radial hydraulic pumps are a type of pump that have been around for many years and are used in a variety of applications. They are commonly used in water treatment plants, for extracting oil and gas from the ground, and for providing water to power plants. In this article, we will learn about the different types of radial hydraulic pumps, their advantages and disadvantages, and the factors that determine their suitability for a specific application.
Radial hydraulic pumps are a type of hydraulic pump that uses the radial flow principle. This means that the fluid is propelled radially outward from the pump’s impeller. The radial flow principle is often used in applications where large amounts of liquid or gas are required to be moved quickly and efficiently.
Advantages of radial hydraulic pumps
Radial hydraulic pumps have a number of advantages over other types of hydraulic pumps. These include:
They are often faster than other types of pumps and can move larger quantities of fluid more quickly. This makes them ideal for applications where speed is important, such as in water treatment plants or power plants.
They are less expensive to operate than other types of pumps. This makes them a good choice for applications where cost is an important factor, such as oil extraction or water supply.
They are less likely to suffer from cavitation, which is a phenomenon that can lead to the pump’s impeller blades becoming damaged. Cavitation is often caused by liquid being forced into small gaps between the pump’s blades and can cause the blades to break. Radial hydraulic pumps are less likely to experience cavitation due to their radial flow principle.
They are better at handling highpressure fluids than other types of pumps. This makes them ideal for applications where high pressures are required, such as in oil extraction or water treatment plants.
They are more resistant to wear and tear than other types of pumps. This means that they will last longer and require less maintenance than other types of pumps
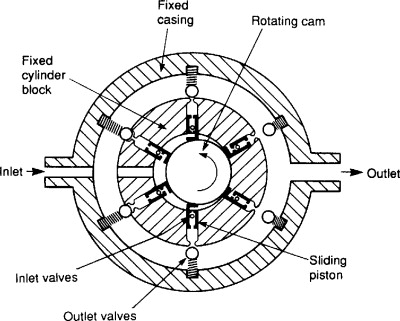
How does a radial hydraulic pump work?
radial hydraulic pumps are used in a variety of industries to move fluids and gases. The rotating impeller causes the fluid to be expelled through the pump’s discharge nozzle. This type of pump is efficient because it uses less energy than other types of pumps, making it a popular choice for industrial applications.
The radial hydraulic pump operates on the principle of Bernoulli’s equation. This equation states that the pressure difference across a fluid flow is inversely proportional to the square of the velocity difference. This means that as the velocity of the fluid decreases, the pressure will also decrease. This is why radial hydraulic pumps are typically more efficient than other types of pumps when it comes to moving fluids and gases.
What are the different types of radial hydraulic pumps?
Radial hydraulic pumps are a type of piston pump that use fluid to move objects or materials. They come in different types, including rotary and reciprocating, and can be used in a variety of applications.
Rotary radial hydraulic pumps use a spinning rotor to create a rotating force that moves the fluid. This type is often used in industrial settings to move large objects or liquids.
Reciprocating radial hydraulic pumps use pistons to push and pull the fluid, which causes it to move forward. They’re often used in construction settings to move concrete or other heavy objects.
If you need help choosing the right radial hydraulic pump for your application, contact a professional supplier like SKF. We have years of experience selecting the right pump for each situation, so we can help you find the perfect pump for your needs.
How is a radial hydraulic pump used?
A radial hydraulic pump is a type of hydraulic pump that uses a rotating cylinder to transfer fluid from one chamber to another. The cylinder has a series of grooves that act as chambers, and the pump transfers the fluid by using a plunger to move the liquid along the grooves. This action creates a force that helps move objects or fluids.
What are the advantages of using a radial hydraulic pump?
Radial hydraulic pumps offer a number of advantages over other types of hydraulic pumps. These include:
-They are typically more efficient than other types of pumps, meaning that they use less energy to move the same amount of fluid.
-They are able to operate at higher pressures than other types of pumps, which means they can handle greater volumes of fluid.
-They are usually less expensive than other types of pumps, making them a good option for smaller businesses or projects that don’t need the highest possible performance.
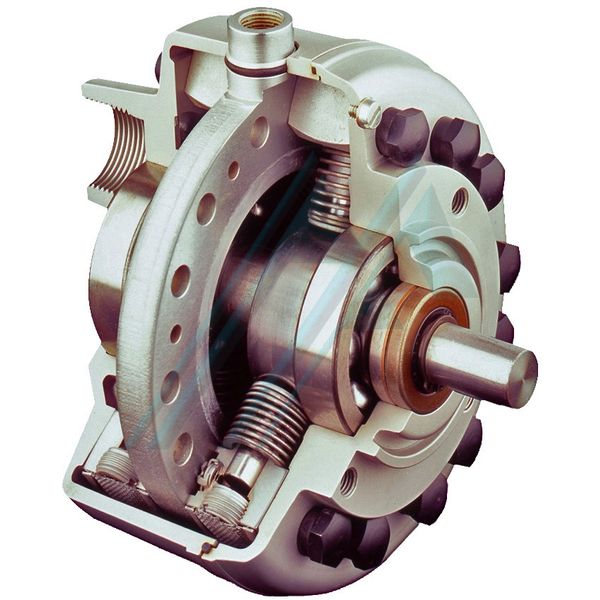
What are the disadvantages of using a radial hydraulic pump?
radial hydraulic pumps are often used in mining and civil engineering applications. They offer high performance and reliability, but they can also be expensive. Here are some of the disadvantages of using a radial hydraulic pump:
-They require more space than other types of pumps.
-They can be noisy.
-They can be difficult to install and maintain.
Who uses a radial hydraulic pump?
radial hydraulic pumps are used in many different industries. They are especially popular in the agricultural and construction industries. radial hydraulic pumps are affordable and efficient, making them a popular choice for small businesses and home repairs.
radial hydraulic pumps are used in many different industries. They are especially popular in the agricultural and construction industries. radial hydraulic pumps are affordable and efficient, making them a popular choice for small businesses and home repairs.
Conclusion
A radial hydraulic pump is a type of pump used in fluidic systems to move fluids. The main purpose of a radial hydraulic pump is to transfer the desired amount of fluid from one point to another, using an impeller to create a rotational motion. These pumps are commonly used in manufacturing and processing plants, as well as other industrial settings where high volumes of fluid are moved at low pressure or temperatures.
What is a radial hydraulic pump,please click topkitparts see more