When you’re looking to purchase a new water pump, it can be tough to figure out just how big of a pump you need. And even if you do know the size of the pump you need, figuring out the cost can be tricky. In this article, we’ll take a look at two ways to calculate the cost of a water pump, and provide some tips on how to get the best deal on your new pump.
What is a Pump?
A pump is a device that moves fluid. The most common type of pump is a water pump, which is used to move water or other liquids.
Pumps are also used to move air, gas, or other gases. Pumping stations are used to move water, gas, or oil from one place to another.
What are the different pump types?
There are many different types of pumps, and it can be hard to determine what size pump is necessary for your application. Here are a few tips to help you choose the right pump:
-Consider the flow rate required. Pumps with higher flow rates require larger sizes.
-Consider the type of fluid being pumped. Pumps designed for liquids will require larger sizes than pumps designed for gases.
-Think about whether you will be using the pump continuously or intermittently. A continuous-use pump will require a larger size than an intermittent-use pump.
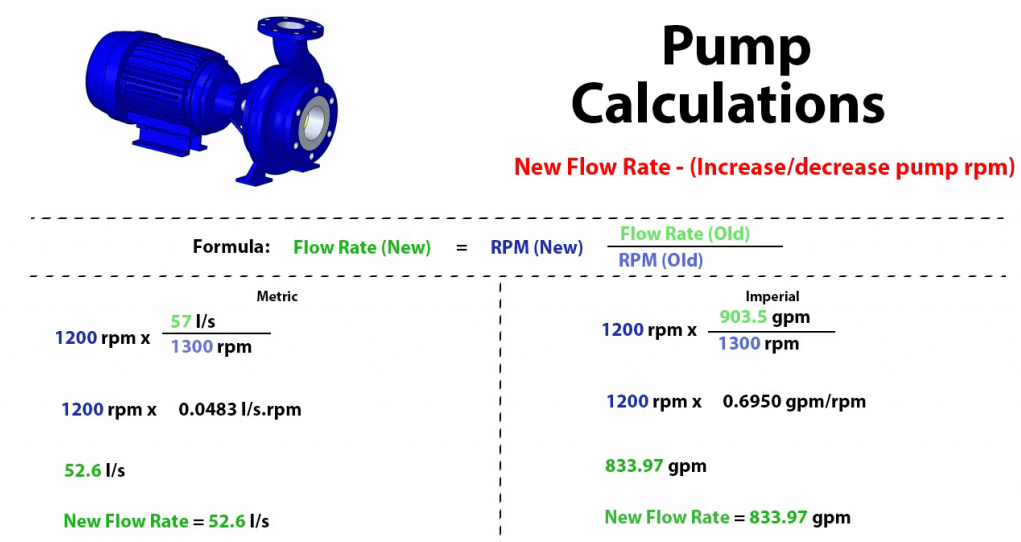
Why is size of pump important?
When you’re buying a new pump, the size of the pump is important. The bigger the pump, the more powerful it is and the more water it can move. However, not all pumps are created equal. So just because a pump is big, doesn’t mean it’s the right one for your application.
There are three main factors to consider when choosing a pump: flow rate (how much water per minute), head (the height of water above the pump), and discharge (the width of the hose).
Flow rate: The most important factor when choosing a pump is flow rate. A pump with a higher flow rate can move more water per minute than a smaller pump. For example, a 1 horsepower pump can move up to 1,500 gallons of water per minute while a 0.5 horsepower pump can only move 300 gallons per minute.
Head: Head is also important when selecting a pump. A larger head means the pump will be able to reach higher heights above the discharge pipe, which allows it to move more water per minute. For example, a 2-1/2 inch head pump can reach up to 12 feet above ground level while a 1-1/2 inch head pump can only reach 6
What are Some Factors That Influence My Pump Size?
When it comes to choosing the right pump for your needs, there are a few things you’ll need to take into account. Here are some of the most important factors:
-The amount of liquid you’ll be pumping
-The size and type of container you’re using
-Your pump’s power requirements
-Your work area’s dimensions (height, width, and depth)
-Your pumping speed
-How often you’ll be using the pump
Which size pump should I get?
Choosing the right pump for your application is important, not only because it will save you time and money, but also because the wrong pump can damage your equipment. In this article, we will outline some of the different factors to consider when choosing a pump and how to calculate the size needed.
When selecting a pump, you’ll need to consider the following:
-The application: What is the desired flow rate?
-The pressure required: How strong of a force will the pump produce?
-The size of the equipment: Will the pump fit in the designated area?
-The budget: How much money do you want to spend?
Once you have these factors in mind, you can begin to look at different pumps and calculate their sizes. The table below provides general guidelines for each of these three factors.
Application Pressure Flow Rate (L/min) Size (in.)
High Pressure Water Pumps 10,000 psi or more 1 – 10 2 ft. x 2 ft.
Low Pressure Water Pumps 1,000 psi or less 3 – 10 3 ft. x 3 ft.
Liquid Nitrogen Pumps N/A 19 – 100 2 ft. x 2 ft.
What is a Good Pump Size for Me?
When you’re thinking about getting a new pump, the first thing to consider is how much suction your current pump can produce. This number is usually listed on the pump’s packaging or on the pump itself. The higher the suction, the more powerful the pump will be. However, not all pumps are created equal when it comes to suction. So, if you’re not sure which size pump will work best for you, here are some tips to help you calculate what size pump is right for you:
-To determine how much suction your current pump can produce, measure the air pressure in your home with an air pressure gauge. The higher the reading on the gauge, the greater the air pressure inside your home. Now multiply that number by 1.15 to account for atmospheric pressure (the force of gravity).
-To find out how many cubic feet of air per minute (CFM) a particular pump can move, multiply the reading on your air pressure gauge by 1.5. For example, if your air pressure gauge reads 10 inches of mercury (inHg), and 1.5 multiplied that number equals 15 CFM, then a pump with a rating of 12 CFM would be
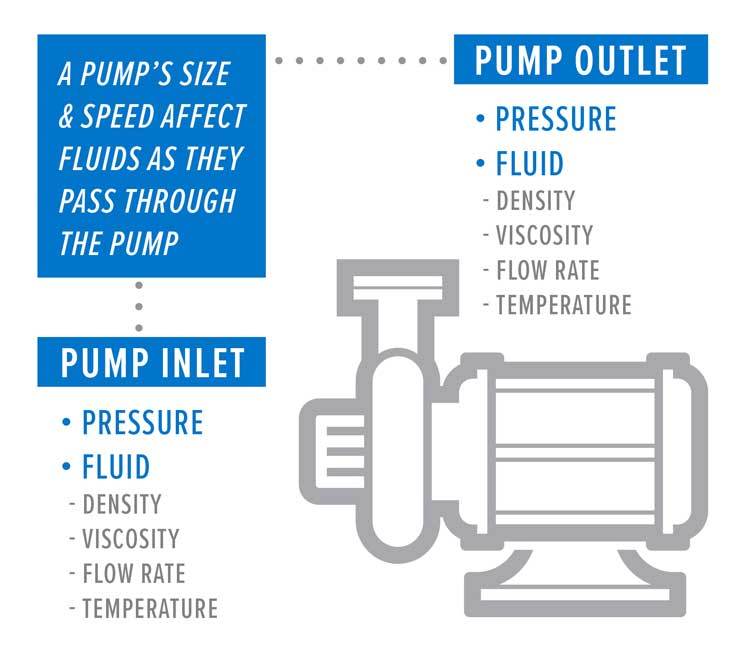
What are the different sizes of pumps available?
When you’re looking to buy a pump, it’s important to consider the size of the pump you need. There are different sizes of pumps available, and each one is designed for a specific purpose. Here are the different sizes of pumps and what they’re used for:
Small pumps are typically used for small objects, such as toys or jewelry.
Medium pumps are usually used for medium objects, such as dolls or furniture.
Large pumps are typically used for large objects, such as water tanks or cars.
Extra-large pumps are typically used for very large objects, such as stadiums or ships.
Conclusion
Finding the right size pump is important for optimizing your pumping experience. To calculate what size pump you need, you’ll need to take into account your breast circumference, nipple width, and bra cup size. Once you have this information, you can use our sizing chart to find the appropriate pump size. If you ever have any questions about which pump size is best for you, don’t hesitate to reach out to our team of experts.
How do I calculate what size pump I need,please click topkitparts see more