Hydraulic pumps are one of the most common types of pumps used in industry. They are used to move fluids and gases, and can be found in everything from factories to water treatment plants. Knowing the different types of hydraulic pumps can help you choose the right one for your needs.
What is a hydraulic pump?
A hydraulic pump is a machine that uses the force of an engine or hydraulics to move fluid. There are many different types of hydraulic pumps, each with its own specific purpose. Here are just a few of the most common:
Pumpjack: This type of pump is used in oil and gas production. It works by using a rotating shaft to create a upward flow of fluid.
Diesel engine: A diesel engine is often used to power hydraulic pumps. It’s a powerful engine that can produce a lot of torque, which is needed to operate a pump efficiently.
Axial flow pump: This type of pump is used to move fluids in circles or along straight lines. It’s often used in industrial settings, where it’s necessary to move large amounts of water or other liquids quickly and efficiently.
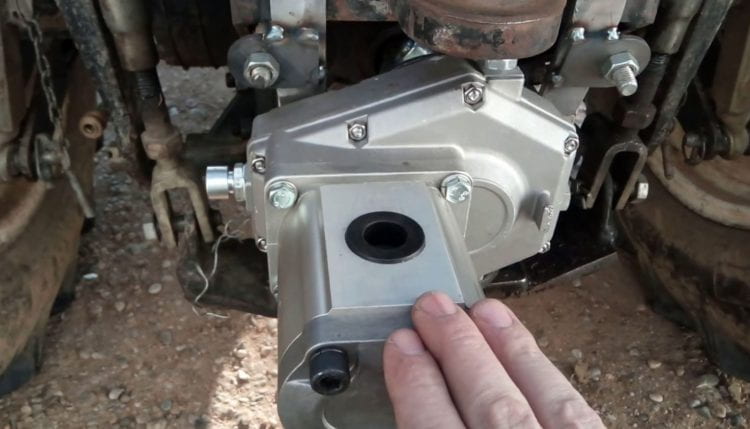
What are the characteristics of a hydraulic pump?
A hydraulic pump is a machine that uses the power of hydraulics to move fluids. There are many types of hydraulic pumps, each with its own unique characteristics. Here are four of the most common types of hydraulic pumps: displacement, impulse, rotary and vane pumps.
Displacement pumps work by transferring a fixed amount of fluid per stroke. They are usually used to move liquids or slurries between two points. Impulse pumps transfer a fixed amount of fluid in a short period of time. Rotary pumps use a rotating disk to generate motion, and vane pumps use vanes to create motion.
How do hydraulic pumps work?
There are many types of hydraulic pumps, but all work by using the pressure of the fluid in the cylinder to move a piston or plunger. The most common types of hydraulic pumps are:
Valves-Avalon series pumps use a diaphragm valve to control the flow of fluid into and out of the pump. The diaphragm can be opened and closed by a cam on the engine or pump drive, which in turn control the pressure in and out of the cylinder. These pumps are used on boat motors and other applications where high volume flow rates are required.
Gear Pumps-Gear pumps are some of the most common types of pumps because they can handle high pressures and low flows with little loss in performance. Gear pumps use a gearbox to transfer power from the engine to the pump, which allows them to operate at high speeds while still maintaining low noise levels. Gear pumps are used in automotive applications, water treatment plants, and numerous industrial settings.
Axial Flow Pumps-Axial flow pumps use an impeller on one side of the pump to create a rotating force that causes the fluid to move in a straight line. This type of pump is often used in
Types of hydraulic pumps
Hydraulic pumps come in many different types, each with its own specific purpose. Here are the most common types of hydraulic pumps:
-Piston pump: This type of pump is usually used to move fluids or solids. It uses pistons to push and pull the fluid or object.
-Vacuum pump: This type of pump is used to create a vacuum. Vacuum pumps are often used in manufacturing and engineering to remove air or gas from a container.
-Pressure pump: This type of pump is used to increase or decrease the pressure inside a container. Pressure pumps are often used in mining, drilling, and manufacturing.
Types of Pump Applications
There are a variety of hydraulic pumps available on the market, geared to meet the specific needs of different industries. Here’s a look at the most common types and their applications.
Pump Types
There are four main types of hydraulic pumps: contact, impulse, centrifugal and rotary.
Contact Pumps: These pumps use push/pull principles to transfer energy from one fluid to another. They’re used in industries such as mining, manufacturing and construction, where they’re used to move fluid substances through pipes or other conduits. Contact pumps come in both diaphragm and sleeve varieties and are typically less expensive than other types of pumps.
Impulse Pumps: Impulse pumps work similarly to contact pumps, but instead of using push/pull principles, they use a piston to create an impulse force that causes the transfer of energy. Impulse pumps are more powerful and are used in industrial settings where high forces are required, such as in oil production. They also have higher operating costs than contact pumps.
Centrifugal Pumps: Centrifugal pumps use a principle called Bernoulli’s Law which states that as
Pros and Cons of the different types of pumps
There are a variety of hydraulic pumps available on the market today. Each has its own advantages and disadvantages, which should be considered before making a purchase. Here is a brief overview of the most common types of hydraulic pumps:
-Piston pump: The piston pump is the most common type of hydraulic pump and is used in applications where high reliability and low noise are important. They are also effective at moving large amounts of fluid quickly. However, they are not as efficient as other types of pumps when it comes to moving smaller quantities of fluid or when the application requires high torque.
-Rotary vane pump: The rotary vane pump is similar to a piston pump, but it uses a series of vanes to move the fluid instead of pistons. This makes them more efficient than piston pumps when it comes to moving small quantities of fluid or when the application requires high torque. They also have less noise than piston pumps, making them well-suited for applications where noise is an issue. However, they can be more expensive than piston pumps and can take longer to start up.
-Water displacement pump: The water displacement pump is unique in that it uses pressurized water instead of oil
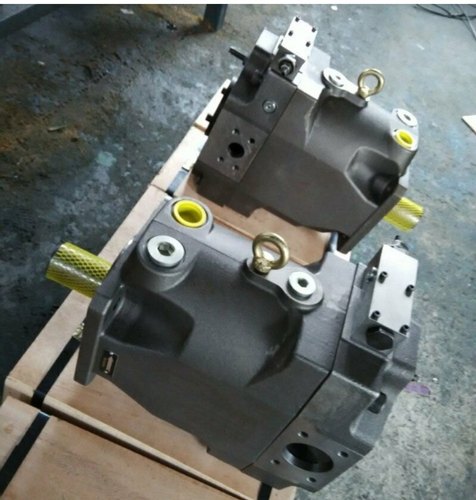
What can go wrong with a pump?
Hydraulic pumps are essential for many industrial and commercial applications, but like any mechanical device they can malfunction. This can lead to a variety of problems, including failure of the pump or its associated equipment, loss of fluid, and environmental contamination. In this article we’ll take a look at some of the most common types of hydraulic pumps and their potential problems.
Types of Hydraulic Pumps
There are a variety of different types of hydraulic pumps available on the market, each with its own unique features and capabilities. Here are four of the most common types:
Piston Pump: This type of pump is powered by a piston moving inside a cylinder. The piston is typically driven by an engine or other external power source, and it can be used to transfer water, oil, or other fluids between two points. Piston pumps are relatively simple and rugged, making them well-suited for industrial applications where reliability is key. However, they can be less efficient than other types of pumps when it comes to transferring liquids at high volumes or speeds.
Rotary Pump: Rotary pumps are similar in principle to piston pumps, but they use a spinning impeller instead of a piston. This
How to avoid pump failure
hydraulic pumps are used in a variety of industries to convey fluid. There are many different types of hydraulic pumps, each with its own advantages and disadvantages. When choosing a pump, it is important to understand the types available and choose the one that best suits your needs. Here are four tips to help you avoid pump failure:
1. Choose the right type of pump for the task at hand. Different types of pumps are better suited for different jobs. For example, centrifugal pumps are good for high-speed operations, while diaphragm pumps are better for low-speed applications.
2. Inspect the pump regularly. Pump failures can happen unexpectedly, so it is important to keep an eye on them and inspect them regularly for signs of wear or damage. If you notice any problems, schedule an inspection as soon as possible.
3. Use quality parts. Poorly made parts can cause a pump to fail quickly. Always use quality parts when assembling or rebuilding a pump, and make sure they match the specifications of the original equipment manufacturer (OEM).
4. Choose the right application. Pumps are often designed for specific applications, so make sure you choose the right one for the
Conclusion
There are a number of different types of hydraulic pumps, each with its own benefits and drawbacks. If you’re in the market for a new pump, it’s important to understand which type is right for your needs before making a purchase. Hopefully, this article has helped you to make an informed decision about which hydraulic pump is best for your needs.
How many types of hydraulic pumps are there,please click topkitparts see more