Torque is the rotational force that moves a machine or tool. In hydraulic motors, torque is generated when the pressure of water in the motor vessel increases as the result of an increase in rpm. Torque can be increased in a hydraulic motor by increasing the rpm, by decreasing the fluid’s pressure or by increasing the amount of fluid. This article will explore each option in detail and provide tips on how to increase torque in a hydraulic motor.
Option 1: Increase the Rpm
One way to increase torque in a hydraulic motor is to increase the rpm. To do this, you will need to modify the machine or tool so that it can operate at a higher speed. You can also use gearing or a reduction gearbox to achieve this. It is important to note that higher rpm will also increase the risk of damage to the motor and machine. Always use caution when modifying or operating a hydraulic motor at high rpm.
Option 2: Decrease the Fluid’s Pressure
Another way to increase torque in a hydraulic motor is to reduce the pressure of the fluid inside the vessel. To do this, you will need to pump more fluid into the motor than you are using to power it. This will allow you to operate the machine at a lower rpm, which will in turn increase torque. However, reducing pressure often requires expensive equipment and may not be possible in all situations.
Option 3: Increase the Amount of Fluid
Another way to increase torque in a hydraulic motor is by increasing the amount of fluid used. This involves filling the motor vessel with more water than necessary and then using that extra water to power the machine. This approach is usually less effective
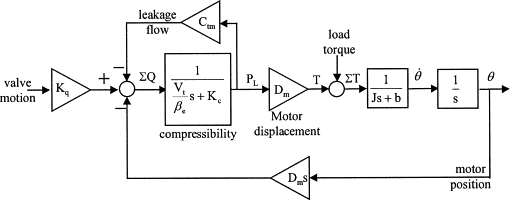
What is a hydraulic motor?
A hydraulic motor is a type of engine that uses hydraulic pressure to turn a shaft. This type of engine is often used in devices like lawn mowers, construction equipment, and aircraft. The main advantage of using a hydraulic motor is that it can produce a large amount of torque, which is the force that turns a shaft. This is why hydraulic motors are often used in devices that need to move quickly and require a lot of force. To increase torque in a hydraulic motor, you need to make sure that you have the right kind of gearbox and shaft. You also need to make sure that the hydraulic system is working properly.
Different types of hydraulic motors
Torque is the turning force that a hydraulic motor can generate. Torque can be increased by increasing the hydraulic pressure or by increasing the speed of the motor. Increasing the pressure will increase the torque, while increasing the speed will increase the RPM.
What is torque and what does it do?
Torque is a measure of the amount of force that can be applied to a rotating object. In engineering, torque is often used to describe the rotation of an object about its axis or about another rotational axis with which it is associated. Torque is also used in physics and engineering to describe the force that causes rotation or movement.
How does torque work in a hydraulic motor?
A hydraulic motor uses pressurized hydraulic fluid to turn a shaft. This rotating force creates a torque that can be used to drive a load. The amount of torque generated by a hydraulic motor is dependent on the pressure and volume of the hydraulic fluid used.
What Causes Torque Loss?
If you’re looking to increase torque in a hydraulic motor, the most common cause of torque loss is a worn or damaged belt. In order to counteract this, you’ll need to either replace the belt or install a new one. Additionally, if the shaft or bearing assembly is leaking, the oil will be forced out and this will also contribute to torque loss. Finally, if the motor is overheated, it will lose power and torque.
How to Increase Torque in a Hydraulic Motor
In order to increase torque in a hydraulic motor, it is important to understand the basic principles of hydraulic motors. A hydraulic motor uses fluid power to turn a shaft. The fluid is pressure pumped through a series of nozzles, which forces the fluid into and out of the motor. This creates a rotating force that can be harnessed to power machines or devices. There are several ways to increase torque in a hydraulic motor. One way is to increase the flow rate of the fluid. Another way is to add more nozzles or chambers to the motor. Finally, you can make modifications to the engine or pump that drives the motor.
Increasing the flow rate of the fluid is one way to increase torque in a hydraulic motor. You can increase the flow rate by increasing the size of the nozzles or by adding more nozzles to the motor. You can also make modifications to the engine or pump that drives the motor.
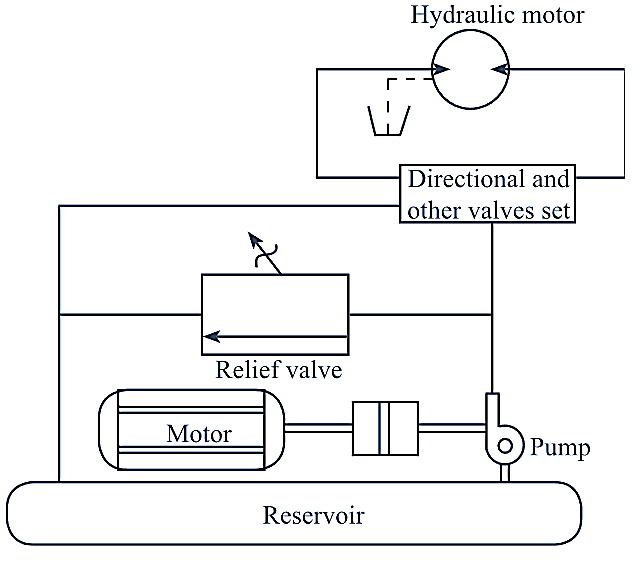
Why is torque important to hydraulic motors?
Torque is important because it is the rotational force that helps a hydraulic motor move objects. A high torque allows a hydraulic motor to move larger objects more easily than a low torque motor.
A better way to increase torque in a hydraulic moto
Most hydraulic motors have a certain amount of torque that they are capable of producing. Increasing the torque of a hydraulic motor can be done in a few different ways. One way to increase torque is to use a larger diameter hose. This will give you more leverage and allow you to produce more torque. Another way to increase torque is to use an increased number of pistons. This will allow you to create a higher pressure in the system, which will lead to greater torque output. Lastly, you can also use a gearbox to increase the speed at which the pistons are moving, which will also lead to greater torque output.
Conclusion
Increasing torque in a hydraulic motor can be a difficult task, but it is not impossible. There are a few things you can do to increase the amount of torque your motor can generate. First, make sure the bearing is in good condition and free from corrosion. Second, use high-quality oil in the transmission and bearings. Third, ensure that the gears are properly meshed and that there is no binding or friction between them. Finally, use proper maintenance procedures to keep your motor running at its best.
How do you increase torque in a hydraulic motor,please click topkitparts see more