Hydraulic motors are used in a variety of applications such as pumps, water turbines, and agricultural machines. In this article, we will discuss the principles of hydraulic motors and see how you can use a hydraulic pump as a hydraulic motor.
A hydraulic motor is a type of electric motor that uses hydraulic pressure to generate power. The hydraulic pump used as a hydraulic motor operates using the principle of double acting: when the pump piston is in the down position, fluid is forced out of the cylinder and this causes a decrease in pressure in the system; when the piston rises, the increased pressure causes liquid to flow back into the cylinder and this restores the original pressure.
The design of a hydraulic pump makes it an ideal candidate for use as a hydraulic motor. A hydraulic pump can be easily converted from an electric motor to a hydraulic motor by replacing the electric motor components with those that provide for hydraulics.
In general, there are two types of electric motors – synchronous and asynchronous – each with its own advantages and disadvantages. A synchronous electric motor operates with both coils spinning at the same speed and this results in high efficiency because power is delivered continuously. However, synchronous motors are less tolerant of disturbances such as faults or overloads, so they are not suitable for applications where reliability is critical. Asynchronous electric motors operate with one coil spinning faster than the other, which results in decreased efficiency but increased tolerance to disturbances.
What is a hydraulic pump?
A hydraulic pump is a machine that uses pressurized fluid to move objects or fluids. A hydraulic motor is an engine that uses a hydraulic pump as its working mechanism.
How does a hydraulic pump work?
When you turn the handle on a traditional gasoline engine, the pistons move up and down, pushing and pulling air and fuel mixture into and out of the cylinders. This moving air and fuel mixture is what makes the engine run. In a hydraulic pump, pressurized fluid moves the same way. The pistons are surrounded by a sealed cylinder filled with pressurized fluid. When you pull on the handle, the pressure in the cylinder forces the fluid through the pistons. That’s how a hydraulic motor works.
What is a hydraulic motor good for?
A hydraulic motor can be used in many different applications. Some of them are:
-Pumps for water, oil, or gas
-Rotating machines, such as fan blades or propellers
-Agricultural equipment
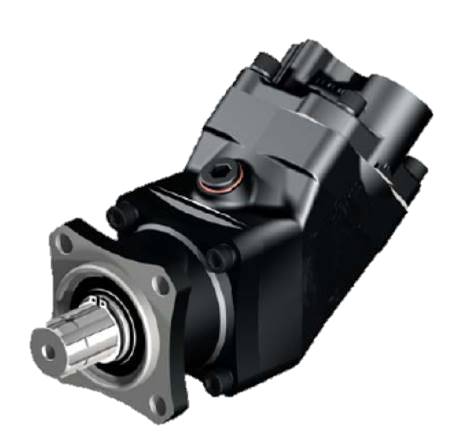
How does a hydraulic pump work?
A hydraulic pump is a type of piston engine that uses the fluid pressure of hydraulics to power the engine. The fluid is usually oil, but it can also be water, air, or even natural gas. When you press down on a plunger in a hydraulic pump, the fluid pressure inside the pump causes a rotating shaft to rotate. This rotation then turns the gears on the pump, which in turn drives the piston or pistons in the engine.
A hydraulic pump is a versatile engine type that can be used for a variety of applications. Some of the most common uses for a hydraulic pump are in pumps for water, oil, and gas, rotating machines, and agricultural equipment.
What is a Hydraulic Motor?
A hydraulic motor is a type of motor that uses hydraulic power to create motion. Hydraulic motors are often used in industrial applications, such as in machine tools and construction equipment, because they are efficient and reliable. They work by using the pressure of water or other liquids to generate motion.
The most common type of hydraulic motor is the direct-drive hydraulic motor. This type of motor uses a gearbox to convert the rotational motion of a shaft into linear motion in a hydraulic fluid. The fluid then power the motor’s rotor, which in turn creates the mechanical power needed to move the machine.
How does a Hydraulic Motor work?
A hydraulic motor is a device that uses pressurized hydraulic fluid to move an object. The hydraulic fluid is usually oil, but it can also be water or other liquids. The pressure in the hydraulic fluid causes the objects to move. Hydraulic motors are used in a variety of applications, including construction, mining, farming, and manufacturing.
The basic principle behind a hydraulic motor is simple. When you apply pressure to liquid, it moves. In a hydraulic motor, this pressure is created by the flow of hydraulic fluid through the motor. The fluid flows through a series of pipes and chambers, which create a high pressure in the system. This high pressure is used to move the object.
In most cases, the hydraulic fluid is pressurized by an electric pump. This pump provides the necessary energy to create the high pressure in the system. When you depress the trigger on a hydraulic pump, this high pressure is released in a continuous stream. This stream of pressurized fluid travels through the motor and moves the object.
The Difference Between a Hydraulic Motor and a Hydraulic Pump
A hydraulic motor is a device that uses hydraulic pressure to create movement. A hydraulic pump, on the other hand, is a device that uses pressurized fluid to move objects. Most often, a hydraulic motor is connected to a hydraulic pump in order to power an object or system.
One common use for a hydraulic motor is in vehicles. Hydraulic motors are often used to power various parts of the vehicle, including the engine, brakes, and steering.
Another common use for a hydraulic motor is in construction. Hydraulic motors are often used in construction vehicles to move objects, such as concrete and rocks.
Overall, a hydraulic motor is more powerful than a hydraulic pump. A hydraulic pump can only move small objects, while a hydraulic motor can move much larger objects.
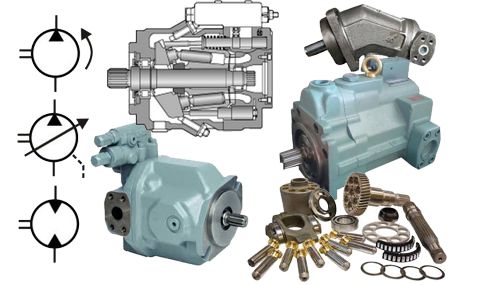
What are the advantages and disadvantages of using a hydraulic pump as a motor?
The main advantage to using a hydraulic pump as a motor is the low cost. A hydraulic pump can be purchased for relatively little money, and there is no need for additional equipment or wiring. Additionally, a hydraulic pump can be easily modified to create a motor. The disadvantage to using a hydraulic pump as a motor is that the power output is limited. A hydraulic pump can only produce a certain amount of power, which may not be enough to power a large machine orvehicle.
Does the hydraulic pump work as a hydraulic motor or not?
The hydraulic pump can be used as a hydraulic motor, but it will not work as effectively as a regular motor. It is important to note that the pump is only effective when using water or other fluid as the medium. If using oil, the pump will not work.
Conclusion
Yes, you can use a hydraulic pump as a hydraulic motor. A hydraulic pump is an application-specific machine that uses pressurized fluid to do work. By using the right type of oil and bearing, you can create a rotating motion using the power of the hydraulic pump.
Can I use a hydraulic pump as a hydraulic motor,please click topkitparts see more