You’ve probably heard the term “pump capacity” before, and you might be wondering what it actually means. In this article, we’re going to take a look at pump capacity and see how you can increase it. By doing this, you’ll be able to handle more water without having to switch to a bigger pump.
What pumps are and how do they work?
If you are looking for a pump to increase your capacity and want to know more about pumps, this is the article for you. Pumps come in all shapes, sizes, and prices. Some pumps come with multiple functions, while others are just for pumping. Here we will take a look at a few pumps and their capabilities.
Pump Overview:
A pump is a machine that uses energy to move fluid or gas through a system. There are many different types of pumps, but they all have one common goal: to increase the flow of something. Pumps can be mechanical or electrical, and they come in various sizes and capacities.
Some pumps are specifically designed to increase the flow of liquids or gases. These pumps are called centrifugal pumps, because their principle function is to create centrifugal force. Centrifugal pumps are used for things like washing machines and air conditioning units, because they can quickly move large volumes of fluid around the machine.
Pump Usage:
There are many different applications for pumps, but some of the most common uses include:
-Moving water or gas through pipelines or tanks
-Pumping oil or gas out of wells
-Compressing air or
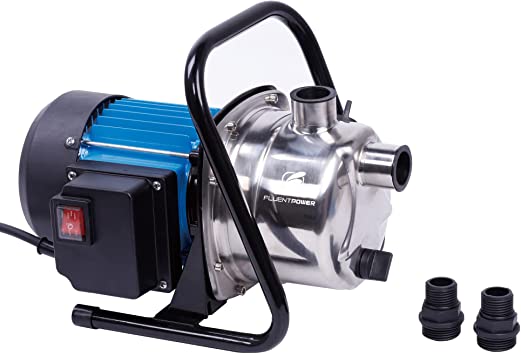
What is pump capacity?
Pump capacity is the maximum amount of fluid that a pump can move in a specific time period. It is determined by the pump’s motor and impeller size, as well as the size and type of fluid being pumped. Pump capacity is important because it affects how quickly a pump can move fluid and how much work it will do.
There are several ways to increase your pump capacity. One way is to upgrade the motor and impeller size. Another way to increase your pump’s capacity is to increase the size or type of fluid being pumped. You can also improve your pumping process by using better hydraulic fluids and fittings, or by increasing the efficiency of your pumping system.
What is the pump capacity?
When you are reading this, you probably want to know how to increase your pump capacity. And the answer is that there is no single answer to this question since the pump capacity depends on the pump, the application, and the user. However, here are a few tips that can help you increase your pump capacity:
1. determinethe type of pump you have: If you have a centrifugal or reciprocating pump, your pump capacity will be based on its design. However, if you have a pusher/drum pump, your pump capacity will be based on its stroke volume (how much it can push or discharge per revolution). So if you need to increase your pump capacity, identify which type of pump you have and work from there.
2. knewo what size you need: Many times when people need to increase their pump capacity, they don’t realize it until they get their hands on the equipment and start measuring things. The best way to find out is to measure your current pumping requirements and see if those requirements match up with what the manufacturer recommends for the size of your pump. This way, you’ll avoid buying something that won’t work for your application.
Benefits of increased pump capacity
There are many benefits to increasing pump capacity, including increased safety and efficiency. Increased pump capacity can also help you to produce more milk faster, which can be beneficial for both you and your baby. Here are some of the most common benefits of increased pump capacity:
1. Increased Safety: A larger pump will generally work more efficiently, meaning that it will produce less waste and heat. This means that your pump will be less likely to overheat and give you a dangerous electric shock.
2. Increased Efficiency: A larger pump will also be able to move more milk per cycle, meaning that it will spend less time working and more time producing milk. This can lead to increased milk production rates and decreased waste.
3. Faster Milk Production: A larger pump can also move more milk per stroke, which can lead to faster milk production rates. Faster milk production is often desired by breastfeeding mothers who want to increase their supply as quickly as possible.
4. Greater Comfort: A larger pump can often be more comfortable to use, due to its greater size and design. This can lead to a smoother experience for you and reduced pain during pumping sessions.
5. Reduced Fatigue: A large pump can
Factors affecting pump capacity
Factors that can affect pump capacity include the size and shape of the pump, the type of fluid being pumped, and how well the pump is maintained. In general, larger pumps are more likely to be able to handle larger volumes of fluid, while smaller pumps may be better suited for pumping smaller volumes of fluid. Additionally, a well-maintained pump will be able to operate more effectively and efficiently.
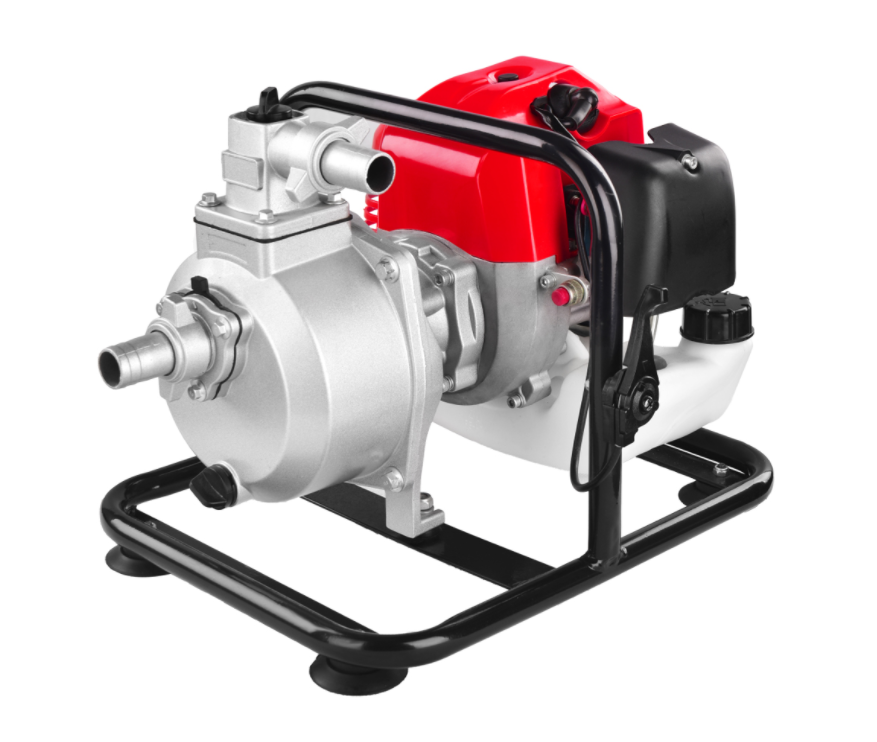
Causes of Low Pump Capacity
There are a few common causes of low pump capacity, and each can be addressed in a different way.
1. Iron deficiency
Iron is an essential mineral that helps your body produce energy. If you’re not getting enough iron, your body will have a harder time producing energy from food, which can eventually lead to low pump capacity. Talk to your doctor if you’re concerned about your iron levels and see if there’s anything you can do to increase your intake.
2. Low muscle mass
If you don’t have enough muscle mass, your pump capacity will be decreased. Muscle cells use energy to contract, which results in the production of blood flow and hormones. If you don’t have enough muscle mass, your pump capacity will be decreased. To increase your muscle mass, start working out regularly and eat a balanced diet that includes plenty of protein.
3. Poor circulation
If your circulation is poor, blood flow will be reduced in many areas of the body, including the muscles. To improve circulation, exercise regularly and eat a balanced diet that includes plenty of fruits and vegetables. Additionally, try using natural supplements like fresh ginger or garlic to improve circulation.
What can I do to increase my pump capacity?
There are a few things that you can do to increase your pump capacity. One of the most common ways to do this is to increase the amount of weight that you are lifting. You can also try changing up your workout routine or adding more cardio workouts. Additionally, you can try using different types of pumps throughout the day to help boost your production.
Conclusion
If you are looking to increase your pump capacity, there are a few things that you can do. First, make sure that your workout routine is intense but not too hard. Second, make sure that you are taking in enough water and electrolytes during your workouts. Third, try using supplements such as nitric oxide boosters or creatine to help increase your pump capacity. Finally, make sure to eat a balanced diet full of nutritious foods that will help support muscle growth and recovery.
How do I increase my pump capacity,please click topkitparts see more