A single-acting cylinder is a type of piston engine that uses air or steam to power the engine. As the piston moves up and down, it compresses the air or steam in the cylinder, which then sends power to the crankshaft. Single-acting cylinders are most often used in small engines, where efficiency is more important than power.
The disadvantage of using a single-acting cylinder is that it can be less powerful than a double-acting cylinder. Additionally, single-acting cylinders are not as efficient as double-acting cylinders when it comes to converting energy into motion.
Overall, the single-acting cylinder is a simple and efficient engine type, but it may not be as powerful or efficient as other engines options.
What is a Single-acting cylinder?
Single-acting cylinders are used in firearms that use a single round of ammunition. This type of cylinder holds only one cartridge and must be reloaded after each shot.
How do I clean a single-acting cylinder?
To clean a single-acting cylinder, first remove the cartridge and wipe down the cylinder with a cloth. Then, use a brass brush to clean any debris that may have accumulated on the inside of the barrel.
How does a single-acting cylinder work?
A single-acting cylinder is a type of air compressor that uses a piston to compress the air. This type of air compressor is less efficient than a double-acting cylinder, because it requires more energy to compress the air. Additionally, a single-acting cylinder can be more difficult to operate, because it requires more effort to start and stop the compressor.
Single-acting cylinders are most commonly used in applications where a higher compression ratio is desired, such as in agricultural equipment or automotive parts.
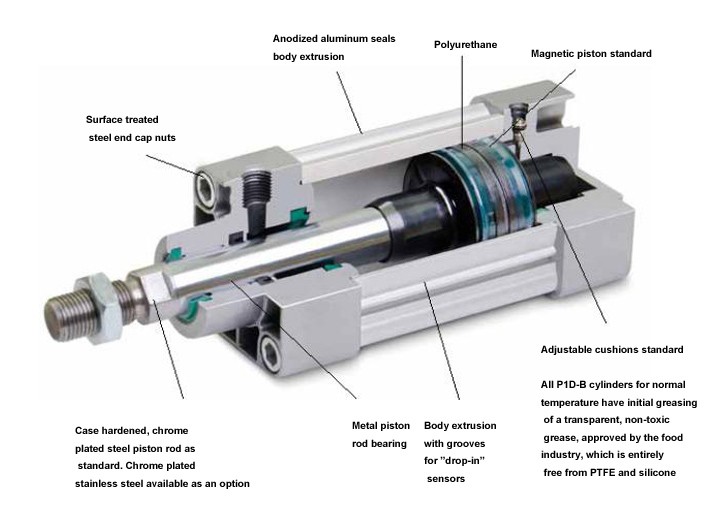
The single-acting cylinder is used in a variety of different industries including:
-Refrigeration
-Air conditioning
-Heating and cooling-Petroleum
-Chemical
The Disadvantages of a Single-acting Cylinder
One of the main disadvantages of using a single-acting cylinder is that the recoil might cause the gun to accidentally discharge. In addition, a single-acting cylinder doesn’t allow for an ejection sequence, which can lead to accidental discharges.
Additionally, a single-acting cylinder can be difficult to reload.
The Advantages of a Single-acting Cylinder
One of the advantages of using a single-acting cylinder is that it’s simpler and more compact than a double-action cylinder. Additionally, a single-action cylinder allows for an ejection sequence, which can help prevent accidental discharges.
Additionally, a single-acting cylinder is easier to reload than a double-action cylinder.
How to Choose a Cylinder for a Gun
When choosing a cylinder for a gun, it’s important to consider the type of firearm it will be used with and the intended use. Some factors to consider include the caliber of the gun, the type of ammunition it will use, and the amount of recoil it will experience.
What are some ways to fix these problems?
There are a few disadvantages to using a single-acting cylinder. One major disadvantage is that the valve must be manually operated, which can be difficult if the cylinder is in an inaccessible location. Additionally, if the cylinder becomes blocked, the pressure inside will rise until it bursts, potentially causing serious injury or even death.
To overcome these limitations, some companies have developed double-acting cylinders. These cylinders have two valves, one that opens when the pressure inside the cylinder reaches a certain level and a second valve that opens when the pressure inside the cylinder falls below a certain level. This design allows the cylinder to be operated with just one hand and prevents the pressure from building up until it breaches.
Another option is to use a piston-driven cylinder. These cylinders use a piston that is driven by air or another fluid. When the air or fluid is released, it pushes the piston down, which causes the valve to open. This design is more complicated than single- and double-acting cylinders, but it allows for greater range of motion and flexibility in terms of how the cylinder can be used.
Different types of engines that use a single-acting cylinder.
Single-acting cylinders are often used in engines that require a high compression ratio, such as diesel engines. This type of cylinder allows for a higher compression ratio because the piston does not have to travel back and forth between the intake and exhaust valves multiple times. However, this type of engine has a disadvantage in that it requires more fuel to operate than an engine that uses a double-acting cylinder.
Another type of engine that uses a single-acting cylinder is the gas turbine. This type of engine is used in aircrafts and spacecrafts because it is capable of generating a high amount of power.
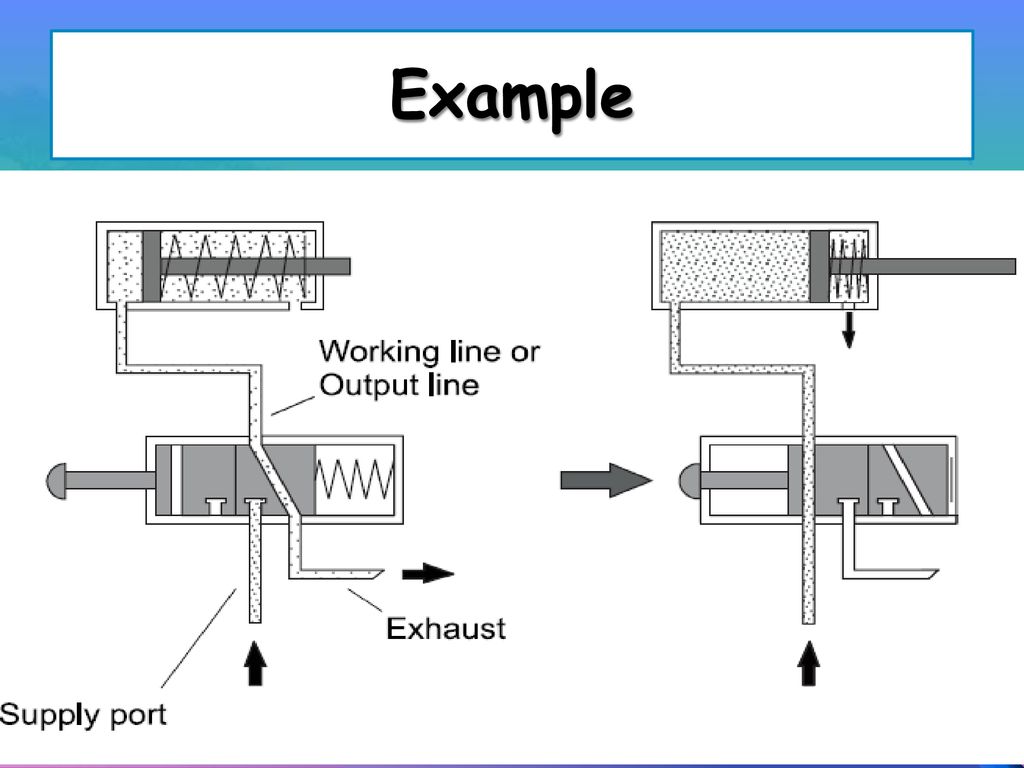
Which Type of Cylinder is Best for You?
When it comes to choosing the right type of cylinder for your needs, there are a few things to consider. A single-acting cylinder is great if you need to use relatively small amounts of air at a time, but a double-acting cylinder is better if you need to use larger amounts of air at a time. Additionally, single-acting cylinders require more effort to operate than double-acting cylinders, and they typically have a shorter lifespan.
If you need to use large amounts of air at a time, a double-acting cylinder is the best option. Additionally, if you plan on using your cylinder frequently, it is worth investing in a model with a longer lifespan.
Ultimately, the best type of cylinder for you depends on your specific needs. If you’re unsure which type of cylinder is best for you, consult with a specialist.
What are the Different Types of Cylinders?
There are a few different types of cylinders available on the market today: single-acting, double-acting, and rotary. Each type of cylinder has its own unique benefits and drawbacks, so it is important to choose the right model for your needs.
Single-Acting Cylinder: This type of cylinder requires more effort to operate than double-acting cylinders, and they typically have a shorter lifespan. Additionally, single-acting cylinders are best suited for use with relatively small amounts of air at a time.
Double-Acting Cylinder: This type of cylinder is better suited for use with larger amounts of air at a time, and they require less effort to operate than single-acting cylinders. Additionally, double-acting cylinders typically have a longer lifespan than single-acting cylinders.
Rotary Cylinder: This type of cylinder uses a rotating element to compress the air inside the cylinder. Rotary cylinders are ideal for applications that require high levels of pressure, such as welding or automotive repair.
Conclusion
There is no one-size-fits-all answer to this question, as the disadvantage of using a single-acting cylinder may vary depending on your specific needs and circumstances. However, some potential disadvantages of using a single-acting cylinder include:
• The need to regularly refill the cylinder
• Increased noise levels due to the pumping action• More difficult and time-consuming operation
What is the disadvantage of using a single-acting cylinde,please click topkitparts see more