals, bearings, or impellers. Other repairs may involve tightening or replacing bolts or adjusting valves.
In most cases, it is important to properly clean and lubricate all moving parts before repairing them.
How much does it cost to make repairs to a hydro pump?
Hydro pumps are important pieces of machinery in any water system and are used to move water from a reservoir to a tap or other use. Hydro pumps can be damaged by a number of things, including improper installation or maintenance, physical damage, or corrosion.
If you notice that your hydro pump is not moving water as it should, the first thing to do is to check the installation. Make sure that the pump is installed properly on the foundation and that the pipes connecting it to the reservoir are properly sealed. If the installation looks good, look for signs of physical damage. If you see any broken pieces or leaks, your pump may need to be replaced. Finally, check for signs of corrosion. If there are any areas where the metal is beginning to rust, your pump may need to be replaced.
Conclusion
If you have a hydro pump that needs repair, there are a few things you need to do in order to get it back up and running as quickly and efficiently as possible. Make sure you have the right tools and supplies on hand before starting work, and be prepared to work diligently for a few hours in order to get your pump fixed up as good as new.
How do you repair a hydro pump,please click topkitparts see more