Hydraulic pumps are essential for many purposes, but one of the most common uses is for splitting logs. In this article, we’ll discuss the different types of hydraulic pumps and their corresponding requirements, so you can make an informed decision about which pump to buy for your particular application.
What is a hydraulic pump?
A hydraulic pump is an engine that uses pressurized fluid to power a mechanical device. When it comes to log splitting, a hydraulic pump is essential for moving the logs around the splitter. There are a few factors to consider when purchasing a hydraulic pump, such as the horsepower requirement and the size of the machine.
To get started, you first need to figure out what horsepower your machine requires. This can be found on the manufacturer’s website or in the product specifications. Next, you need to determine the size of pump that will fit your machine. Pumps come in different sizes based on their horsepower rating. For example, a pump that has a rating of 50 horsepower will fit machines that require a smaller pump, while a pump with a rating of 200 horsepower will fit machines that require a larger pump.
Once you know the size of pump you need and the horsepower requirement of your machine, you can start shopping for a pump. Try to find a reputable supplier who offers quality pumps at competitive prices. If possible, test drive different pumps before making your purchase. This will help ensure that you get the right pump for your needs.
How does a hydraulic motor work?
A hydraulic motor is a type of electric motor that uses hydraulic pressure to perform work. This pressure is generated by the hydraulic fluid (a liquid or gas) that is kept under high pressure in a reservoir. When the trigger is pulled, the hydraulic fluid is forced through a series of small nozzles to create a high-pressure flow. This flow then acts on a piston inside the engine, which causes it to rotate. The rotation of the piston causes the engine to produce energy, which can be used to power various devices.
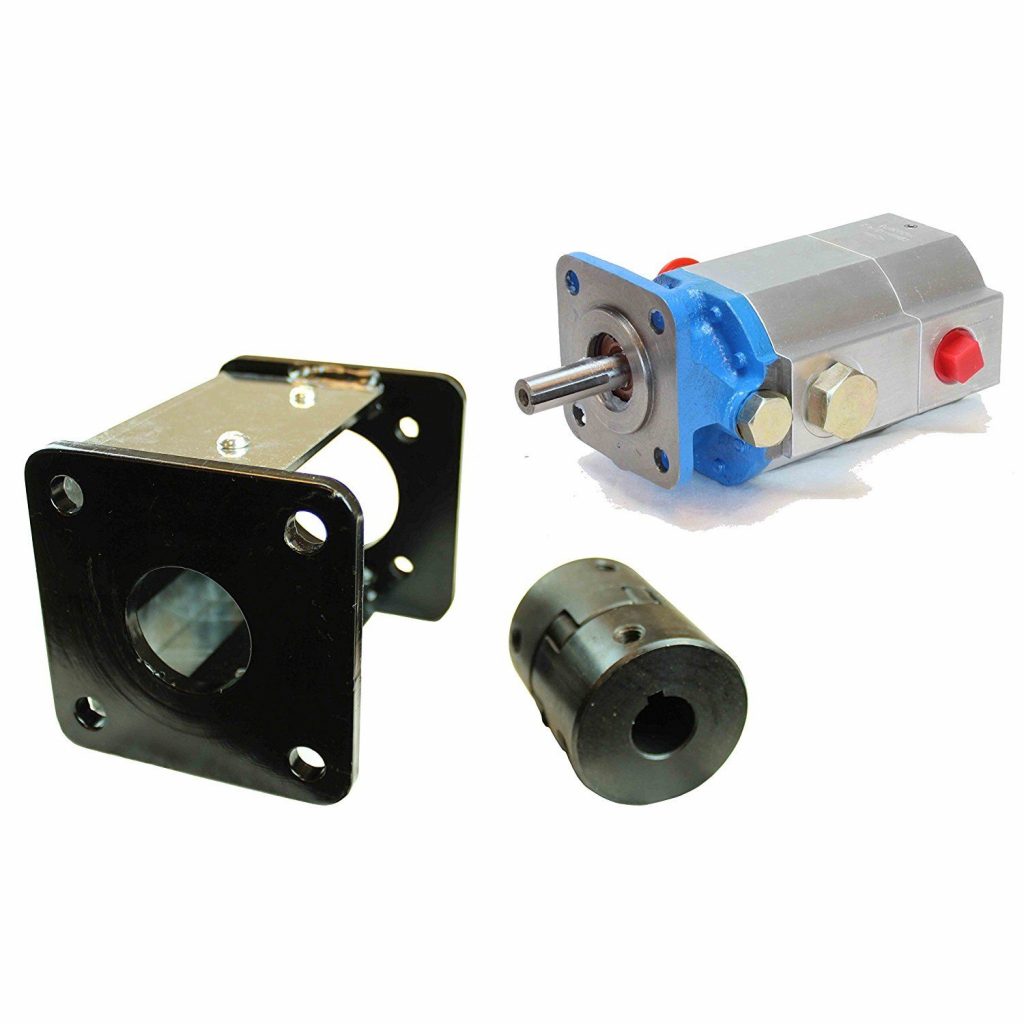
What is a log splitter?
A log splitter is a machine used to split logs into lumber. Most log splitters use hydraulics to do the job. There are many different sizes of hydraulic pumps available for log splitting, so it is important to choose the right one for your machine. Here are some things to consider when choosing a pump:
-The horsepower (or power) of the pump. A higher-power pump will be able to move more water andsplit logs more quickly.
-The type of hydraulic fluid that the pump uses. Some pumps use synthetic fluids, while others use mineral oil. It is important to choose a fluid that is compatible with the pump and the logging machine.
-The size of the logs that the pump can handle. Some log splitters can handle logs up to 12 inches in diameter, while others can only handle logs up to 6 inches in diameter. It is important to check the dimensions of the logs that you will be splitting before you choose a pump.
How to determine the horsepower required for your log splitter
There are a few things you will need to determine in order to figure out what size hydraulic pump you will need for your log splitter.
1. The horsepower required for the machine.
2. The type of wood you will be splitting.
3. The dimensions of the machine.
4. The type of hydraulic fluid you will be using.
5. The installation dimensions of the machine.
6. Other factors that may affect the power requirements, such as the number of splitter blades and auger type used.
Once all these variables have been determined, it is possible to calculate the necessary horsepower for your machine by using one of several formulas available online or in engineering texts. Once the horsepower has been determined, it is easy to find a compatible hydraulic pump by doing a search on the internet or by calling several manufacturers directly.
Why do I need a Hydraulic Log Splitter Pump?
A hydraulic log splitter pump is necessary for splitting logs. The pump recirculates the water through the log and separates the chips from the lumber. There are many factors to consider when selecting the correct size pump for your needs, including the horsepower of your machine, the size of the logs you will be splitting, and the terrain where you will be using the machine.
Choosing a pump that is too large will not result in increased power or efficiency. Conversely, choosing a pump that is too small may result in decreased performance. A good rule of thumb is to select a pump that has at least twice the horsepower of your machine. In addition, choose a pump with an appropriate displacement (volume). This will ensure that enough water can flow through the log to split it properly.
Lastly, consider your intended use location. Pumps with higher capacity are generally more efficient when used on slopes or uneven terrain because they can move more water per revolution. Pumps with lower capacity are more efficient on flat ground or smooth surfaces.
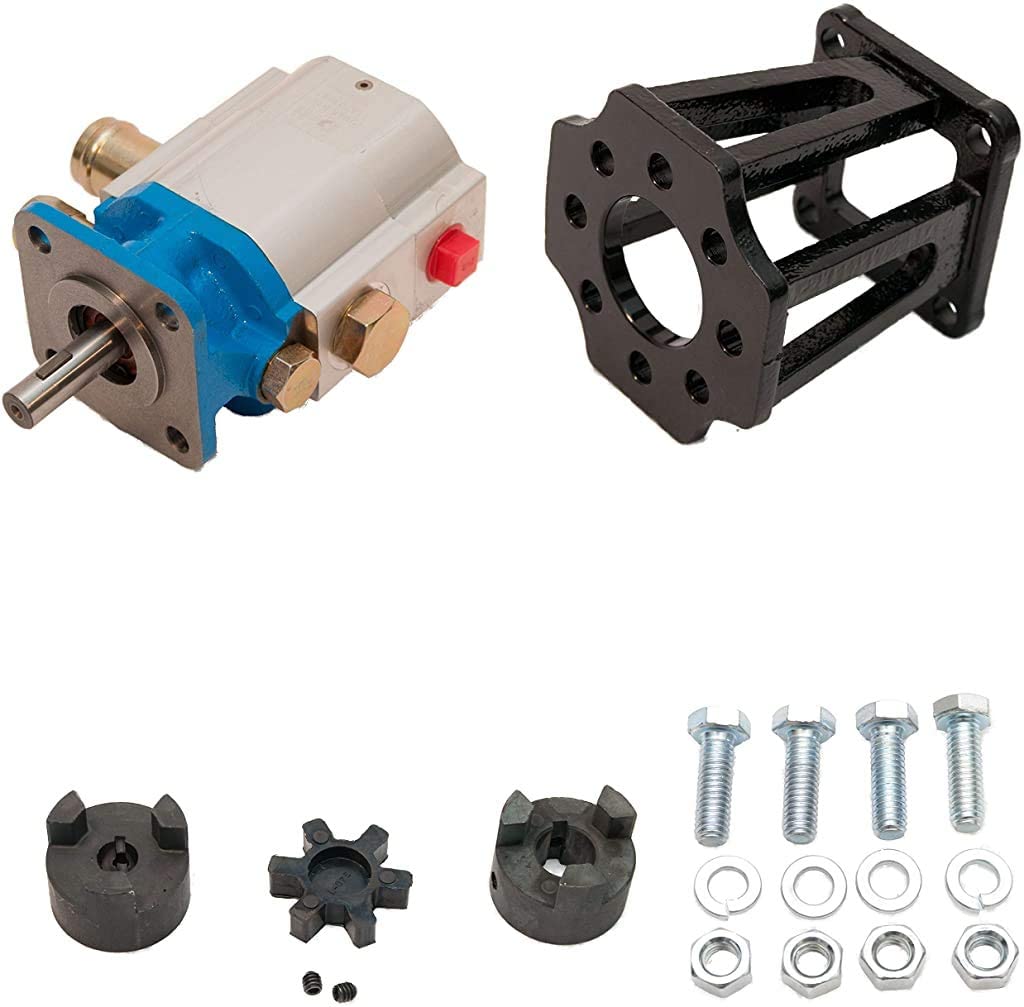
How much horsepower do I need for my log splitting set up?
When it comes to choosing the right size hydraulic pump for your log splitting setup, it’s important to understand how much horsepower your machine will require. Here are a few tips to help you decide:
-The more horsepower your machine has, the larger the pump you’ll need.
-Generally speaking, the more logs your machine will be splitting, the more horsepower you’ll need.
-If you’re splitting logs that are less than 2 inches in diameter, a smaller pump may be sufficient. For larger logs, a larger pump may be necessary.
-Be sure to consult with an expert if you have any doubts about what size pump is necessary for your specific set up.
Checking Log Splitter Hydraulic Pumps Online
If you are looking for a hydraulic pump for your log splitter, there are a few things you should consider. First, you will need to know the horsepower of the machine you plan to buy. Second, you will need to decide how much fluid the pump will require. Finally, you will need to find a size that fits your needs. Here are some general guidelines to help you get started:
-For machines with 1-10 horsepower: A 3/4 HP or smaller pump will work fine.
-For machines with 10-30 horsepower: A 1 HP or smaller pump is recommended.
-For machines with more than 30 horsepower: A 1 1/2 HP or smaller pump is recommended.
Conclusion
If you’re looking to purchase a hydraulic pump for your log splitter, we recommend checking out our selection of pumps. We have a variety of different sizes available, so you can find the perfect one for your needs. If you need any help finding the right size pump, don’t hesitate to reach out to us at our customer service desk.
What size hydraulic pump do I need for a log splitter,please click topkitparts see more